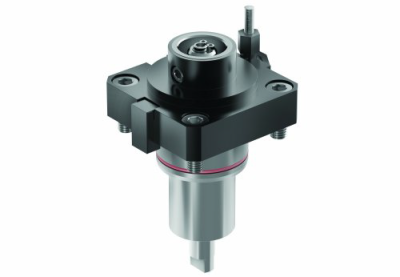
As machine tools become increasingly complex and the need to produce parts in less time grows, CNC lathe owners and managers must look to the latest technologies if they’re to improve shop floor efficiency. Isn’t it ironic then that one of the most productive of these solutions is far from new—in fact, it’s been a champion in the war on machine tool downtime for nearly three decades. It’s called KMTM Quick Change Tooling, and whether it’s an old friend, a complete stranger, or an acquaintance you met briefly and discounted, it’s time to take a long hard look at what it can do for your bottom line.
That’s because Kennametal is changing the rules of quick-change once again. The Latrobe, Pa., tooling provider launches an entirely new KMTM product line: turret-adapted clamping units. What’s more, Kennametal has partnered with global lathe tool specialist, EWS Tool Technologies, to manufacture and support this series of KM adapters. Together, the two companies plan to redefine how shops will tool up the turrets on their DMG Mori, Okuma, Mazak, Haas, Doosan, Nakamura, Hwacheon, and Hyundai lathes, with more to come.
Maybe you’ve looked at quick-change tooling in the past and said it’s not for you. Too expensive, perhaps, or not worth the hassle that comes with implementing any new technology. That might be why an overwhelming majority of machine shops apparently choose to take the path of least resistance and use the standard turret tooling that came with their CNC lathe. “I spoke to a lot of customers at last IMTS and EMO show, and my best estimate is that 80-percent of them do not use a quick-change tooling system,” says Michael Schuffenhauer, manager tooling systems at
Kennametal. “I was very surprised, and to me, it indicates a tremendous opportunity for these shops to become more competitive.”
Turret adapted clamping units support this opportunity by replacing the standard block-style turret tooling with quick-change capable adapters made specifically for your brand of CNC lathe. This is true for both VDI and BMT-style turrets, whether they are rotating or static, and for toolholders with axial, radial, and even angular orientation.
Suddenly quick-change is much easier to implement. Total tooling costs are reduced. Concerns over toolholder rigidity are eliminated. And because each clamping unit model was created by EWS to be a perfect match for prescribed machine tool builders, it’s as if the machines were designed with a KM turret.
“Available machining time is one of the key contributors to any manufacturing company’s productivity,” notes Schuffenhauer. “Obviously, reducing setup is a big part of improving this metric, something that quick-change tooling systems excel at. But there’s also the downtime that comes during tool changes, when the operator spends ten minutes looking for the screw that fell in to the chip pan, for example, or the time lost by having to touch off a drill in the middle of a job. KM eliminates this nonproductive time, and turret adapted clamping units are the bridge between the system’s quick-change capabilities and the machine tool.”
This bridge is both robust and comprehensive. Offset and inline clamping unit models are available, as are ones for right or left-hand placement. Hydraulic chucks, ER-collet holders, shell mill adapters, ID and OD turning cutting units after close to thirty years of development, the list of KM adapters is extensive. So too is the clamping unit size range, with interfaces ranging from 32 to 63 mm (KM32 to KM63). So whether your lathe, mill-turn machine, or multitasking center produces tiny medical screws or bearing hubs large enough for a tractor trailer, turret adapted clamping units
and KM have you covered.
But what is KM, and why is it better than the competition? For those unfamiliar with this mature and accepted system, Schuffenhauer offers the following explanation. “KM uses a pair of hardened steel balls that sit within a tapered tool shank. As clamping force is applied, the tail end of the taper expands while the toolholder is pulled back against the locating face. Together with a small amount of interference at the gage line, this three-point contact provides extremely precise radial and axial positioning and repeatability, as well as high clamping forces. Simply put, it is the most rigid and accurate quick-change system available in this size range.”
Ready to take a look, (or maybe a second look) but still concerned about the cost? Jay Verellen, Kennametal director of global product management, tooling systems, points to the ROI calculator on Kennametal.com as a way to quantify improvements in machine utilization. He notes that a potential positive return on investment (ROI) in as little as three to six months is not unusual, and that the company’s Customer Application Support (CAS) team is ready to help customers ensure they are getting the value they seek.
“It’s not a terribly complex calculation,” he says. “Enter a few inputs such as hourly rate and number of setups per shift and it’ll make sense pretty quickly. But you also need to consider the less tangible effects of KM. Setups and in-process tool changes are simpler, so having a less skilled operator isn’t a scary proposition. And flexibility is greatly increased. This doesn’t refer so much to the wide variety of tools and adapters that are available (although this is certainly important) but is more about the flexibility to make your customer happy—if you can set up a machine in five minutes, it becomes much easier to meet their changing demands without losing your shirt. That’s what KM and turret adapted clamping units bring to the table.”
Contact Details
Related Glossary Terms
- computer numerical control ( CNC)
computer numerical control ( CNC)
Microprocessor-based controller dedicated to a machine tool that permits the creation or modification of parts. Programmed numerical control activates the machine’s servos and spindle drives and controls the various machining operations. See DNC, direct numerical control; NC, numerical control.
- inner diameter ( ID)
inner diameter ( ID)
Dimension that defines the inside diameter of a cavity or hole. See OD, outer diameter.
- lathe
lathe
Turning machine capable of sawing, milling, grinding, gear-cutting, drilling, reaming, boring, threading, facing, chamfering, grooving, knurling, spinning, parting, necking, taper-cutting, and cam- and eccentric-cutting, as well as step- and straight-turning. Comes in a variety of forms, ranging from manual to semiautomatic to fully automatic, with major types being engine lathes, turning and contouring lathes, turret lathes and numerical-control lathes. The engine lathe consists of a headstock and spindle, tailstock, bed, carriage (complete with apron) and cross slides. Features include gear- (speed) and feed-selector levers, toolpost, compound rest, lead screw and reversing lead screw, threading dial and rapid-traverse lever. Special lathe types include through-the-spindle, camshaft and crankshaft, brake drum and rotor, spinning and gun-barrel machines. Toolroom and bench lathes are used for precision work; the former for tool-and-die work and similar tasks, the latter for small workpieces (instruments, watches), normally without a power feed. Models are typically designated according to their “swing,” or the largest-diameter workpiece that can be rotated; bed length, or the distance between centers; and horsepower generated. See turning machine.
- lathe bit ( lathe tool)
lathe bit ( lathe tool)
Cutting tool for lathes and other turning machines. Normally a single-point cutting tool, square in cross section and ground to a shape suitable for the material and task. Intended for simple metal removal, threading, slotting or other internal or external cutting jobs. Clearance to prevent rubbing is provided by grinding back rake, side rake, end relief and side relief, as well as side- and end-cutting edges.
- milling machine ( mill)
milling machine ( mill)
Runs endmills and arbor-mounted milling cutters. Features include a head with a spindle that drives the cutters; a column, knee and table that provide motion in the three Cartesian axes; and a base that supports the components and houses the cutting-fluid pump and reservoir. The work is mounted on the table and fed into the rotating cutter or endmill to accomplish the milling steps; vertical milling machines also feed endmills into the work by means of a spindle-mounted quill. Models range from small manual machines to big bed-type and duplex mills. All take one of three basic forms: vertical, horizontal or convertible horizontal/vertical. Vertical machines may be knee-type (the table is mounted on a knee that can be elevated) or bed-type (the table is securely supported and only moves horizontally). In general, horizontal machines are bigger and more powerful, while vertical machines are lighter but more versatile and easier to set up and operate.
- outer diameter ( OD)
outer diameter ( OD)
Dimension that defines the exterior diameter of a cylindrical or round part. See ID, inner diameter.
- shank
shank
Main body of a tool; the portion of a drill or similar end-held tool that fits into a collet, chuck or similar mounting device.
- toolholder
toolholder
Secures a cutting tool during a machining operation. Basic types include block, cartridge, chuck, collet, fixed, modular, quick-change and rotating.
- turning
turning
Workpiece is held in a chuck, mounted on a face plate or secured between centers and rotated while a cutting tool, normally a single-point tool, is fed into it along its periphery or across its end or face. Takes the form of straight turning (cutting along the periphery of the workpiece); taper turning (creating a taper); step turning (turning different-size diameters on the same work); chamfering (beveling an edge or shoulder); facing (cutting on an end); turning threads (usually external but can be internal); roughing (high-volume metal removal); and finishing (final light cuts). Performed on lathes, turning centers, chucking machines, automatic screw machines and similar machines.