Contact Details
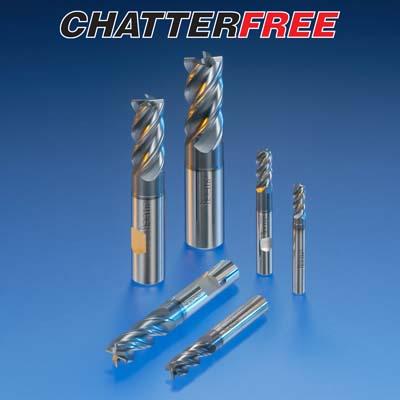
With a new level of built-in asymmetry, ISCAR EC-H CHATTERFREE solid carbide endmills bring a new level of speed and process security to slotting and shoulder milling of ferrous metals. On alloy and stainless steel, users report 20-25 percent longer tool life than with ordinary variable-pitch endmills. Familiar variable-pitch flutes have proven out for years for their vibration-dampening characteristics in solid carbide endmills.
Now ISCAR has gone one step better by varying the helixes as well. Two flutes have a 35-degree helix angle and the other two ascend at 37 degrees. ISCAR's theory is that the more asymmetry they design into a solid carbide tool, the greater its resistance to harmonic vibration and chatter. The variable helix adds one extra dampening influence against harmonic vibrations, a principal cause of tool fracture in hard but brittle solid carbide endmills. By the same mechanism it also further minimizes chatter marks in the workpiece.
EC-H CHATTERFREE endmills are available in the diameter range of 6-25mm, with either Weldon (relieved) or cylindrical (straight) shanks. All have corner radii and are made of IC900, the most versatile PVD coated grade available today. Besides defeating vibration, ISCAR EC-H CHATTERFREE endmills feature a free-cutting edge geometry that improves chip evacuation and reduces cutting forces, suiting them ideally for low power machines with ISO 40 or BT40 adaptations. With such improved control over vibration and cutting forces, they can safely be used on slots up to 2.5 x D in alloy and stainless steel.
Four-flute EC-H CHATTERFREE endmills come in three types: standard lengths with cylindrical shanks, standard lengths with relieved shanks and extra long 4 x D mills with cylindrical shanks. Two early applications underscore the added performance of the variable-helix/variable-flute endmill vs. standard variable-flute tool. In rough shoulder milling of an austenitic stainless steel workpiece, the material removal rate improved to 20.05 cm/min., from 9.17 with the tool change, and tool life improved to 45 pieces vs. 30, before flank wear necessitated replacement.
The main improvement with the EC-H cutter stemmed from doubling the depth of cut, which would have snapped off the competing tool. Also, in the case of a rough slotting operation with X6CrNiMoTi17-12-2, the EC-H CHATTERFREE endmill lasted through 60 pieces under identical conditions that had snapped off the competing endmill at 45 pieces.
Related Glossary Terms
- chatter
chatter
Condition of vibration involving the machine, workpiece and cutting tool. Once this condition arises, it is often self-sustaining until the problem is corrected. Chatter can be identified when lines or grooves appear at regular intervals in the workpiece. These lines or grooves are caused by the teeth of the cutter as they vibrate in and out of the workpiece and their spacing depends on the frequency of vibration.
- depth of cut
depth of cut
Distance between the bottom of the cut and the uncut surface of the workpiece, measured in a direction at right angles to the machined surface of the workpiece.
- endmill
endmill
Milling cutter held by its shank that cuts on its periphery and, if so configured, on its free end. Takes a variety of shapes (single- and double-end, roughing, ballnose and cup-end) and sizes (stub, medium, long and extra-long). Also comes with differing numbers of flutes.
- flank wear
flank wear
Reduction in clearance on the tool’s flank caused by contact with the workpiece. Ultimately causes tool failure.
- flutes
flutes
Grooves and spaces in the body of a tool that permit chip removal from, and cutting-fluid application to, the point of cut.
- gang cutting ( milling)
gang cutting ( milling)
Machining with several cutters mounted on a single arbor, generally for simultaneous cutting.
- helix angle
helix angle
Angle that the tool’s leading edge makes with the plane of its centerline.
- milling
milling
Machining operation in which metal or other material is removed by applying power to a rotating cutter. In vertical milling, the cutting tool is mounted vertically on the spindle. In horizontal milling, the cutting tool is mounted horizontally, either directly on the spindle or on an arbor. Horizontal milling is further broken down into conventional milling, where the cutter rotates opposite the direction of feed, or “up” into the workpiece; and climb milling, where the cutter rotates in the direction of feed, or “down” into the workpiece. Milling operations include plane or surface milling, endmilling, facemilling, angle milling, form milling and profiling.
- physical vapor deposition ( PVD)
physical vapor deposition ( PVD)
Tool-coating process performed at low temperature (500° C), compared to chemical vapor deposition (1,000° C). Employs electric field to generate necessary heat for depositing coating on a tool’s surface. See CVD, chemical vapor deposition.
- slotting
slotting
Machining, normally milling, that creates slots, grooves and similar recesses in workpieces, including T-slots and dovetails.