Contact Details
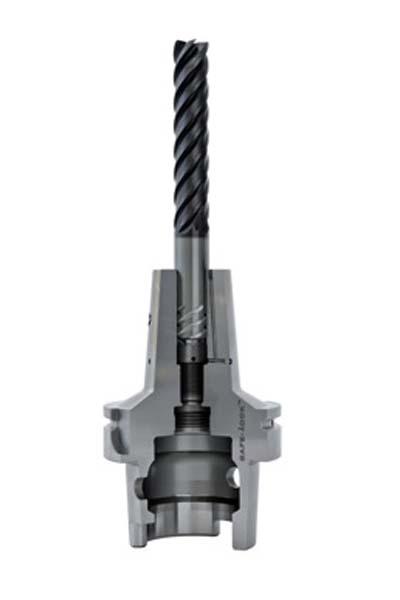
WIDIA can now offer customers the SAFE-LOCK system by Haimer. The SAFE-LOCK system is a pull-out-protection and adapter system for round-shanked cutting tools that enhances security in heavy-duty cutting. It combines a positive locking feature with on-center high accuracy for improved process reliability, longer cutting tool life and higher productivity.
The continuing development of advanced high-strength, lightweight materials such as titanium alloys, INCONEL and new aluminium alloys are being investigated by manufacturers in many industries, including aerospace and defense, energy and transportation. Not only do these new materials present significant machining challenges, competitive pressures in these global industries make finding efficient manufacturing solutions a priority.
"This has become increasingly evident in the last few years, ever since high-performance cutting tools that facilitate this type of machining have been on the market," says Doug Ewald, lead product manager for WIDIA tooling systems. "Many industries are upgrading their manufacturing resources (machine tools, cutting tools and toolholding systems) that can withstand the high torques, feeds and forces to ensure that the operation doesn't fail and potentially scrap expensive parts."
The danger of milling cutters being pulled out of the toolholder at these extreme forces has significantly increased. Such toolholders like shrink fit work with friction alone for locking. They have great accuracy, but their clamping force can be insufficient for roughing operations.
The standard industry response for years has been to require Weldon shanks on cutting tools. The Weldon straight shank with a drive flat for locking in place with a clamping screw was developed to compensate for pullout forces, and to drive the end mill as hard as possible in roughing and other high-metal-removal operations. It is estimated that about 70 percent of all users use standard Weldon holders for heavy roughing due to security concerns, because the clamping screw creates a positive locking. Tool accuracy and run-out is poor, however, due to characteristic offset and one line contact of the cutting tool in the holder bore. This also contributes to shorter tool life.
SAFE-LOCK is a pull-out protection system for round-shanked cutting tools. Helical grooves are ground into the shank of the tool. These together with the respective pin drivers in the holder prevent the tool from spinning or being pulled out of the holder altogether under extreme machining conditions. Because the helical path of the SAFE-LOCK grooves means that the length of the tools can be adjusted, tools can be reground and preset as usual.
SAFE-LOCK can be combined with the latest toolholder systems, such as shrink-fit technology, because it can be used for both high-speed as well as heavy chip removal situations. The chuck is heated as usual and the tool inserted with a slightly twisting movement. The locking elements of the SAFE-LOCK system find their own way into the grooves when the tool is turned into the locking position. A spring can be used to aid in the play-free positioning of the tool. The holder cools down after a few seconds, creating the press fit and positive locking.
Concentric accuracy of +/-3µm (0.00012") is achieved during shrinking, a value that is 10 times better than any standard clamping in Weldon chucks. The stable and accurate tool clamping achieved in this way allows users to machine even greater cutting depths with higher feed rates. The tangible benefits: time savings, enhanced productivity, lower scrap rates, less vibration and operator peace of mind.
Related Glossary Terms
- alloys
alloys
Substances having metallic properties and being composed of two or more chemical elements of which at least one is a metal.
- chuck
chuck
Workholding device that affixes to a mill, lathe or drill-press spindle. It holds a tool or workpiece by one end, allowing it to be rotated. May also be fitted to the machine table to hold a workpiece. Two or more adjustable jaws actually hold the tool or part. May be actuated manually, pneumatically, hydraulically or electrically. See collet.
- feed
feed
Rate of change of position of the tool as a whole, relative to the workpiece while cutting.
- flat ( screw flat)
flat ( screw flat)
Flat surface machined into the shank of a cutting tool for enhanced holding of the tool.
- gang cutting ( milling)
gang cutting ( milling)
Machining with several cutters mounted on a single arbor, generally for simultaneous cutting.
- milling
milling
Machining operation in which metal or other material is removed by applying power to a rotating cutter. In vertical milling, the cutting tool is mounted vertically on the spindle. In horizontal milling, the cutting tool is mounted horizontally, either directly on the spindle or on an arbor. Horizontal milling is further broken down into conventional milling, where the cutter rotates opposite the direction of feed, or “up” into the workpiece; and climb milling, where the cutter rotates in the direction of feed, or “down” into the workpiece. Milling operations include plane or surface milling, endmilling, facemilling, angle milling, form milling and profiling.
- milling machine ( mill)
milling machine ( mill)
Runs endmills and arbor-mounted milling cutters. Features include a head with a spindle that drives the cutters; a column, knee and table that provide motion in the three Cartesian axes; and a base that supports the components and houses the cutting-fluid pump and reservoir. The work is mounted on the table and fed into the rotating cutter or endmill to accomplish the milling steps; vertical milling machines also feed endmills into the work by means of a spindle-mounted quill. Models range from small manual machines to big bed-type and duplex mills. All take one of three basic forms: vertical, horizontal or convertible horizontal/vertical. Vertical machines may be knee-type (the table is mounted on a knee that can be elevated) or bed-type (the table is securely supported and only moves horizontally). In general, horizontal machines are bigger and more powerful, while vertical machines are lighter but more versatile and easier to set up and operate.
- shank
shank
Main body of a tool; the portion of a drill or similar end-held tool that fits into a collet, chuck or similar mounting device.
- toolholder
toolholder
Secures a cutting tool during a machining operation. Basic types include block, cartridge, chuck, collet, fixed, modular, quick-change and rotating.