Contact Details
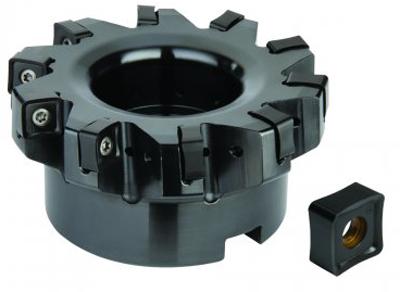
With eight cutting edges, the new KSSM8+ face milling platform from Kennametal is focused on maximum metal-cutting performance in cast irons and steel workpieces at a low cost.
Cutting cast-iron parts is tough and it should be. Cast-iron pump housings, brake calipers, turbine housings, and many other parts are critical foundation components for entire industries, including automotive, heavy equipment, energy, and fluid power. Achieving the highest level of milling performance at the lowest cost per cutting edge is essential for success.
The IC10 size provides a 9mm (0.354") depth of cut, while the IC 12.7 achieves a 6mm (0.236") DOC. Both have high lead angles (88 degress and 87 degrees, respectively), making them good choices in applications where fixture limitations or part designs call for close to 90-degree shoulders.
The double-sided insert design with eight cutting edges provides users with the lowest cost per edge, while the -LD geometry's positive rake face and honed edges result in lower cutting forces and good floor finishes in medium and finish machining.
While face milling is a common, everyday metal-cutting task, it is one with many critical considerations. Depth of cut must be balanced against maximizing speeds and feeds for long tool life. High surface finish requirements must be factored into achieving high production efficiencies. That is why a range of insert grades for the new KSSM8+ platform is available for face milling steels, stainless steels, and wet or dry machining of ductile cast irons. Together with the choice of medium- and fine-density cutter bodies makes KSSM8+ the right solution in addition to the preferred low-cost choice when milling cast irons.
Related Glossary Terms
- cast irons
cast irons
Cast ferrous alloys containing carbon in excess of solubility in austenite that exists in the alloy at the eutectic temperature. Cast irons include gray cast iron, white cast iron, malleable cast iron and ductile, or nodular, cast iron. The word “cast” is often left out.
- depth of cut
depth of cut
Distance between the bottom of the cut and the uncut surface of the workpiece, measured in a direction at right angles to the machined surface of the workpiece.
- ductile cast irons
ductile cast irons
Ferrous alloys in which graphite is present as tiny balls or spherulites. The spheroidal graphite structure is produced by adding one or more elements to the molten metal, among which magnesium and cerium are commercially important. Approximate composition of ductile cast irons is: 3.0 to 4.0 percent carbon, 0.1 to 1.0 percent manganese, 1.8 to 2.8 percent silicon, 0.1 percent (maximum) phosphorus and 0.03 percent (maximum) sulfur. Typical ductile cast iron grades are D-4018, D-4512, D-5506 and D-7003 by definition of the Society of Automotive Engineers; 60-40-18, 65-45-12, 80-55-06, 100-70-03 and 120-90-02 by definition of the American Society for Testing and Materials. Also known as nodular cast irons.
- fixture
fixture
Device, often made in-house, that holds a specific workpiece. See jig; modular fixturing.
- gang cutting ( milling)
gang cutting ( milling)
Machining with several cutters mounted on a single arbor, generally for simultaneous cutting.
- inscribed circle ( IC)
inscribed circle ( IC)
Imaginary circle that touches all sides of an insert. Used to establish size. Measurements are in fractions of an inch and describe the diameter of the circle.
- milling
milling
Machining operation in which metal or other material is removed by applying power to a rotating cutter. In vertical milling, the cutting tool is mounted vertically on the spindle. In horizontal milling, the cutting tool is mounted horizontally, either directly on the spindle or on an arbor. Horizontal milling is further broken down into conventional milling, where the cutter rotates opposite the direction of feed, or “up” into the workpiece; and climb milling, where the cutter rotates in the direction of feed, or “down” into the workpiece. Milling operations include plane or surface milling, endmilling, facemilling, angle milling, form milling and profiling.
- rake
rake
Angle of inclination between the face of the cutting tool and the workpiece. If the face of the tool lies in a plane through the axis of the workpiece, the tool is said to have a neutral, or zero, rake. If the inclination of the tool face makes the cutting edge more acute than when the rake angle is zero, the rake is positive. If the inclination of the tool face makes the cutting edge less acute or more blunt than when the rake angle is zero, the rake is negative.
- stainless steels
stainless steels
Stainless steels possess high strength, heat resistance, excellent workability and erosion resistance. Four general classes have been developed to cover a range of mechanical and physical properties for particular applications. The four classes are: the austenitic types of the chromium-nickel-manganese 200 series and the chromium-nickel 300 series; the martensitic types of the chromium, hardenable 400 series; the chromium, nonhardenable 400-series ferritic types; and the precipitation-hardening type of chromium-nickel alloys with additional elements that are hardenable by solution treating and aging.
Additional Products from Kennametal Inc.
Pagination
- First page
- Previous page
- 1
- 2
- 3
- 4
- 5
- 6
- 7
- 8
- 9