Contact Details
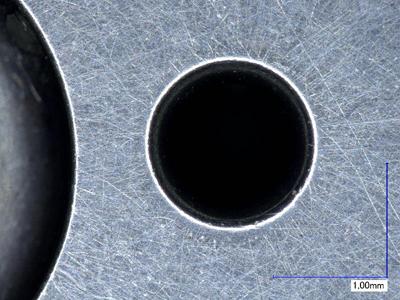
Fuel system manufacturers seeking the best fuel performance require flexible high-flow grinding and high-flow test capabilities to achieve finely tuned orifices in numerous design variations. To this end, Kennametal Precision Surface Solutions is announcing EXTRUDE HONE MF PROGRESS, the next generation of flow tuning and flow measurement featuring a flow targeting accuracy to +/-1 percent aimed at orifices 100-350µm in parts less than 30mm in diameter and flow rates up to 5 L/min.
"Additionally, MF PROGRESS delivers another exclusive added value that we call Flexibility Through Modularity," says Sharath Shankaregowda, Kennametal Precision Surface Solutions MICROFLOW product manager. "Customers benefit from a self-contained modular construction for each process (grinding, flush, flow testing, etc.) and configurable hardware (manifolds, frequency drives, etc.)."
Customers are saying adding such advanced process options can help ensure components meet ever more stringent government regulations. From CAFÉ in North America, EURO6 and expected EURO7 in Europe, and PRC standards in Asia, all focused on reducing CO2 emissions, EXTRUDE HONE MF PROGRESS provides the perfect next step in upgraded manufacturing and finishing. In addition, this all takes place in a 25 percent reduced machine footprint, 50 percent less tool wear compared to previous-generation equipment, and depending on the application the output can be increased by up to 100 percent.
MICROFLOW Explained:
• MICROFLOW is the real-time monitored flow of abrasive media through small passages, such as fuel-injector spray holes.
• It achieves specific, repeatable processing results, including edge radius, micro-hole size and surface finish. These changes to small-hole geometry improve part function and performance.
• Media flows in one direction, similar to part operation.
• Increased flow is attributed to subtly changing the geometry of the opening entrance (opening exit usually is not affected).
• MICROFLOW processing involves pressure drop, flow rate, geometry, and fluid properties; machine design and dynamics; workpiece characteristics; media properties and processing procedures.
• Exclusive range of standard and customized MICROFLOW media with specific properties perform a step beyond classical hydro erosive liquid.
EXTRUDE HONE MF PROGRESS is available in various inside station layouts: flow tuning, media reclaim, flush module, test module, marking, thanks to the system's modular design and construction. It is easy to configure and easy to fit into modern production lines ready for robotic or other handling system automation. The machine also comes with expanded on-screen maintenance capabilities and improved filtration to further pump and valve life.
Reliability being at the heart of production control requirements, EXTRUDE HONE MF PROGRESS provides for online monitoring and control of all relevant parameters. The online feature is also beneficial in delivering remote process demonstrations and gathering resulting data.
Related Glossary Terms
- abrasive
abrasive
Substance used for grinding, honing, lapping, superfinishing and polishing. Examples include garnet, emery, corundum, silicon carbide, cubic boron nitride and diamond in various grit sizes.
- grinding
grinding
Machining operation in which material is removed from the workpiece by a powered abrasive wheel, stone, belt, paste, sheet, compound, slurry, etc. Takes various forms: surface grinding (creates flat and/or squared surfaces); cylindrical grinding (for external cylindrical and tapered shapes, fillets, undercuts, etc.); centerless grinding; chamfering; thread and form grinding; tool and cutter grinding; offhand grinding; lapping and polishing (grinding with extremely fine grits to create ultrasmooth surfaces); honing; and disc grinding.
- modular design ( modular construction)
modular design ( modular construction)
Manufacturing of a product in subassemblies that permits fast and simple replacement of defective assemblies and tailoring of the product for different purposes. See interchangeable parts.
- modular design ( modular construction)2
modular design ( modular construction)
Manufacturing of a product in subassemblies that permits fast and simple replacement of defective assemblies and tailoring of the product for different purposes. See interchangeable parts.