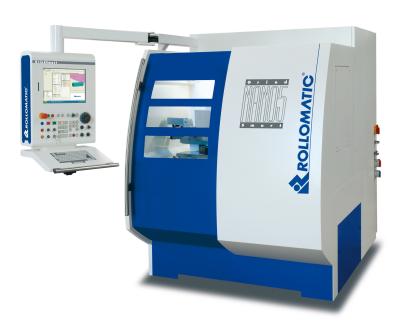
Rollomatic, a leading machine tool manufacturer based in Le Landeron, Switzerland, maintains its global leadership position in the dental industry by highlighting a number of upgraded models for manufacturing dentals rotary cutting tools. The various Rollomatic CNC grinding machines can be used for high-volume geometry grinding and blank preparation of a number of dental cutting tools, such as:
- Surgical and laboratory dental burs
- 1– or 2-piece construction, solid tungsten carbide, steel or stainless
- Gates-Glidden Rotary endodontic files
- Lindemann cutters
- Implant twist drills
- Implant taps
- Endmills for CAD/CAM dentistry
- and more
Dental tool grinding on the 5-axis GrindSmart® Nano5 grinding machine offers exceptional flexibility in comparison to conventional single-purpose grinders. With its 5 fully interpolating CNC axes and a pick-and-place automatic tool loader, the machine can easily be adapted for any type of dental cutting instrument, both for short and long runs.
Compared to 5-axis machines, the model CNC246F is a prime example of a dedicated and highly productive 3-axis fluting machines suitable for flute and relief grinding of rotary files. The machine is equipped with 2 grinding stations and a pick-and-place automatic loader. Highest productivity can be achieved due to its compact design. The machine is equally suited for flute/relief grinding of drills, taps, reamers and other rotary cutting tools. The GrindSmart® model 530XW 5-axis tool grinding machine with new and innovative capabilities relating to the production grinding of dental burs and rotary files is equipped with a pick-and-place automatic loader and a wheel/nozzle changer. The compact and versatile design allows full and user-friendly interchangeability between different tool types as well as industrial tools such as inserts and round-shank tools. The machine is particularly suited for grinding carbide endmills for the CAD/CAM dentistry.
With a choice of 4 and 5 CNC axes, both ShapeSmart® NP30 and NP50 precision pinch and peel grinding machines are based on the proven method of pinch grinding, a technology invented by Rollomatic, that ensures polished surface finishes and unmatched performances achieving micron precision. The machines are particularly suitable for cylindrical grinding or blank preparation of CAD/CAM endmills, drills and burs. Quick-change attachments can also be ground with these machines.
The RPG is a hydraulically operated precision plunge grinding machine for cylindrical grinding operations and blank preparations. The machine is equipped with a V-type magazine loader and is therefore suitable for unattended high volume production grinding. The shank guidance and following steady rest allow precise grinding results with a TIR below 1 micron. This machine is highly recommended for blank preparation of dental burs.
The Rollomatic 5-axis CNC tool grinders are equipped with tool design software called VirtualGrindPro which runs the multiaxis GrindSmart® series machines. In addition to the already extensive tool diversity, further tool geometries have been added both for dental tools as well as industrial cutting tools. Rollomatic’s strategy with this expansion is based on helping operators and programmers to facilitate an environment of efficiency and collaboration within the user’s organization. This powerful software offers the highest possible speed, ease-of-use and flexibility. These machines can switch over from dental to industrial tools in an operator-friendly and timely fashion.
In addition to the software expansion, the 3-dimensional simulator has been updated with a faster and more accurate version. The impressive stability and instantaneous rendering of 3D images will enable users to save valuable programming time and effort.
Contact Details
Related Glossary Terms
- computer numerical control ( CNC)
computer numerical control ( CNC)
Microprocessor-based controller dedicated to a machine tool that permits the creation or modification of parts. Programmed numerical control activates the machine’s servos and spindle drives and controls the various machining operations. See DNC, direct numerical control; NC, numerical control.
- cylindrical grinding
cylindrical grinding
Grinding operation in which the workpiece is rotated around a fixed axis while the grinding wheel is fed into the outside surface in controlled relation to the axis of rotation. The workpiece is usually cylindrical, but it may be tapered or curvilinear in profile. See centerless grinding; grinding.
- grinding
grinding
Machining operation in which material is removed from the workpiece by a powered abrasive wheel, stone, belt, paste, sheet, compound, slurry, etc. Takes various forms: surface grinding (creates flat and/or squared surfaces); cylindrical grinding (for external cylindrical and tapered shapes, fillets, undercuts, etc.); centerless grinding; chamfering; thread and form grinding; tool and cutter grinding; offhand grinding; lapping and polishing (grinding with extremely fine grits to create ultrasmooth surfaces); honing; and disc grinding.
- grinding machine
grinding machine
Powers a grinding wheel or other abrasive tool for the purpose of removing metal and finishing workpieces to close tolerances. Provides smooth, square, parallel and accurate workpiece surfaces. When ultrasmooth surfaces and finishes on the order of microns are required, lapping and honing machines (precision grinders that run abrasives with extremely fine, uniform grits) are used. In its “finishing” role, the grinder is perhaps the most widely used machine tool. Various styles are available: bench and pedestal grinders for sharpening lathe bits and drills; surface grinders for producing square, parallel, smooth and accurate parts; cylindrical and centerless grinders; center-hole grinders; form grinders; facemill and endmill grinders; gear-cutting grinders; jig grinders; abrasive belt (backstand, swing-frame, belt-roll) grinders; tool and cutter grinders for sharpening and resharpening cutting tools; carbide grinders; hand-held die grinders; and abrasive cutoff saws.
- micron
micron
Measure of length that is equal to one-millionth of a meter.
- relief
relief
Space provided behind the cutting edges to prevent rubbing. Sometimes called primary relief. Secondary relief provides additional space behind primary relief. Relief on end teeth is axial relief; relief on side teeth is peripheral relief.
- shank
shank
Main body of a tool; the portion of a drill or similar end-held tool that fits into a collet, chuck or similar mounting device.
- steady rest
steady rest
Supports long, thin or flexible work being turned on a lathe. Mounts on the bed’s ways and, unlike a follower rest, remains at the point where mounted. See follower rest.
- total indicator runout ( TIR)
total indicator runout ( TIR)
Combined variations of all dimensions of a workpiece, measured with an indicator, determined by rotating the part 360°.
- tungsten carbide ( WC)
tungsten carbide ( WC)
Intermetallic compound consisting of equal parts, by atomic weight, of tungsten and carbon. Sometimes tungsten carbide is used in reference to the cemented tungsten carbide material with cobalt added and/or with titanium carbide or tantalum carbide added. Thus, the tungsten carbide may be used to refer to pure tungsten carbide as well as co-bonded tungsten carbide, which may or may not contain added titanium carbide and/or tantalum carbide.