Contact Details
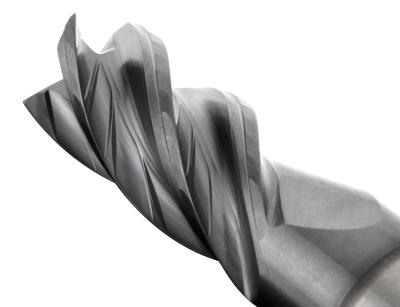
Kennametal announced the latest addition to its HARVI line of high-performance solid endmills, the HARVI I TE 4-flute solid-carbide endmill. With a radical new design, the HARVI I TE delivers outstanding performance in a broad range of materials, including steel, stainless steel, high-temperature alloys and cast iron. And thanks to significantly reduced cutting forces, this tool can be used on any machining center or mill/turn center in the shop.
“The HARVI I TE consistently outperformed competing four-flute end mills in both wet and dry machining tests on a variety of materials and applications, with unprecedented tool life in many cases,” said Bernd Fiedler, manager, solid endmilling. “It performs exceptionally well on heavy roughing and finishing cuts alike – from deep cavities and full width slots to shoulder and dynamic milling.”
Kennametal engineers designed the HARVI I TE to address four key problems that plague more than 90% of all milling applications: chip evacuation, tool deflection, corner stability and breakage due to radial cutting forces. The result is a tool that’s durable and versatile enough to tackle the lion’s share of milling applications.
Consider chip evacuation. The HARVI I TE has an innovative flute design that helps curl and break chips into manageable pieces, while a series of chip gashes within the flute lift those chips up and away from the workpiece. Both serve to promote coolant flow, eliminate chip re-cutting, and improve tool life. A twisted end face and unique gashing further promote chip evacuation but are also responsible for the HARVI I TE’s enhanced ramping and plunging capabilities.
Tool deflection is reduced thanks to the tool’s parabolic core, as well as an eccentric, faceted relief along the entire flute length that significantly lowers cutting friction. This relief also increases edge strength, making the tool a versatile solution. Together with a variable-helix angle and asymmetric flutes it dampens vibration before it can negatively affect machining operations.
“The HARVI I TE improves process stability, surface quality and chip evacuation,” Fiedler said. “Most importantly, it maintains these benefits even at increased feeds, speeds, and depths of cut – delivering maximum metal removal, tool life and productivity.”
Related Glossary Terms
- alloys
alloys
Substances having metallic properties and being composed of two or more chemical elements of which at least one is a metal.
- coolant
coolant
Fluid that reduces temperature buildup at the tool/workpiece interface during machining. Normally takes the form of a liquid such as soluble or chemical mixtures (semisynthetic, synthetic) but can be pressurized air or other gas. Because of water’s ability to absorb great quantities of heat, it is widely used as a coolant and vehicle for various cutting compounds, with the water-to-compound ratio varying with the machining task. See cutting fluid; semisynthetic cutting fluid; soluble-oil cutting fluid; synthetic cutting fluid.
- endmill
endmill
Milling cutter held by its shank that cuts on its periphery and, if so configured, on its free end. Takes a variety of shapes (single- and double-end, roughing, ballnose and cup-end) and sizes (stub, medium, long and extra-long). Also comes with differing numbers of flutes.
- endmilling
endmilling
Operation in which the cutter is mounted on the machine’s spindle rather than on an arbor. Commonly associated with facing operations on a milling machine.
- flutes
flutes
Grooves and spaces in the body of a tool that permit chip removal from, and cutting-fluid application to, the point of cut.
- gang cutting ( milling)
gang cutting ( milling)
Machining with several cutters mounted on a single arbor, generally for simultaneous cutting.
- machining center
machining center
CNC machine tool capable of drilling, reaming, tapping, milling and boring. Normally comes with an automatic toolchanger. See automatic toolchanger.
- milling
milling
Machining operation in which metal or other material is removed by applying power to a rotating cutter. In vertical milling, the cutting tool is mounted vertically on the spindle. In horizontal milling, the cutting tool is mounted horizontally, either directly on the spindle or on an arbor. Horizontal milling is further broken down into conventional milling, where the cutter rotates opposite the direction of feed, or “up” into the workpiece; and climb milling, where the cutter rotates in the direction of feed, or “down” into the workpiece. Milling operations include plane or surface milling, endmilling, facemilling, angle milling, form milling and profiling.
- relief
relief
Space provided behind the cutting edges to prevent rubbing. Sometimes called primary relief. Secondary relief provides additional space behind primary relief. Relief on end teeth is axial relief; relief on side teeth is peripheral relief.