Contact Details
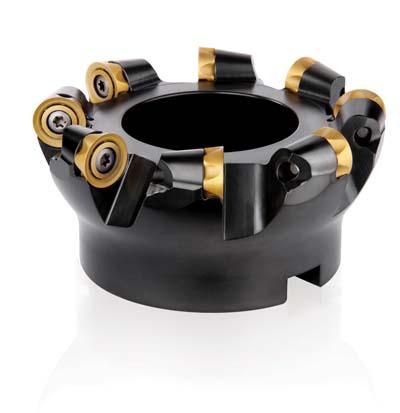
The KSRM line of cutters is a new, multipurpose milling solution from Kennametal specifically engineered for titanium and stainless steel applications. Their design enables pocketing, profiling, ramping, and plunging with up to 1mm fz. KSRM milling cutters deliver consistent performance and excellent metal removal rates with the lowest cutting forces for roughing applications.
All KSRM inserts offer up to eight indexable positions for fast and accurate insert changes. These inserts were designed with a high positive rake angle and stronger cutting edges for lower cutting forces when machining titanium.
KSRM inserts are available in 12mm and 16mm diameters for KSRM face mills and screw-on, Weldon and cylindrical KSRM end mills. These diameters are offered in SGE and ELE insert styles, which are the first choice for titanium applications. SGE inserts are designed for medium and heavy milling tasks, whereas ELE inserts should be used at low cutting forces and to avoid edge build-up.
A 20mm diameter insert is also available for compatible KSRM face mill models. These inserts are offered in three styles. ELF inserts are designed for low cutting forces to avoid edge build-up. SGF and SHF inserts are for general purpose and heavy-duty roughing applications, respectively.
KSRM tool bodies are offered in a range of internally cooled face mill and end mill styles with pocketing, ramping, plunging, and helical interpolation capabilities. All are designed with a high clearance for superior plunging, ramping, and chip load capacities. An anti-rotation screw delivers excellent stability with higher feed rates and cutting forces. The anti-rotation components also provide eight indexable positions for 12mm and 16mm inserts. Face mills utilizing 20mm inserts are engineered for roughing titanium with large depths of cut through positive geometry inserts. These mills allow six indexable rotations and are used for diameters from 60mm to 200mm.
Related Glossary Terms
- clearance
clearance
Space provided behind a tool’s land or relief to prevent rubbing and subsequent premature deterioration of the tool. See land; relief.
- feed
feed
Rate of change of position of the tool as a whole, relative to the workpiece while cutting.
- gang cutting ( milling)
gang cutting ( milling)
Machining with several cutters mounted on a single arbor, generally for simultaneous cutting.
- interpolation
interpolation
Process of generating a sufficient number of positioning commands for the servomotors driving the machine tool so the path of the tool closely approximates the ideal path. See CNC, computer numerical control; NC, numerical control.
- milling
milling
Machining operation in which metal or other material is removed by applying power to a rotating cutter. In vertical milling, the cutting tool is mounted vertically on the spindle. In horizontal milling, the cutting tool is mounted horizontally, either directly on the spindle or on an arbor. Horizontal milling is further broken down into conventional milling, where the cutter rotates opposite the direction of feed, or “up” into the workpiece; and climb milling, where the cutter rotates in the direction of feed, or “down” into the workpiece. Milling operations include plane or surface milling, endmilling, facemilling, angle milling, form milling and profiling.
- milling machine ( mill)
milling machine ( mill)
Runs endmills and arbor-mounted milling cutters. Features include a head with a spindle that drives the cutters; a column, knee and table that provide motion in the three Cartesian axes; and a base that supports the components and houses the cutting-fluid pump and reservoir. The work is mounted on the table and fed into the rotating cutter or endmill to accomplish the milling steps; vertical milling machines also feed endmills into the work by means of a spindle-mounted quill. Models range from small manual machines to big bed-type and duplex mills. All take one of three basic forms: vertical, horizontal or convertible horizontal/vertical. Vertical machines may be knee-type (the table is mounted on a knee that can be elevated) or bed-type (the table is securely supported and only moves horizontally). In general, horizontal machines are bigger and more powerful, while vertical machines are lighter but more versatile and easier to set up and operate.
- profiling
profiling
Machining vertical edges of workpieces having irregular contours; normally performed with an endmill in a vertical spindle on a milling machine or with a profiler, following a pattern. See mill, milling machine.
- rake
rake
Angle of inclination between the face of the cutting tool and the workpiece. If the face of the tool lies in a plane through the axis of the workpiece, the tool is said to have a neutral, or zero, rake. If the inclination of the tool face makes the cutting edge more acute than when the rake angle is zero, the rake is positive. If the inclination of the tool face makes the cutting edge less acute or more blunt than when the rake angle is zero, the rake is negative.