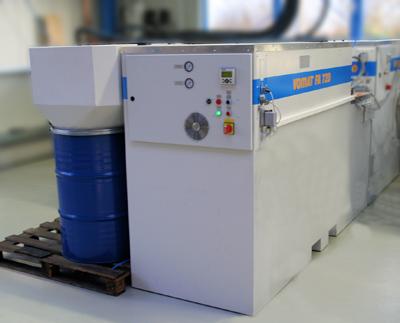
In tool grinding all individual processing steps are part of a coherent value chain. Therefore, it is important that the filtration process of metal coolants is integrated seamlessly in this value chain. When operational requirements or technical improvements cause changes and flexibility is needed, the filtration system should meet those new needs. The filtration specialist Vomat meets these challenges with a line-up of high-tech systems. From stand alone to large industrial central filtration systems Vomat's offerings are of modular design and can be adapted quickly and easily to changing shop and production requirements.
Stephan Hecht of oelheld U.S. Inc., Vomat's general agent in Elgin, Ill., states: "By design the stand alone Vomat-FA-series models have a flow capacity of 120 to 960 liters per minute. In addition, we provide our customers with a number of add-on modules which can be easily integrated, when the need arises. The array of modules includes displays for the complete visualization of the filtration process in real time, frequency controlled pumps, internal and external pre-filters and various cooling solutions. In close cooperation with the customer, Vomat tailors a filtration solution to individual production conditions, which can be can be altered in case requirements change. If our client implements technological improvements in his production process, Vomat can help to make sure that the filtration system will meet the new requirements."
Besides the modular expandability of Vomat systems, it is mainly the innovative filter technology that provides Vomat customers with economic benefits: Vomat systems filter in full flow stream and separate dirty from clean oil 100 percent, thanks to high capacity pre-coated filters. The results are lubricants, which meet NAS 7/8 or 3-5µm in terms of purity and cleanliness. Clean oil is decisive for dimensional accuracy and surface quality of the finished work piece.
In addition, Vomat systems adapt intelligently to changing volumes of sludge and automatically initiate the backflush cycle depending filter contamination. Each Vomat machine is equipped with enough filters, that during the backflush cycle the operator always has full oil flow. This allows for energy efficient, time optimized operation in sync with the customer's grinding machine. The Vomat FA 120 through 420 series machines with dimensions of 1 x 1 x 1,6 meters are also significantly smaller than comparable filtration systems on the market. This keeps transportation costs low, possibly reduces facility alterations and provides the client with more floor space.
Flexibility and customer satisfaction are paramount at Vomat. Hecht said: "We analyze the requirements of each operation exactly in order to supply the optimal system. Many times customers invite us early on to be involved in the planning phase when new operations or modifications to existing ones are planned. Even operations where frequent changes are common are always in good shape with Vomat filtration."
Contact Details
Related Glossary Terms
- grinding
grinding
Machining operation in which material is removed from the workpiece by a powered abrasive wheel, stone, belt, paste, sheet, compound, slurry, etc. Takes various forms: surface grinding (creates flat and/or squared surfaces); cylindrical grinding (for external cylindrical and tapered shapes, fillets, undercuts, etc.); centerless grinding; chamfering; thread and form grinding; tool and cutter grinding; offhand grinding; lapping and polishing (grinding with extremely fine grits to create ultrasmooth surfaces); honing; and disc grinding.
- grinding machine
grinding machine
Powers a grinding wheel or other abrasive tool for the purpose of removing metal and finishing workpieces to close tolerances. Provides smooth, square, parallel and accurate workpiece surfaces. When ultrasmooth surfaces and finishes on the order of microns are required, lapping and honing machines (precision grinders that run abrasives with extremely fine, uniform grits) are used. In its “finishing” role, the grinder is perhaps the most widely used machine tool. Various styles are available: bench and pedestal grinders for sharpening lathe bits and drills; surface grinders for producing square, parallel, smooth and accurate parts; cylindrical and centerless grinders; center-hole grinders; form grinders; facemill and endmill grinders; gear-cutting grinders; jig grinders; abrasive belt (backstand, swing-frame, belt-roll) grinders; tool and cutter grinders for sharpening and resharpening cutting tools; carbide grinders; hand-held die grinders; and abrasive cutoff saws.
- modular design ( modular construction)
modular design ( modular construction)
Manufacturing of a product in subassemblies that permits fast and simple replacement of defective assemblies and tailoring of the product for different purposes. See interchangeable parts.