Contact Details
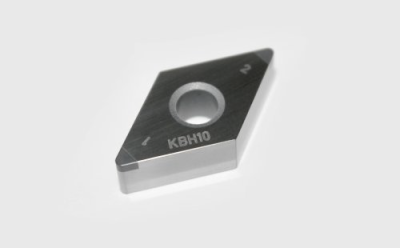
KBH10 is an uncoated PCBN turning insert that offers exceptional wear resistance and very low cutting forces. As a result, many customers are now enjoying double the tool life together with improved part quality.
Hard turning has been used for decades to streamline and in many cases eliminate cylindrical grinding operations. It’s fast, accurate, and thanks to tooling suppliers such as Kennametal, a broad assortment of predictable, cost-effective cutting tools is available to tame even the mos tdifficult hardened steels, superalloys, and chilled irons. But as the aerospace, automotive, power generation, and other industries continue to develop even more robust metals, cutting tool manufacturers must evolve as well with high-performance tooling to tackle these materials.
That’s what Kennametal Inc. has accomplished recently with its introduction of KBH10, a PCBN hard turning insert designed specifically for the challenges of today’s demanding market place. Helmut Gremer, senior engineer for global machining technology, says the new insert complements Kennametal’s existing PCBN grades KBH20 and KB5630 by providing the extreme wear resistance needed to successfully turn hardened metals up to 65 HRC, especially where very fine surface finishes are required.
“We’ve seen that many manufacturers are decreasing the allowable tolerances on bearing journals, rings and pistons, gear hubs, and so on,” he says. “For example, dimensional tolerances of less than 4 μm or less are increasingly common, as are surface requirements better than Ra 0.4 μm. This new grade closes the gap for these and other customers that need superior tool life when finishing such parts.”
In one example, a well-known automotive manufacturer was able to more than double tool life—from 150 pieces per edge to 350 pieces—during an internal facing operation on a 140 mm (5.5 in.) diameter 5115 alloy steel bearing hub that was previously heat-treated to 62 HRC. And a driveshaft producer achieved similar results, increasing tool life from 250 to 450 pieces per edge when turning 58 HRC UC1 (similar to S53) steel on its vertical turret lathes, consistently maintaining a 6 Rz surface finish while doing so.
In each instance, cutting speeds of 180 m/min were used (590 sfm), with depths of cut averaging 0.15 mm (0.006 in.) and feed rates ranging from 0.22 to 0.32 mm per rev (0.0087 to 0.013 ipr). Also in each case, the customer saved thousands of dollars annually in insert costs compared to its existing solution, while substantially reducing downtime due to tool changeovers.
The KBH10 substrate is completely new. Its PCBN composition is designed for up to 20-percent higher cutting speeds while providing equivalent or in some cases far greater tool life. Kennametal engineers were frequently able to achieve Ra 0.2 and Rz 1 surface roughness, while consistently maintaining the profile and dimensional tolerances noted earlier. KBH10 is available in several different geometries and edge preparations.
“KBH10 is ideally suited for fine-finishing operations yet is tough enough to handle light interruptions or varying depth of cut operations,” says Gremer. “And because cutting pressure and therefore heat is reduced, crater and flank wear are likewise reduced, extending tool life. There’s also a lower occurrence of the white layer that plagues many hard part machining operations.”
This last part is accomplished through KBH10’s unique edge preparation. Rather than the traditional waterfall or radiused hone applied to virtually all PCBN cutting tools, Kennametal has developed a special shape that is both sharper and freer cutting than competing solutions yet still tough enough to withstand the rigors of hard turning.
“Five years ago, no one was able to generate edges like this, let alone measure them,” Gremer explains. “But thanks to some fairly recent advances in metrology and machine tool technology, we can consistently produce this hone shape, which reduces passive cutting forces by up to 40 percent. Together with KBH10’s tougher substrate—also new—we’ve produced an insert that achieves a fine balance between wear-resistance, hardness and sharpness.
Related Glossary Terms
- cylindrical grinding
cylindrical grinding
Grinding operation in which the workpiece is rotated around a fixed axis while the grinding wheel is fed into the outside surface in controlled relation to the axis of rotation. The workpiece is usually cylindrical, but it may be tapered or curvilinear in profile. See centerless grinding; grinding.
- depth of cut
depth of cut
Distance between the bottom of the cut and the uncut surface of the workpiece, measured in a direction at right angles to the machined surface of the workpiece.
- edge preparation
edge preparation
Conditioning of the cutting edge, such as a honing or chamfering, to make it stronger and less susceptible to chipping. A chamfer is a bevel on the tool’s cutting edge; the angle is measured from the cutting face downward and generally varies from 25° to 45°. Honing is the process of rounding or blunting the cutting edge with abrasives, either manually or mechanically.
- feed
feed
Rate of change of position of the tool as a whole, relative to the workpiece while cutting.
- flank wear
flank wear
Reduction in clearance on the tool’s flank caused by contact with the workpiece. Ultimately causes tool failure.
- grinding
grinding
Machining operation in which material is removed from the workpiece by a powered abrasive wheel, stone, belt, paste, sheet, compound, slurry, etc. Takes various forms: surface grinding (creates flat and/or squared surfaces); cylindrical grinding (for external cylindrical and tapered shapes, fillets, undercuts, etc.); centerless grinding; chamfering; thread and form grinding; tool and cutter grinding; offhand grinding; lapping and polishing (grinding with extremely fine grits to create ultrasmooth surfaces); honing; and disc grinding.
- hard turning
hard turning
Single-point cutting of a workpiece that has a hardness value higher than 45 HRC.
- hardness
hardness
Hardness is a measure of the resistance of a material to surface indentation or abrasion. There is no absolute scale for hardness. In order to express hardness quantitatively, each type of test has its own scale, which defines hardness. Indentation hardness obtained through static methods is measured by Brinell, Rockwell, Vickers and Knoop tests. Hardness without indentation is measured by a dynamic method, known as the Scleroscope test.
- metrology
metrology
Science of measurement; the principles on which precision machining, quality control and inspection are based. See precision machining, measurement.
- polycrystalline cubic boron nitride ( PCBN)
polycrystalline cubic boron nitride ( PCBN)
Cutting tool material consisting of polycrystalline cubic boron nitride with a metallic or ceramic binder. PCBN is available either as a tip brazed to a carbide insert carrier or as a solid insert. Primarily used for cutting hardened ferrous alloys.
- superalloys
superalloys
Tough, difficult-to-machine alloys; includes Hastelloy, Inconel and Monel. Many are nickel-base metals.
- turning
turning
Workpiece is held in a chuck, mounted on a face plate or secured between centers and rotated while a cutting tool, normally a single-point tool, is fed into it along its periphery or across its end or face. Takes the form of straight turning (cutting along the periphery of the workpiece); taper turning (creating a taper); step turning (turning different-size diameters on the same work); chamfering (beveling an edge or shoulder); facing (cutting on an end); turning threads (usually external but can be internal); roughing (high-volume metal removal); and finishing (final light cuts). Performed on lathes, turning centers, chucking machines, automatic screw machines and similar machines.
- wear resistance
wear resistance
Ability of the tool to withstand stresses that cause it to wear during cutting; an attribute linked to alloy composition, base material, thermal conditions, type of tooling and operation and other variables.