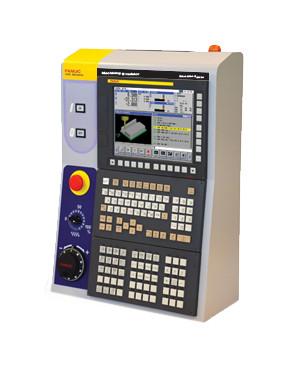
FANUC America has developed a new machining simulator that encompasses the complete manufacturing process from part design and engineering to CNC programming to virtual production simulation. The FANUC Machining Simulator features Autodesk Fusion 360 CAD/CAM/CAE software and a custom machining simulation program designed by ModuleWorks.
The FANUC Machining Simulator comes with Fusion 360, a cloud-based 3D CAD, CAM and CAE software platform that helps bridge the gap between design and machining and works on both Mac and PC. Students can use Fusion 360 to perform CAD/CAM work and the included post processors will convert the designs into G-code suitable for the included CNC. The CNC will use this G code to command the machine tool. The simulation system also includes a simple G-code editor for making modifications before the program is sent to the CNC. Students can easily import their programs directly to the CNC using the FANUC FASBacCNC user interface and also back-up the critical CNC data.
The core of the system is the flexible and powerful FANUC CNC Simulator. This portable CNC Simulator provides users with the experience of working with real look and feel of a true hardware-based FANUC control. Based on the industry standard FANUC Series 0i-Model F, the CNC Simulator can be operated as either a 3-axis mill or a 2-axis lathe. Users can run programs, manage tooling and make any modifications on the control just like they would in a manufacturing environment. The FANUC CNC Simulator includes FANUC Manual Guide i conversational programming software for users who would like to learn shop floor programming. An integrated PC is embedded in the FANUC CNC Simulator to run the Fusion 360 and ModuleWorks simulation software.
The machining simulation component was developed in partnership with ModuleWorks, a leading supplier of CAD/CAM components for toolpath generation and simulation. Users can virtually manufacture parts in milling or turning environments with realistic kinematics and structure. The simulation is based on actual CNC position data, not on the G-code program, this provides the most realistic simulation as the virtual machine reacts exactly as a real machine. Manual machine functions like jog, hand-wheel and reference cycles also work exactly like a real machine. The software also uses color-coded tool paths, back-plot and cut locations to make it easy for users to identify the tool, path and cutting result. Real-time collision detection uses visual and audio signals to notify users of collisions. The milling simulation includes a 21-tool changer and the turning simulation includes a 12-tool turret. Milling tool data can be freely assigned or imported from the CNC Simulator, while turning uses a predefined set of turning tools that cover a wide range of applications.
Fusion 360 is free for students, startups, educators and hobbyists once they create an Autodesk account. Commercial users can sign up for a free 1-year subscription through a special promotion with FANUC.
Contact Details
Related Glossary Terms
- computer numerical control ( CNC)
computer numerical control ( CNC)
Microprocessor-based controller dedicated to a machine tool that permits the creation or modification of parts. Programmed numerical control activates the machine’s servos and spindle drives and controls the various machining operations. See DNC, direct numerical control; NC, numerical control.
- computer-aided design ( CAD)
computer-aided design ( CAD)
Product-design functions performed with the help of computers and special software.
- computer-aided engineering ( CAE)
computer-aided engineering ( CAE)
Engineering functions performed with the help of computers and special software. Includes functions such as determining a material’s ability to withstand stresses.
- computer-aided manufacturing ( CAM)
computer-aided manufacturing ( CAM)
Use of computers to control machining and manufacturing processes.
- conversational programming
conversational programming
Method for using plain English to produce G-code file without knowing G-code in order to program CNC machines.
- gang cutting ( milling)
gang cutting ( milling)
Machining with several cutters mounted on a single arbor, generally for simultaneous cutting.
- lathe
lathe
Turning machine capable of sawing, milling, grinding, gear-cutting, drilling, reaming, boring, threading, facing, chamfering, grooving, knurling, spinning, parting, necking, taper-cutting, and cam- and eccentric-cutting, as well as step- and straight-turning. Comes in a variety of forms, ranging from manual to semiautomatic to fully automatic, with major types being engine lathes, turning and contouring lathes, turret lathes and numerical-control lathes. The engine lathe consists of a headstock and spindle, tailstock, bed, carriage (complete with apron) and cross slides. Features include gear- (speed) and feed-selector levers, toolpost, compound rest, lead screw and reversing lead screw, threading dial and rapid-traverse lever. Special lathe types include through-the-spindle, camshaft and crankshaft, brake drum and rotor, spinning and gun-barrel machines. Toolroom and bench lathes are used for precision work; the former for tool-and-die work and similar tasks, the latter for small workpieces (instruments, watches), normally without a power feed. Models are typically designated according to their “swing,” or the largest-diameter workpiece that can be rotated; bed length, or the distance between centers; and horsepower generated. See turning machine.
- milling
milling
Machining operation in which metal or other material is removed by applying power to a rotating cutter. In vertical milling, the cutting tool is mounted vertically on the spindle. In horizontal milling, the cutting tool is mounted horizontally, either directly on the spindle or on an arbor. Horizontal milling is further broken down into conventional milling, where the cutter rotates opposite the direction of feed, or “up” into the workpiece; and climb milling, where the cutter rotates in the direction of feed, or “down” into the workpiece. Milling operations include plane or surface milling, endmilling, facemilling, angle milling, form milling and profiling.
- milling machine ( mill)
milling machine ( mill)
Runs endmills and arbor-mounted milling cutters. Features include a head with a spindle that drives the cutters; a column, knee and table that provide motion in the three Cartesian axes; and a base that supports the components and houses the cutting-fluid pump and reservoir. The work is mounted on the table and fed into the rotating cutter or endmill to accomplish the milling steps; vertical milling machines also feed endmills into the work by means of a spindle-mounted quill. Models range from small manual machines to big bed-type and duplex mills. All take one of three basic forms: vertical, horizontal or convertible horizontal/vertical. Vertical machines may be knee-type (the table is mounted on a knee that can be elevated) or bed-type (the table is securely supported and only moves horizontally). In general, horizontal machines are bigger and more powerful, while vertical machines are lighter but more versatile and easier to set up and operate.
- toolpath( cutter path)
toolpath( cutter path)
2-D or 3-D path generated by program code or a CAM system and followed by tool when machining a part.
- turning
turning
Workpiece is held in a chuck, mounted on a face plate or secured between centers and rotated while a cutting tool, normally a single-point tool, is fed into it along its periphery or across its end or face. Takes the form of straight turning (cutting along the periphery of the workpiece); taper turning (creating a taper); step turning (turning different-size diameters on the same work); chamfering (beveling an edge or shoulder); facing (cutting on an end); turning threads (usually external but can be internal); roughing (high-volume metal removal); and finishing (final light cuts). Performed on lathes, turning centers, chucking machines, automatic screw machines and similar machines.