Contact Details
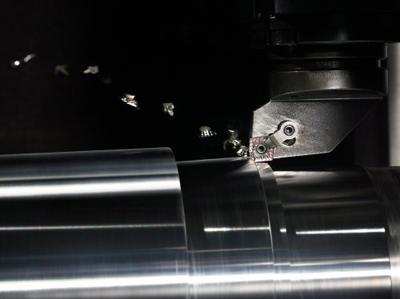
Shops turning a wide range of materials face extreme challenges daily. They know that the most efficient machining means finding the "sweet spot." Too slow may increase attention to detail but also increase opportunities from speedier competitors. Accelerating speeds and feeds may actually lower efficiency if you're using up tooling faster or stopping your turning center more often to clean out stringers. The WIDIA Victory family of turning inserts from WIDIA is announcing new geometries and grades that extend your turning sweet spot by delivering excellent chip flow that results in smooth machining, improved efficiencies, and extended tool life.
For difficult-to-machine materials like Inconel and Rene in complex aerospace applications or cobalt-chromes and high-alloy stainless steels in precise medical applications, the new WIDIA Victory FS geometry is a ground, high positive design best used in finishing tasks where surface finish and minimizing part deflection are critical. Precision grinding, proprietary nose geometry, and optimized edge treatment result in an insert that retains its high-quality cutting edge with minimal heat generation and good chip breaking at finishing parameters. Its high rake angle reduces cutting forces and also reduces built-up edge.
The FS is available in WS10PT, a high-performance PVD grade. This grade utilizes a two-layer coating that increases coating integrity and reduces depth-of-cut notching, increasing productivity and dependability. All inserts in the WS10PT grade undergo a post-coat treatment to increase compressive stress and improve edge toughness. This delays built-up edge and results in longer tool life. WS10PT is available in other geometries including the UR geometry.
WIDIA's Universal Roughing (UR) geometry is specifically designed to increase roughing and medium turning performance in stainless steels and steel workpieces. Its unique chip breaker and rake profile design without inflection points breaks up stringers without concentrating cutting forces that result in breakage. Its positive rake angle further reduces cutting forces while improving depth of cut notching resistance. Together with a multilayer coating with a ZrCN top coat for both extended performance and improved wear identification, the result is the ability to increase speeds or feed rates efficiently, increasing productivity and reducing cycle times.
WIDIA grades WP15CT, WP25CT, and WP35CT are also available in the Universal Roughing geometry to particularly improve performance on steel workpieces. Emphasizing an excellent combination of toughness and cutting performance, WP15CT is universally applicable on all finishing, medium machining and light roughing steel operations, wet or dry, interrupted and non-interrupted.
WP25CT is best applicable on all medium to light roughing operations, wet or dry on interrupted and non-interrupted cuts. WP35CT is for all roughing and heavy roughing jobs, also wet or dry, interrupted or non-interrupted. These new grades also feature the ZrCN top coating and proprietary post-coat treatment that reduces friction and improves edge toughness as well as functioning as an excellent wear indicator.
"Shops doing a major percentage of turning work know beating the competition involves delivering excellent results reliably," says WIDIA global product manager John Gable. "The WIDIA Victory turning portfolio is just the kind of tool selection that allows these shops to up their performance to even higher levels."
Related Glossary Terms
- built-up edge ( BUE)
built-up edge ( BUE)
1. Permanently damaging a metal by heating to cause either incipient melting or intergranular oxidation. 2. In grinding, getting the workpiece hot enough to cause discoloration or to change the microstructure by tempering or hardening.
- depth of cut
depth of cut
Distance between the bottom of the cut and the uncut surface of the workpiece, measured in a direction at right angles to the machined surface of the workpiece.
- feed
feed
Rate of change of position of the tool as a whole, relative to the workpiece while cutting.
- grinding
grinding
Machining operation in which material is removed from the workpiece by a powered abrasive wheel, stone, belt, paste, sheet, compound, slurry, etc. Takes various forms: surface grinding (creates flat and/or squared surfaces); cylindrical grinding (for external cylindrical and tapered shapes, fillets, undercuts, etc.); centerless grinding; chamfering; thread and form grinding; tool and cutter grinding; offhand grinding; lapping and polishing (grinding with extremely fine grits to create ultrasmooth surfaces); honing; and disc grinding.
- physical vapor deposition ( PVD)
physical vapor deposition ( PVD)
Tool-coating process performed at low temperature (500° C), compared to chemical vapor deposition (1,000° C). Employs electric field to generate necessary heat for depositing coating on a tool’s surface. See CVD, chemical vapor deposition.
- rake
rake
Angle of inclination between the face of the cutting tool and the workpiece. If the face of the tool lies in a plane through the axis of the workpiece, the tool is said to have a neutral, or zero, rake. If the inclination of the tool face makes the cutting edge more acute than when the rake angle is zero, the rake is positive. If the inclination of the tool face makes the cutting edge less acute or more blunt than when the rake angle is zero, the rake is negative.
- stainless steels
stainless steels
Stainless steels possess high strength, heat resistance, excellent workability and erosion resistance. Four general classes have been developed to cover a range of mechanical and physical properties for particular applications. The four classes are: the austenitic types of the chromium-nickel-manganese 200 series and the chromium-nickel 300 series; the martensitic types of the chromium, hardenable 400 series; the chromium, nonhardenable 400-series ferritic types; and the precipitation-hardening type of chromium-nickel alloys with additional elements that are hardenable by solution treating and aging.
- turning
turning
Workpiece is held in a chuck, mounted on a face plate or secured between centers and rotated while a cutting tool, normally a single-point tool, is fed into it along its periphery or across its end or face. Takes the form of straight turning (cutting along the periphery of the workpiece); taper turning (creating a taper); step turning (turning different-size diameters on the same work); chamfering (beveling an edge or shoulder); facing (cutting on an end); turning threads (usually external but can be internal); roughing (high-volume metal removal); and finishing (final light cuts). Performed on lathes, turning centers, chucking machines, automatic screw machines and similar machines.