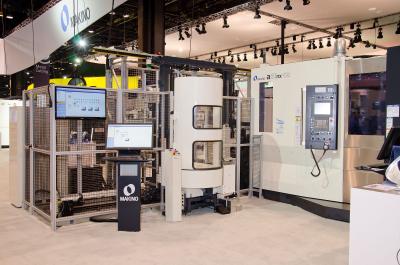
Automation is essential in helping manufacturers achieve maximum return on investment from their machine tools. Makino offers the availability of a new design configuration for its MMC2 automated pallet-handling system, which enables full compatibility with the company’s a61nx-5E 5-axis horizontal machining center. Together, these technologies offer a combination of processing speed and flexibility, giving aerospace manufacturers more control over their workflow and the ability to adapt quickly to customers’ just-in-time needs for complex, multidimension part applications.
The updated MMC2 retains the same modular design and capabilities of its predecessors, but with a new pallet-transfer interface on the system’s rail-guided vehicle. This interface can handle the unique pallet designs used on the a61nx-5E. As a result, manufacturers are able to achieve spindle utilization rates upwards of 95 percent to further maximize the value of their a61nx-5E investment, according to the company.
“Based on feedback from current a61nx-5E owners, we’d come to realize that the machine’s productive capabilities were so high that most operators were struggling to keep their machines fed with raw materials,” said David Ward, product marketing manager at Makino. “While we see this as a good problem to have, it is still an issue that we wanted to address. By providing this optional pallet interface on the MMC2, we’re able to help manufacturers keep up with the productivity rates of the a61nx-5E to get the most value out of their investments.”
The MMC2 is designed to accommodate up to 15 machining centers and four work-setting stations into a single system. Each system can hold up to 200 pallet stockers—stacked either one, two or three layers high—with a virtually unlimited variety of parts and fixtures.
The system’s RGV is supported by a floor rail and upper-guide rail for enhanced stability and simultaneous, high-speed movement. The system’s work-setting stations (WSS) provide easy access for operators to load and unload parts either by hand or crane. Each WSS has 180-degree pivoting doors to save space and prevent a cluttered work area. The MMC2 can be equipped with optional workpiece washing guns.
Users of the MMC2 frequently report spindle utilization rate improvements of up to 95 percent, leading to dramatic increases in production without adding staff or equipment. The MMC2 system permits users to virtually eliminate part setup time, reducing non-value-added time in their machining operations. By providing a continual flow of parts to the a61nx-5E, the system can run for extended periods unattended, including over nights and weekends.
The updated MMC2 retains the same Microsoft Windows-based MAS-A5 control software, which helps maximize production output while monitoring multimachine production requirements. The MAS-A5 main PC hard drive stores and manages all NC programs for optimal machine utilization, including NC programs that exceed CNC memory. With these storage capabilities, there is practically no limit to the number of fixtures and associated process sequences and offsets that can be logically assigned to an individual pallet.
Tool data, both in and out of the a61nx-5E machines, can be accessed and modified from the MAS-A5 user interface. A variety of file formats for tooling and part information are supported and can be displayed to assist with part loading/unloading and tool-setting operations. The Tool-Life Predict function enables the MAS-A5 to gather tool-life data per NC program. When a request is opened, this function informs the operator of how long a tool is used in each NC program execution, as well as how many spare tools per machine are required to finish any work that is currently loaded or awaiting processing at the time that the request was placed. The MAS-A5 then schedules work only for the machines that meet tool-life and availability requirements for the desired process sequence. Interfacing with a tool presetter also reduces errors by automatically capturing tool-offset data, which can be transferred from the presetter to the MAS-A5 system control.
Standard control features include in-cell production scheduling, equipment status monitoring, NC program management and on-board reporting. These capabilities enable the MMC2 to assign work and initiate operations automatically, based on machine and material availability, using maximum spindle capabilities and monitoring all automated procedures.
Contact Details
Related Glossary Terms
- centers
centers
Cone-shaped pins that support a workpiece by one or two ends during machining. The centers fit into holes drilled in the workpiece ends. Centers that turn with the workpiece are called “live” centers; those that do not are called “dead” centers.
- computer numerical control ( CNC)
computer numerical control ( CNC)
Microprocessor-based controller dedicated to a machine tool that permits the creation or modification of parts. Programmed numerical control activates the machine’s servos and spindle drives and controls the various machining operations. See DNC, direct numerical control; NC, numerical control.
- just-in-time ( JIT)
just-in-time ( JIT)
Philosophy based on identifying, then removing, impediments to productivity. Applies to machining processes, inventory control, rejects, changeover time and other elements affecting production.
- machining center
machining center
CNC machine tool capable of drilling, reaming, tapping, milling and boring. Normally comes with an automatic toolchanger. See automatic toolchanger.
- modular design ( modular construction)
modular design ( modular construction)
Manufacturing of a product in subassemblies that permits fast and simple replacement of defective assemblies and tailoring of the product for different purposes. See interchangeable parts.
- numerical control ( NC)
numerical control ( NC)
Any controlled equipment that allows an operator to program its movement by entering a series of coded numbers and symbols. See CNC, computer numerical control; DNC, direct numerical control.