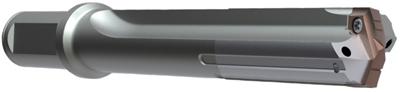
Allied Machine & Engineering Corp. presents its Guided T-A and 3XL drilling systems for deep-hole drilling applications. The two systems provide predictable and confident deep-hole machining and tool life increases of up to 50 percent with inserts available in the high-heat-resistant AM200 coating, according to the company.
Guided T-A provides for tighter, true position and a straighter hole throughout the operation, providing penetration rates of up to twice that of a gundrill. Engineered for breaking out on uneven surfaces, Guided T-A is available in carbide-clad and chrome-plated styles and can be used with standard T-A and GEN2 T-A, HSS or carbide blades.
3XL, the longest of the T-A style holders, is available in helical or straight flute designs; lathe, Morse taper, or Flange style shanks; and lengths from 1xD up to 28xD (stocked).
Contact Details
Related Glossary Terms
- gundrill
gundrill
Self-guided drill for producing deep holes with good accuracy and fine surface finish. Has coolant passages that deliver coolant to the tool/workpiece interface at high pressure.
- high-speed steels ( HSS)
high-speed steels ( HSS)
Available in two major types: tungsten high-speed steels (designated by letter T having tungsten as the principal alloying element) and molybdenum high-speed steels (designated by letter M having molybdenum as the principal alloying element). The type T high-speed steels containing cobalt have higher wear resistance and greater red (hot) hardness, withstanding cutting temperature up to 1,100º F (590º C). The type T steels are used to fabricate metalcutting tools (milling cutters, drills, reamers and taps), woodworking tools, various types of punches and dies, ball and roller bearings. The type M steels are used for cutting tools and various types of dies.
- lathe
lathe
Turning machine capable of sawing, milling, grinding, gear-cutting, drilling, reaming, boring, threading, facing, chamfering, grooving, knurling, spinning, parting, necking, taper-cutting, and cam- and eccentric-cutting, as well as step- and straight-turning. Comes in a variety of forms, ranging from manual to semiautomatic to fully automatic, with major types being engine lathes, turning and contouring lathes, turret lathes and numerical-control lathes. The engine lathe consists of a headstock and spindle, tailstock, bed, carriage (complete with apron) and cross slides. Features include gear- (speed) and feed-selector levers, toolpost, compound rest, lead screw and reversing lead screw, threading dial and rapid-traverse lever. Special lathe types include through-the-spindle, camshaft and crankshaft, brake drum and rotor, spinning and gun-barrel machines. Toolroom and bench lathes are used for precision work; the former for tool-and-die work and similar tasks, the latter for small workpieces (instruments, watches), normally without a power feed. Models are typically designated according to their “swing,” or the largest-diameter workpiece that can be rotated; bed length, or the distance between centers; and horsepower generated. See turning machine.