Contact Details
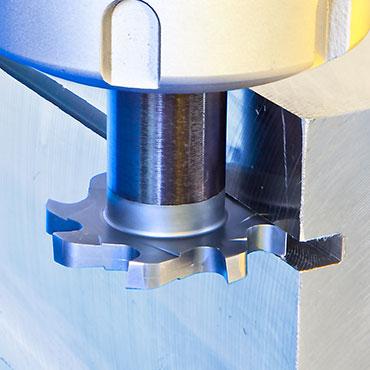
The cutters consist of interchangeable solid carbide T-SLOT milling heads and cylindrical shanks assembled by means of a unique spline connection.
The spline connection is used to transmit the torque in the best way, ensuring very durable assembly to withstand considerable cutting forces during slot milling and bending forces caused by long reach overhang.
The spline connection designation is SP… where the no. indicates the connection size.
The general duty cutting geometry of the heads is suited for efficient slot milling on a wide spectrum of workpiece materials for maximum depth of cut.
Features
- Wide range of 32 mm (1.25 ") ,40 mm (1.5 ") and 50 mm diameter solid carbide milling heads with 8 ,10 and 12 effective teeth and width range of 1 -12 mm (0.046 – 0.375 ")
- The solid heads are clamped onto the shanks with a central screw
- Steel and solid carbide shanks with different lengths
- SD Cab - Adapter for connecting SD T-SLOT heads with MULTI-MASTER shanks
Diameter range:
- SD D32 mm (1.25")
No. of Flutes: 8
Insert width: 1 – 8.5 mm (0.046 – 0.25 ")
Insert max depth: 10 mm (0.393") with SP11 and 8 mm (0.315") with SP15.
Diameter range:
- SD D40 mm (1.5").
No. of Flutes: 10
Insert width: 1 – 10 mm (0.078– 0.375 ")
Insert max depth: 13 mm (0.51") with SP13 and 11 mm (0.43") with SP17.
Diameter range:
- SD D50 mm
No. of Flutes: 12
Insert width: 4– 12 mm
Insert max depth: 15 mm with SP19.
Grades
- IC908
Related Glossary Terms
- depth of cut
depth of cut
Distance between the bottom of the cut and the uncut surface of the workpiece, measured in a direction at right angles to the machined surface of the workpiece.
- gang cutting ( milling)
gang cutting ( milling)
Machining with several cutters mounted on a single arbor, generally for simultaneous cutting.
- milling
milling
Machining operation in which metal or other material is removed by applying power to a rotating cutter. In vertical milling, the cutting tool is mounted vertically on the spindle. In horizontal milling, the cutting tool is mounted horizontally, either directly on the spindle or on an arbor. Horizontal milling is further broken down into conventional milling, where the cutter rotates opposite the direction of feed, or “up” into the workpiece; and climb milling, where the cutter rotates in the direction of feed, or “down” into the workpiece. Milling operations include plane or surface milling, endmilling, facemilling, angle milling, form milling and profiling.