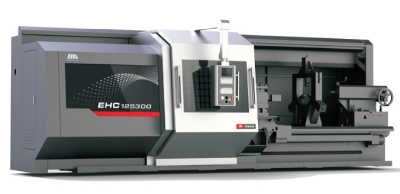
SMTCL has announced the development of a new horizontal turning center, the EHC125300. This machine reportedly demonstrates SMTCL’s commitment to United States’ job shop customers by allowing them to get a large high-quality machine tool at a cost-effective price.
SMTCL’s national sales representative, Chad Turner stated, “Previously, major companies were not able to outsource large turning work, because many job shops did not have the machine tools to do the work accurately or cost effectively.”
The EHC125300 is a precision CNC horizontal lathe featuring swing over the bed of 1250mm, or 49”. The machine also can handle parts up to 3 meters in length, or 118 inches.
Another new product, the EHC125500 can handle parts up to 5 meters, or 196 inches, in length. The machine can handle shaft parts weighing up to 11,000 lbs. The EHC125300 comes standard with a 1,000mm chuck, 8-position turret, steady rest, hydraulic tailstock and a chip conveyor.
Jerry McCarty, COO of SMTCL, added, “We use world-wide components on this machine. In addition to the high-quality FANUC 0i-TF control and FANUC Motors, the machine uses THK ballscrews from Japan, NSK spindle bearings from Japan, a German Stober gearbox, and a German Sauter turret. The machine weighs an amazing 44,000 lbs. and is priced under $300,000.”
Contact Details
Related Glossary Terms
- chuck
chuck
Workholding device that affixes to a mill, lathe or drill-press spindle. It holds a tool or workpiece by one end, allowing it to be rotated. May also be fitted to the machine table to hold a workpiece. Two or more adjustable jaws actually hold the tool or part. May be actuated manually, pneumatically, hydraulically or electrically. See collet.
- computer numerical control ( CNC)
computer numerical control ( CNC)
Microprocessor-based controller dedicated to a machine tool that permits the creation or modification of parts. Programmed numerical control activates the machine’s servos and spindle drives and controls the various machining operations. See DNC, direct numerical control; NC, numerical control.
- lathe
lathe
Turning machine capable of sawing, milling, grinding, gear-cutting, drilling, reaming, boring, threading, facing, chamfering, grooving, knurling, spinning, parting, necking, taper-cutting, and cam- and eccentric-cutting, as well as step- and straight-turning. Comes in a variety of forms, ranging from manual to semiautomatic to fully automatic, with major types being engine lathes, turning and contouring lathes, turret lathes and numerical-control lathes. The engine lathe consists of a headstock and spindle, tailstock, bed, carriage (complete with apron) and cross slides. Features include gear- (speed) and feed-selector levers, toolpost, compound rest, lead screw and reversing lead screw, threading dial and rapid-traverse lever. Special lathe types include through-the-spindle, camshaft and crankshaft, brake drum and rotor, spinning and gun-barrel machines. Toolroom and bench lathes are used for precision work; the former for tool-and-die work and similar tasks, the latter for small workpieces (instruments, watches), normally without a power feed. Models are typically designated according to their “swing,” or the largest-diameter workpiece that can be rotated; bed length, or the distance between centers; and horsepower generated. See turning machine.
- steady rest
steady rest
Supports long, thin or flexible work being turned on a lathe. Mounts on the bed’s ways and, unlike a follower rest, remains at the point where mounted. See follower rest.
- turning
turning
Workpiece is held in a chuck, mounted on a face plate or secured between centers and rotated while a cutting tool, normally a single-point tool, is fed into it along its periphery or across its end or face. Takes the form of straight turning (cutting along the periphery of the workpiece); taper turning (creating a taper); step turning (turning different-size diameters on the same work); chamfering (beveling an edge or shoulder); facing (cutting on an end); turning threads (usually external but can be internal); roughing (high-volume metal removal); and finishing (final light cuts). Performed on lathes, turning centers, chucking machines, automatic screw machines and similar machines.