Contact Details
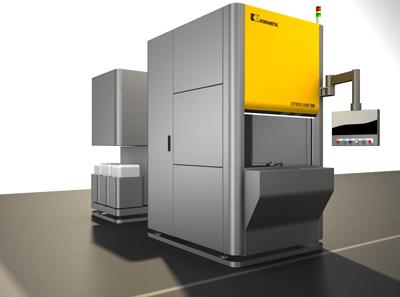
Manufacturers and quality professionals requiring high-precision components such as automotive fuel systems and powertrains are under constant pressure to deliver the utmost quality efficiently. Consequently, Kennametal Precision Surface Solutions is announcing Extrude Hone EVO, the next generation of electrochemical machining solutions featuring proprietary generator technology delivering from 3kW to 100kW power depending on machine configuration.
"Additionally, EVO delivers another exclusive added value: electrochemical machining without stray machining attack," says Bruno Boutantin, Kennametal Precision Surface Solutions global marketing manager. "Customers will enjoy the highest surface finish quality for improved component performance."
ECM is used in contouring, radiusing, polishing, deburring, and flow tuning applications. Essentially, ECM is a subtractive method that works on the principle of anodic metal dissolution. Each part to be machined requires a cathode (-) for selective material removal on the workpiece (+). The cutting speed is equal to the DC current applied to the part. The lack of contact between the tool (-) and the workpiece (+) is important. An electrolyte solution (NaCl or NaNO3 in water or glycol base) handles charge transfer in the working gap. The resulting electron current releases metal ions from the workpiece. The amount of material removed is defined by Faraday's Law (equivalent to current x cycle time). Using the electrolyte, the removed material is flushed out of the gap as a hydroxide. This must be captured by an adequate filter system to maintain constant electrolyte conditions. There will be a constant gap, resulting in proper tooling and cathode life. The shape of the tool cathode determines the shape of the material removal. ECM's main benefits of this process are:
-Targeted material removal in precise locations
-No mechanical or thermal stress
-Process stability
-High productivity
EXTRUDE HONE EVO is available in various standard layouts: single or dual cell, or even in multi-cell configurations thanks to the system's modular design and construction. It is easy to configure and easy to integrate into modern production lines. For customers looking for specific machining operations, the machine integrates an interface for Dynamic ECM.
Reliability being at the heart of the production control requirements, EVO provides for online monitoring and control of all relevant parameters. The online feature is also beneficial in delivering remote process demonstrations.
Related Glossary Terms
- cutting speed
cutting speed
Tangential velocity on the surface of the tool or workpiece at the cutting interface. The formula for cutting speed (sfm) is tool diameter 5 0.26 5 spindle speed (rpm). The formula for feed per tooth (fpt) is table feed (ipm)/number of flutes/spindle speed (rpm). The formula for spindle speed (rpm) is cutting speed (sfm) 5 3.82/tool diameter. The formula for table feed (ipm) is feed per tooth (ftp) 5 number of tool flutes 5 spindle speed (rpm).
- electrochemical machining ( ECM)
electrochemical machining ( ECM)
Operation in which electrical current flows between a workpiece and conductive tool through an electrolyte. Initiates a chemical reaction that dissolves metal from the workpiece at a controlled rate. Unlike with traditional cutting methods, workpiece hardness is not a factor, making ECM suitable for difficult-to-machine materials. Takes such forms as electrochemical grinding, electrochemical honing and electrochemical turning.
- electrochemical machining ( ECM)2
electrochemical machining ( ECM)
Operation in which electrical current flows between a workpiece and conductive tool through an electrolyte. Initiates a chemical reaction that dissolves metal from the workpiece at a controlled rate. Unlike with traditional cutting methods, workpiece hardness is not a factor, making ECM suitable for difficult-to-machine materials. Takes such forms as electrochemical grinding, electrochemical honing and electrochemical turning.
- modular design ( modular construction)
modular design ( modular construction)
Manufacturing of a product in subassemblies that permits fast and simple replacement of defective assemblies and tailoring of the product for different purposes. See interchangeable parts.
- polishing
polishing
Abrasive process that improves surface finish and blends contours. Abrasive particles attached to a flexible backing abrade the workpiece.