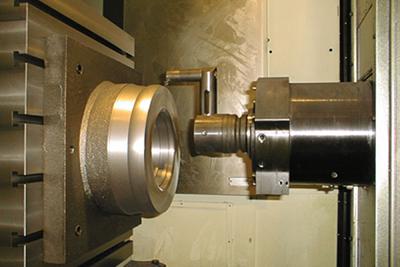
Okuma America Corp. introduces its Turn-Cut function, which allows for processing work on horizontal machining centers without the need to use secondary machinery for a turning application. Turn-Cut is available as an option on Okuma's MA and MB series of horizontal machining centers and, in some cases, can also be retrofitted to an existing Okuma machining center.
Turn-Cut is a programming option available on Okuma horizontal machining centers that allows the machine to create bores and diameters that include circular and/or angular features. This enables users to turn features on large, unbalanced parts on the same platform where standard CNC machining functions are performed, eliminating the need to purchase special-purpose machines, tooling, fixtures or add-on components. Adding the Turn-Cut functionality to a machining center does not interfere with performance or longevity of the machine, and often enhances performance with the addition of abso-scales and in some cases, Super-NURBS.
Cutting is performed on a horizontal machining center with the Turn-Cut function by synchronizing the circular motion of the feed axis with the spindle's turning angle (tool tip position control). The surfaces created by Turn-Cut can be either on the outside or inside diameter of the machined part.
Contact Details
Related Glossary Terms
- centers
centers
Cone-shaped pins that support a workpiece by one or two ends during machining. The centers fit into holes drilled in the workpiece ends. Centers that turn with the workpiece are called “live” centers; those that do not are called “dead” centers.
- computer numerical control ( CNC)
computer numerical control ( CNC)
Microprocessor-based controller dedicated to a machine tool that permits the creation or modification of parts. Programmed numerical control activates the machine’s servos and spindle drives and controls the various machining operations. See DNC, direct numerical control; NC, numerical control.
- feed
feed
Rate of change of position of the tool as a whole, relative to the workpiece while cutting.
- machining center
machining center
CNC machine tool capable of drilling, reaming, tapping, milling and boring. Normally comes with an automatic toolchanger. See automatic toolchanger.
- turning
turning
Workpiece is held in a chuck, mounted on a face plate or secured between centers and rotated while a cutting tool, normally a single-point tool, is fed into it along its periphery or across its end or face. Takes the form of straight turning (cutting along the periphery of the workpiece); taper turning (creating a taper); step turning (turning different-size diameters on the same work); chamfering (beveling an edge or shoulder); facing (cutting on an end); turning threads (usually external but can be internal); roughing (high-volume metal removal); and finishing (final light cuts). Performed on lathes, turning centers, chucking machines, automatic screw machines and similar machines.