Contact Details
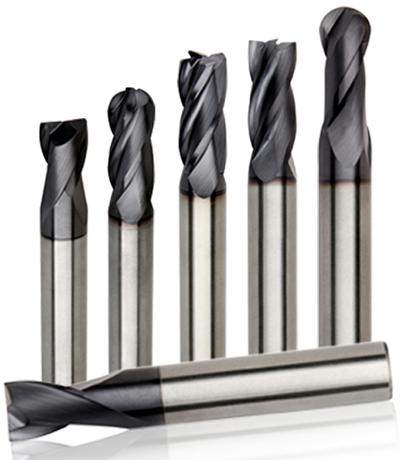
VariMill GP (General Purpose) is the latest in WIDIA's "Vari" family of tools, which extends to VariDrill and VariTap. "The ‘Vari-‘ in VariMill stands for variability, and essentially, this means high flexibility for manufacturers," says Global Product Manager Bernd Fiedler. Job shops by nature live and die by their ability to attack multiple, small-lot jobs under tight deadlines. Removing more metal at high rates across multiple operations with a single go-to multi-function tool means lower tool costs and better throughput compared to a lineup of high-performance specialty options.
VariMill GP is a portfolio of multi-purpose end mills suitable for roughing, semi-finishing, and finishing in an expanded range of work materials (aluminum, steels, stainless steels, and cast irons). The key benefits to manufacturing companies include reduced inventory and tool management on your machine tools as one tool covers roughing and finishing; lower tool costs due to long tool life at value pricing; and ease of reconditioning to keep the production flowing.
Consisting of two- and four-flute versions in square-end, chamfered-edge, and ball-nose configurations, VariMill GP end mills prove their performance increases through advanced design features. A 30-degree helix angle and eccentric relief provides strong edges and stability for roughing, semi-finishing, and finishing with the same tool. A thick TiAlN coating contributes to extended tool life across steel, stainless steel, and cast iron workpieces and milling, ramping, or slotting operations.
VariMill GP mills are available in inch and metric sizes along with varying lengths and shank styles. Customers looking to handle more work across more materials will do well to increase their flexibility and lower their costs with these truly multi-function, long-life, general-purpose mills.
High-torque chucks also benefit milling performance, and with among the highest levels of transmittable torque due to a more compact design, featuring a 40 percent thicker front-wall cross-section, the new WIDIA HydroForce HT universal hydraulic chuck provides the increased rigidity necessary for improved cutting parameters and better results. Clamping force is up to three times better than regular hydraulic chucks, and with improved vibration dampening, runout is threeµm at 2 times diameter overhang. Balance quality of G2.5 is achieved at speeds up to 25,000 rpm.
All this robust performance is available in a high-torque chuck requiring only two sizes for all your rotating tooling tasks, according to Kennametal. Direct clamping is available for 20 and 32mm (0.75 and 1.5") diameters and reducer sleeves are applied for all other diameters.
Related Glossary Terms
- chuck
chuck
Workholding device that affixes to a mill, lathe or drill-press spindle. It holds a tool or workpiece by one end, allowing it to be rotated. May also be fitted to the machine table to hold a workpiece. Two or more adjustable jaws actually hold the tool or part. May be actuated manually, pneumatically, hydraulically or electrically. See collet.
- gang cutting ( milling)
gang cutting ( milling)
Machining with several cutters mounted on a single arbor, generally for simultaneous cutting.
- helix angle
helix angle
Angle that the tool’s leading edge makes with the plane of its centerline.
- milling
milling
Machining operation in which metal or other material is removed by applying power to a rotating cutter. In vertical milling, the cutting tool is mounted vertically on the spindle. In horizontal milling, the cutting tool is mounted horizontally, either directly on the spindle or on an arbor. Horizontal milling is further broken down into conventional milling, where the cutter rotates opposite the direction of feed, or “up” into the workpiece; and climb milling, where the cutter rotates in the direction of feed, or “down” into the workpiece. Milling operations include plane or surface milling, endmilling, facemilling, angle milling, form milling and profiling.
- relief
relief
Space provided behind the cutting edges to prevent rubbing. Sometimes called primary relief. Secondary relief provides additional space behind primary relief. Relief on end teeth is axial relief; relief on side teeth is peripheral relief.
- shank
shank
Main body of a tool; the portion of a drill or similar end-held tool that fits into a collet, chuck or similar mounting device.
- slotting
slotting
Machining, normally milling, that creates slots, grooves and similar recesses in workpieces, including T-slots and dovetails.
- stainless steels
stainless steels
Stainless steels possess high strength, heat resistance, excellent workability and erosion resistance. Four general classes have been developed to cover a range of mechanical and physical properties for particular applications. The four classes are: the austenitic types of the chromium-nickel-manganese 200 series and the chromium-nickel 300 series; the martensitic types of the chromium, hardenable 400 series; the chromium, nonhardenable 400-series ferritic types; and the precipitation-hardening type of chromium-nickel alloys with additional elements that are hardenable by solution treating and aging.
- titanium aluminum nitride ( TiAlN)
titanium aluminum nitride ( TiAlN)
Often used as a tool coating. AlTiN indicates the aluminum content is greater than the titanium. See coated tools.