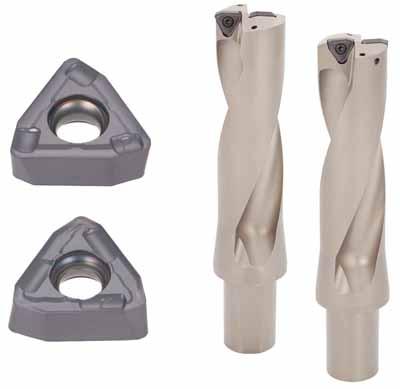
With ever greater importance being put upon the productivity, accuracy and overall quality of holemaking, the Tungaloy Corp. has developed its new TungSix-Drill to enhance all these facts for end users. The TungSix-Drill is the world's first indexable drilling range that offers double sided inserts with six cutting edges to reduce consumption.
The TungSix-Drill is reportedly an extremely economical drilling solution from a leading Japanese cutting tool manufacturer that has been created with six cutting edges for reduced tooling costs and inventory requirements for the end user. The innovative new series incorporates a drill body with two insert pockets, one for centre cutting and the other for cutting the periphery. This tool design suits setup and inventory needs of the end user by enabling just one insert type to be used for both the central and peripheral insert pockets. Tungaloy achieves six cutting edges by creating enough distance between each cutting edge to incorporate a trigon shaped insert. This unique design optimizes the insert position to prevent overlapping of damaged edges that can de-stabilize drill performance when alternating insert corners. Furthermore each insert has an alternate design on the opposite side, with one side of each insert being suited to the central insert pocket and the other side of the insert for the peripheral pocket.
By creating different insert geometries on either side of the insert, the TungSix-Drill can incorporate the optimum geometry for each insert position. The central insert geometry has a thick width and gentle curve to prevent chip packing. Additionally, it generates low cutting forces and extends insert life with a grooved surface on the rake face. As for the peripheral geometry, it includes a high rake angle with a high breaker wall to reduce cutting forces while enhancing the chip-breaking process.
The R&D teams at Tungaloy have optimized the drill body and insert geometry to enhance cutting balance, according to the company. Added to this, the corner of the central insert features an obtuse angle relief. This design eliminates the commonplace issue of corner fracture with alternate indexable drills. Additionally, with a positive land design, the cutting forces are reduced even further to perform at levels comparable to drills with fewer cutting edges. This also decreases the power consumption of the machine tool and the stresses placed upon the spindle during operation.
A common issue with many indexable cutting tools is incorrect clamping of the insert. The engineers at Tungaloy have overcome this issue by designing a new insert seat which prevents incorrect insert clamping.
One aspect that sets the TungSix-Drill apart from its competitors is the innovative drill body that incorporates twisted through coolant holes that directs coolant right to the cutting edge. This design increases coolant flow, therefore improving chip evacuation, cooling and lubrication of the cutting edges.
The drill bodies are available in L/D=2 and L/D=3 dimensions with diameters from 1.125" to 2.000" in 0.0625" increments. This diameter range is covered with four sizes of inserts; WWMU08, 09, 11, and 13.
The new TungSix-Drill is available with Tungaloy's renowned AH9030 and AH6030 insert grades that enable the exciting new drill to be used on a wide variety of material types. The PVD coated AH9030 delivers excellent wear and oxidation resistance to generate better tool life than competitor inserts. In addition, it is coated with Tungaloy's special surface technology "PremiumTec" that reduces chip adhesion and increases the flow of swarf from the cutting edge.
The recent addition of AH6030 to the TungSix-Drill series has been added to improve machining performance on stainless steels and low carbon steels. Offered with the new DS chipbreaker, AH6030 excels when cutting stainless steel. The DS chipbreaker sees a wider land width on the central edge corner to prevent chipping and fracture when subjected to low to zero cutting speeds and high impact loads. With a dimple on the cutting edge, chip curling is significantly improved on the peripheral insert while the dimple on the central insert crushes the chips and helps to improve chip flow.
Contact Details
Related Glossary Terms
- carbon steels
carbon steels
Known as unalloyed steels and plain carbon steels. Contains, in addition to iron and carbon, manganese, phosphorus and sulfur. Characterized as low carbon, medium carbon, high carbon and free machining.
- chipbreaker
chipbreaker
Groove or other tool geometry that breaks chips into small fragments as they come off the workpiece. Designed to prevent chips from becoming so long that they are difficult to control, catch in turning parts and cause safety problems.
- coolant
coolant
Fluid that reduces temperature buildup at the tool/workpiece interface during machining. Normally takes the form of a liquid such as soluble or chemical mixtures (semisynthetic, synthetic) but can be pressurized air or other gas. Because of water’s ability to absorb great quantities of heat, it is widely used as a coolant and vehicle for various cutting compounds, with the water-to-compound ratio varying with the machining task. See cutting fluid; semisynthetic cutting fluid; soluble-oil cutting fluid; synthetic cutting fluid.
- land
land
Part of the tool body that remains after the flutes are cut.
- physical vapor deposition ( PVD)
physical vapor deposition ( PVD)
Tool-coating process performed at low temperature (500° C), compared to chemical vapor deposition (1,000° C). Employs electric field to generate necessary heat for depositing coating on a tool’s surface. See CVD, chemical vapor deposition.
- rake
rake
Angle of inclination between the face of the cutting tool and the workpiece. If the face of the tool lies in a plane through the axis of the workpiece, the tool is said to have a neutral, or zero, rake. If the inclination of the tool face makes the cutting edge more acute than when the rake angle is zero, the rake is positive. If the inclination of the tool face makes the cutting edge less acute or more blunt than when the rake angle is zero, the rake is negative.
- relief
relief
Space provided behind the cutting edges to prevent rubbing. Sometimes called primary relief. Secondary relief provides additional space behind primary relief. Relief on end teeth is axial relief; relief on side teeth is peripheral relief.
- stainless steels
stainless steels
Stainless steels possess high strength, heat resistance, excellent workability and erosion resistance. Four general classes have been developed to cover a range of mechanical and physical properties for particular applications. The four classes are: the austenitic types of the chromium-nickel-manganese 200 series and the chromium-nickel 300 series; the martensitic types of the chromium, hardenable 400 series; the chromium, nonhardenable 400-series ferritic types; and the precipitation-hardening type of chromium-nickel alloys with additional elements that are hardenable by solution treating and aging.
- swarf
swarf
Metal fines and grinding wheel particles generated during grinding.