Contact Details
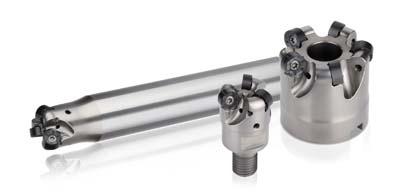
WIDIA has announced the M200 copy mill as its latest addition to the WIDIA Victory line of tooling. WIDIA's new M200 series sets the standards for performance and productivity in the die and mold, energy, and aerospace industries and is engineered to outperform in roughing to semi-finishing applications.
The IC12mm double-sided inserts used with this platform are capable of running in multiple types of milling operations and workpiece materials. This series of milling inserts is available in three distinctive geometries that are specifically designed for multiple milling tasks: ML for stainless steel and high-temp alloys;mm for general purpose milling, including steel; and MH for heavy applications like cast iron and high-strength steels. With 12 cutting edges, the M200 series offers a competitive cost per edge.
Available in milling grades WK15PM, WP25PM, WU35PM, WP35CM, the M200 is designed to work effectively at high speeds and is engineered for longer tool life in finishing to heavy roughing operations. Additionally, the anti-rotation feature included in this platform enhances insert stability and ensures safety during operation.
Tool bodies for the M200 series also come in a variety of internally cooled styles, including screw-on, Weldon, cylindrical, and shell mill. Each body style was designed with an easy-to-use anti-rotation feature that provides excellent stability for higher feed rates and cutting forces. Each of the tool bodies has a higher clearance to permit pocketing, profiling, and 5-axis machining applications.
Related Glossary Terms
- clearance
clearance
Space provided behind a tool’s land or relief to prevent rubbing and subsequent premature deterioration of the tool. See land; relief.
- feed
feed
Rate of change of position of the tool as a whole, relative to the workpiece while cutting.
- gang cutting ( milling)
gang cutting ( milling)
Machining with several cutters mounted on a single arbor, generally for simultaneous cutting.
- milling
milling
Machining operation in which metal or other material is removed by applying power to a rotating cutter. In vertical milling, the cutting tool is mounted vertically on the spindle. In horizontal milling, the cutting tool is mounted horizontally, either directly on the spindle or on an arbor. Horizontal milling is further broken down into conventional milling, where the cutter rotates opposite the direction of feed, or “up” into the workpiece; and climb milling, where the cutter rotates in the direction of feed, or “down” into the workpiece. Milling operations include plane or surface milling, endmilling, facemilling, angle milling, form milling and profiling.
- milling machine ( mill)
milling machine ( mill)
Runs endmills and arbor-mounted milling cutters. Features include a head with a spindle that drives the cutters; a column, knee and table that provide motion in the three Cartesian axes; and a base that supports the components and houses the cutting-fluid pump and reservoir. The work is mounted on the table and fed into the rotating cutter or endmill to accomplish the milling steps; vertical milling machines also feed endmills into the work by means of a spindle-mounted quill. Models range from small manual machines to big bed-type and duplex mills. All take one of three basic forms: vertical, horizontal or convertible horizontal/vertical. Vertical machines may be knee-type (the table is mounted on a knee that can be elevated) or bed-type (the table is securely supported and only moves horizontally). In general, horizontal machines are bigger and more powerful, while vertical machines are lighter but more versatile and easier to set up and operate.
- profiling
profiling
Machining vertical edges of workpieces having irregular contours; normally performed with an endmill in a vertical spindle on a milling machine or with a profiler, following a pattern. See mill, milling machine.