Contact Details
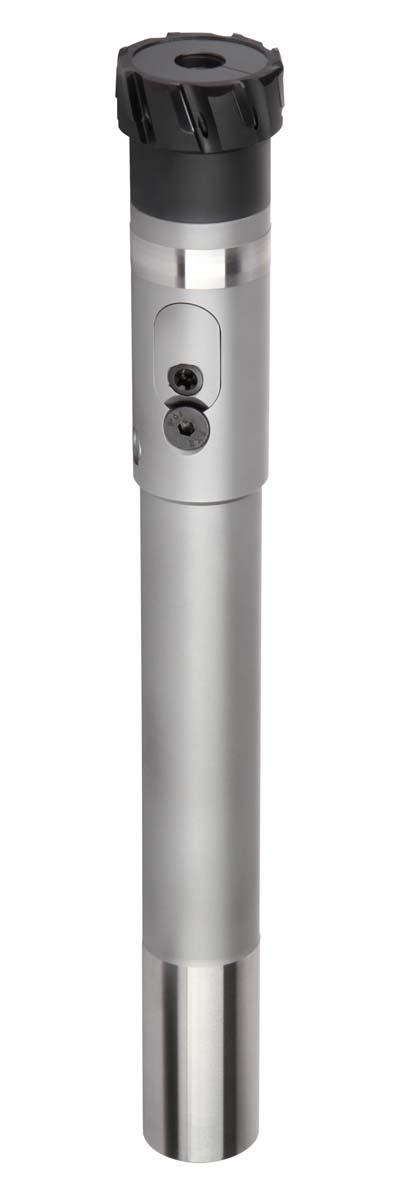
Kennametal Inc. introduces a new line of innovative, expandable, high performance reamers. RMB-E monobloc and RHM-E modular reamers are accurate, easy-to-use, expansion tools.
Both RMB-E and RHM-E expandable reamers operate with a rotation wrench that offers a predictable linear expansion of 2µm for every 30 degree turned. This reportedly means that no adjustment measurements are required and the tool does not need to be removed from the machine during the expansion process. The simple adjustment process also requires less training, as manual calibration is not necessary. Not only does this feature make expanding tool sizes easier and more manageable, it also dramatically reduces downtime when machining.
These expansion platforms are capable of a large expansion range of up to three times IT6 tolerance class. This capability increases tool life by up to 300 percent. With these tools, elastic expansion takes place within the steel body so that the tool is not damaged. The proprietary failsafe design has a runstop after two complete revolutions to further prevent tool damage through over-expansion. This expansion system also allows the user to reverse any expansion in case the tools has been expanded too much or if a smaller expansion is needed.
The RMB-E and RHM-E platforms are both offered with internal through coolant capabilities and are available in two geometries: straight fluted for machining blind holes and helical fluted for through holes. Kennametal is offering these products in two different grades. KC6305 is for multipurpose applications, and KC6005 is engineered especially for cast iron. Further cutting, such as cermets, PCD, or CBN materials will be available as custom solutions. All of these grades provide superior wear resistance and outstanding frictional properties for longer tool life and good surface quality. RHM-E reamers are available in diameters ranging from 14mm to 42mm, while RMB-E diameters range from 14mm to 20mm.
Related Glossary Terms
- calibration
calibration
Checking measuring instruments and devices against a master set to ensure that, over time, they have remained dimensionally stable and nominally accurate.
- cermets
cermets
Cutting tool materials based mostly on titanium carbonitride with nickel and/or cobalt binder. Cermets are characterized by high wear resistance due to their chemical and thermal stability. Cermets are able to hold a sharp edge at high cutting speeds and temperatures, which results in exceptional surface finish when machining most types of steels.
- coolant
coolant
Fluid that reduces temperature buildup at the tool/workpiece interface during machining. Normally takes the form of a liquid such as soluble or chemical mixtures (semisynthetic, synthetic) but can be pressurized air or other gas. Because of water’s ability to absorb great quantities of heat, it is widely used as a coolant and vehicle for various cutting compounds, with the water-to-compound ratio varying with the machining task. See cutting fluid; semisynthetic cutting fluid; soluble-oil cutting fluid; synthetic cutting fluid.
- cubic boron nitride ( CBN)
cubic boron nitride ( CBN)
Crystal manufactured from boron nitride under high pressure and temperature. Used to cut hard-to-machine ferrous and nickel-base materials up to 70 HRC. Second hardest material after diamond. See superabrasive tools.
- polycrystalline diamond ( PCD)
polycrystalline diamond ( PCD)
Cutting tool material consisting of natural or synthetic diamond crystals bonded together under high pressure at elevated temperatures. PCD is available as a tip brazed to a carbide insert carrier. Used for machining nonferrous alloys and nonmetallic materials at high cutting speeds.
- tolerance
tolerance
Minimum and maximum amount a workpiece dimension is allowed to vary from a set standard and still be acceptable.
- wear resistance
wear resistance
Ability of the tool to withstand stresses that cause it to wear during cutting; an attribute linked to alloy composition, base material, thermal conditions, type of tooling and operation and other variables.