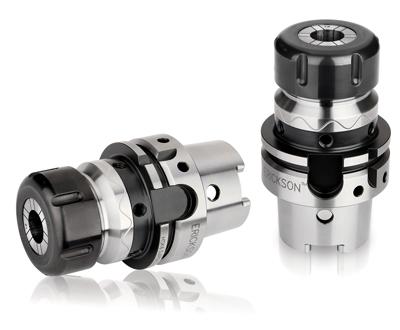
WIDIA says manufacturers of high-precision components (aerospace, transportation, die and mold, general engineering, and many more) wage a constant battle between producing high-tolerance parts and a "we-have-to-have-it-tomorrow" reality. WIDIA is announcing a significant new weapon to bring shops closer to victory, a universal, high-precision collet chuck offering use in multiple applications (milling, drilling, reaming, and tapping), while maintaining runout accuracies of 0.003mm (0.0001 inches) at 3xD.
Shops looking to upgrade performance and final part tolerance will welcome this chuck's features:
• Added versatility--the ability to continue using standard ER collets while upgrading to precision collets
• Thicker chuck walls and a stronger outer form for added rigidity and lower vibration for longer spindle and tool life
• Unique sealed-by-design precision collets (6 — 20mm or 0.24 – 0.79 inches) for excellent coolant delivery and longer tool life
• Better and repeatable balancing, all contributing to higher accuracy
Aerospace, die/mold and many other industries regularly encounter high-strength, difficult-to-machine materials requiring high torques, feeds, and forces. The danger of milling cutters being pulled out of the tool holder at these extreme forces has significantly increased. This is at least true for tool holders that offer precision clamping with good concentricity such as shrink-fit. Such toolholders work with frictional locking, but their clamping force is often not sufficient for roughing.
In response, the new WIDIA universal precision collet is available with Safe-Lock pull-out protection from Haimer. Helical grooves are ground into the shank of the milling tool that, together with the respective pin drivers in the chuck, prevent the tool from spinning or being pulled out of the holder altogether under extreme machining conditions. The helical path of the Safe-Lock grooves also allows for adjusting tool length, meaning tools can be reground and pre-set as usual.
Contact Details
Related Glossary Terms
- chuck
chuck
Workholding device that affixes to a mill, lathe or drill-press spindle. It holds a tool or workpiece by one end, allowing it to be rotated. May also be fitted to the machine table to hold a workpiece. Two or more adjustable jaws actually hold the tool or part. May be actuated manually, pneumatically, hydraulically or electrically. See collet.
- collet
collet
Flexible-sided device that secures a tool or workpiece. Similar in function to a chuck, but can accommodate only a narrow size range. Typically provides greater gripping force and precision than a chuck. See chuck.
- coolant
coolant
Fluid that reduces temperature buildup at the tool/workpiece interface during machining. Normally takes the form of a liquid such as soluble or chemical mixtures (semisynthetic, synthetic) but can be pressurized air or other gas. Because of water’s ability to absorb great quantities of heat, it is widely used as a coolant and vehicle for various cutting compounds, with the water-to-compound ratio varying with the machining task. See cutting fluid; semisynthetic cutting fluid; soluble-oil cutting fluid; synthetic cutting fluid.
- gang cutting ( milling)
gang cutting ( milling)
Machining with several cutters mounted on a single arbor, generally for simultaneous cutting.
- milling
milling
Machining operation in which metal or other material is removed by applying power to a rotating cutter. In vertical milling, the cutting tool is mounted vertically on the spindle. In horizontal milling, the cutting tool is mounted horizontally, either directly on the spindle or on an arbor. Horizontal milling is further broken down into conventional milling, where the cutter rotates opposite the direction of feed, or “up” into the workpiece; and climb milling, where the cutter rotates in the direction of feed, or “down” into the workpiece. Milling operations include plane or surface milling, endmilling, facemilling, angle milling, form milling and profiling.
- shank
shank
Main body of a tool; the portion of a drill or similar end-held tool that fits into a collet, chuck or similar mounting device.
- tolerance
tolerance
Minimum and maximum amount a workpiece dimension is allowed to vary from a set standard and still be acceptable.