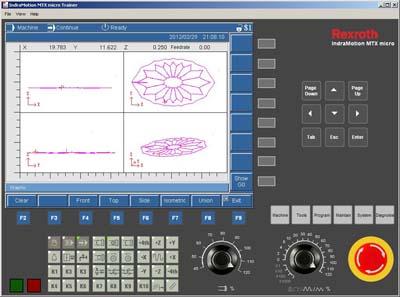
The IndraMotion MTX micro Trainer from Bosch Rexroth gives machine operators the ability to simulate, develop, test and transfer CNC programs from a personal computer without disrupting production. Available as a free download from www.boschrexroth-us.com/MTXmicro, this easy-to-use software package provides a machine-like representation of Rexroth's IndraMotion MTX micro CNC user interface.
Designed for tool operators, machine builders, instructors and students, the training software offers realistic operation and programming capabilities for milling, turning and drilling sequences, independent of any machine tool hardware. The program runs on Microsoft Windows XP or Windows 7 operating systems with no licensing required.
Part of the company's IndraMotion MTX platform, the MTX micro is Rexroth's low-cost compact CNC solution for standard machining applications. It consists of a compact HMI interface and a powerful multi-axis drive controller with performance CNC and PLC control.
The MTX micro Trainer can be used independently, or to support the development and optimization of an MTX micro CNC system control. Users can choose between pre-configured lathe and milling machine scenarios. The software includes features and simulation sequences drawn from Rexroth's in-depth experience developing robust CNC platforms.
Trainees can use this CNC trainer to set up and operate a wide range of functions, correct errors and test their skills on simulations — all without interrupting machine production. Users can practice configuring the tool list, plot tool movement in various views and develop greater familiarity and efficiency with CNC tools.
As a development resource, operators can use it to simulate sequences and to test and debug programs and fixes in a realistic environment, helping to streamline CNC program development offline.
CNC programs can also be imported, modified and exported after testing and fine-tuning. The sample milling and turning demo programs can be used to create workable CNC programs. Built-in help systems for operation and NC-functionality, g-codes and cycles are also available.
For those seeking to purchase a compact CNC system, the MTX micro Trainer is also useful for previewing the features and capabilities of Rexroth's IndraMotion MTX micro CNC platform.
Contact Details
Related Glossary Terms
- computer numerical control ( CNC)
computer numerical control ( CNC)
Microprocessor-based controller dedicated to a machine tool that permits the creation or modification of parts. Programmed numerical control activates the machine’s servos and spindle drives and controls the various machining operations. See DNC, direct numerical control; NC, numerical control.
- gang cutting ( milling)
gang cutting ( milling)
Machining with several cutters mounted on a single arbor, generally for simultaneous cutting.
- lathe
lathe
Turning machine capable of sawing, milling, grinding, gear-cutting, drilling, reaming, boring, threading, facing, chamfering, grooving, knurling, spinning, parting, necking, taper-cutting, and cam- and eccentric-cutting, as well as step- and straight-turning. Comes in a variety of forms, ranging from manual to semiautomatic to fully automatic, with major types being engine lathes, turning and contouring lathes, turret lathes and numerical-control lathes. The engine lathe consists of a headstock and spindle, tailstock, bed, carriage (complete with apron) and cross slides. Features include gear- (speed) and feed-selector levers, toolpost, compound rest, lead screw and reversing lead screw, threading dial and rapid-traverse lever. Special lathe types include through-the-spindle, camshaft and crankshaft, brake drum and rotor, spinning and gun-barrel machines. Toolroom and bench lathes are used for precision work; the former for tool-and-die work and similar tasks, the latter for small workpieces (instruments, watches), normally without a power feed. Models are typically designated according to their “swing,” or the largest-diameter workpiece that can be rotated; bed length, or the distance between centers; and horsepower generated. See turning machine.
- milling
milling
Machining operation in which metal or other material is removed by applying power to a rotating cutter. In vertical milling, the cutting tool is mounted vertically on the spindle. In horizontal milling, the cutting tool is mounted horizontally, either directly on the spindle or on an arbor. Horizontal milling is further broken down into conventional milling, where the cutter rotates opposite the direction of feed, or “up” into the workpiece; and climb milling, where the cutter rotates in the direction of feed, or “down” into the workpiece. Milling operations include plane or surface milling, endmilling, facemilling, angle milling, form milling and profiling.
- milling machine ( mill)
milling machine ( mill)
Runs endmills and arbor-mounted milling cutters. Features include a head with a spindle that drives the cutters; a column, knee and table that provide motion in the three Cartesian axes; and a base that supports the components and houses the cutting-fluid pump and reservoir. The work is mounted on the table and fed into the rotating cutter or endmill to accomplish the milling steps; vertical milling machines also feed endmills into the work by means of a spindle-mounted quill. Models range from small manual machines to big bed-type and duplex mills. All take one of three basic forms: vertical, horizontal or convertible horizontal/vertical. Vertical machines may be knee-type (the table is mounted on a knee that can be elevated) or bed-type (the table is securely supported and only moves horizontally). In general, horizontal machines are bigger and more powerful, while vertical machines are lighter but more versatile and easier to set up and operate.
- turning
turning
Workpiece is held in a chuck, mounted on a face plate or secured between centers and rotated while a cutting tool, normally a single-point tool, is fed into it along its periphery or across its end or face. Takes the form of straight turning (cutting along the periphery of the workpiece); taper turning (creating a taper); step turning (turning different-size diameters on the same work); chamfering (beveling an edge or shoulder); facing (cutting on an end); turning threads (usually external but can be internal); roughing (high-volume metal removal); and finishing (final light cuts). Performed on lathes, turning centers, chucking machines, automatic screw machines and similar machines.