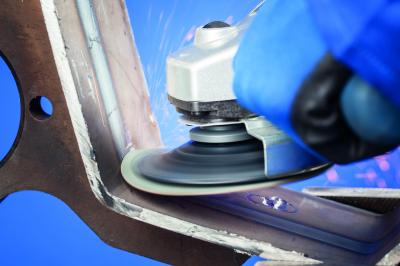
The patented COMBICLICK quick-change disc system from PFERD provides lower workpiece temperature while improving stock removal and disc life. Designed for use with coated abrasive, nonwoven and felt discs, the COMBICLICK system consists of a specially developed backing pad with an innovative locking mechanism. The threaded backing pad allows COMBICLICK discs to be used on most available angle grinders.
The special geometry of the cooling slots ensures a high throughput of air, thus significantly reducing the thermal load on the abrasive material and workpiece. This optimized cooling, together with the quick-mounting system, rugged fixture, and secure attachment of the disc allow COMBICLICK to provide up to 30% lower workpiece temperature, up to 25% increased stock removal, and up to 30% longer disc life.
The extensive range of COMBICLICK fiber discs provides the optimal product for any grinding application. PFERD offers fiber discs with various grit sizes, abrasives, and diameters of 4, 4-1/2, 5, and 7-inches, depending on the disc type. Applications include working on weld seams, deburring of steel components, rough grinding, fine grinding of stainless steel (INOX) components, removal of mill and casting skins, and working on narrow, hard to reach areas such as cooling ribs.
Varieties of COMBICLICK discs include fiber discs available in ceramic (CO) and aluminum oxide (AO), zirconia alumina (Z), silicon carbide (SiC), and COOL versions with active additives to prevent loading reducing heat build-up; non-woven unitized discs in hard through-soft types for use in face-down grinding on variable speed angle grinders; and felt discs for pre-polishing and high-gloss polishing. COMBICLICK backing pads permit the use of COMBICLICK discs on all common angle grinders. Plus, the patented mounting system minimizes disc changing time. The backing pads, like the discs, come in 4, 4-1/2, 5, and 7-inch sizes.
COMBICLICK kits offer a convenient way to get started with the system. A wide variety of coated and non-woven materials are included to test performance and surface finish results to help determine the ideal product selections for the customer's applications prior to bulk purchases. The included discs provide solutions for rough grinding, fine grinding, surface conditioning, pre-polish and polishing to a mirror finish.
Contact Details
Related Glossary Terms
- abrasive
abrasive
Substance used for grinding, honing, lapping, superfinishing and polishing. Examples include garnet, emery, corundum, silicon carbide, cubic boron nitride and diamond in various grit sizes.
- aluminum oxide
aluminum oxide
Aluminum oxide, also known as corundum, is used in grinding wheels. The chemical formula is Al2O3. Aluminum oxide is the base for ceramics, which are used in cutting tools for high-speed machining with light chip removal. Aluminum oxide is widely used as coating material applied to carbide substrates by chemical vapor deposition. Coated carbide inserts with Al2O3 layers withstand high cutting speeds, as well as abrasive and crater wear.
- backing
backing
1. Flexible portion of a bandsaw blade. 2. Support material behind the cutting edge of a tool. 3. Base material for coated abrasives.
- coated abrasive
coated abrasive
Flexible-backed abrasive. Grit is attached to paper, fiber, cloth or film. Types include sheets, belts, flap wheels and discs.
- fixture
fixture
Device, often made in-house, that holds a specific workpiece. See jig; modular fixturing.
- grinding
grinding
Machining operation in which material is removed from the workpiece by a powered abrasive wheel, stone, belt, paste, sheet, compound, slurry, etc. Takes various forms: surface grinding (creates flat and/or squared surfaces); cylindrical grinding (for external cylindrical and tapered shapes, fillets, undercuts, etc.); centerless grinding; chamfering; thread and form grinding; tool and cutter grinding; offhand grinding; lapping and polishing (grinding with extremely fine grits to create ultrasmooth surfaces); honing; and disc grinding.
- milling machine ( mill)
milling machine ( mill)
Runs endmills and arbor-mounted milling cutters. Features include a head with a spindle that drives the cutters; a column, knee and table that provide motion in the three Cartesian axes; and a base that supports the components and houses the cutting-fluid pump and reservoir. The work is mounted on the table and fed into the rotating cutter or endmill to accomplish the milling steps; vertical milling machines also feed endmills into the work by means of a spindle-mounted quill. Models range from small manual machines to big bed-type and duplex mills. All take one of three basic forms: vertical, horizontal or convertible horizontal/vertical. Vertical machines may be knee-type (the table is mounted on a knee that can be elevated) or bed-type (the table is securely supported and only moves horizontally). In general, horizontal machines are bigger and more powerful, while vertical machines are lighter but more versatile and easier to set up and operate.
- polishing
polishing
Abrasive process that improves surface finish and blends contours. Abrasive particles attached to a flexible backing abrade the workpiece.