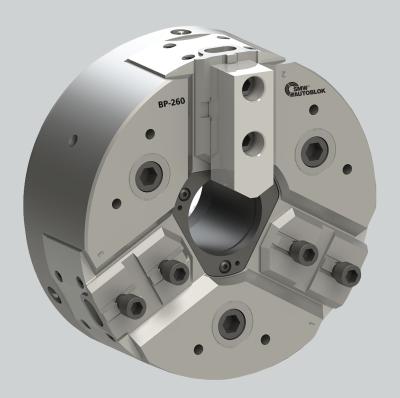
SMW Autoblok, a world leader in the design and manufacture of rotational chucks, stationary workholding, tooling and custom engineered solutions for the machine tool industry, presents the BP chuck, the only standard fully sealed power chuck on the market with large through hole for maximum lifespan, throughput and durability.
Ideal for CNC lathe applications, BP’s large through hole provides tremendous flexibility for virtually any application where a standard chuck is used including: O.D. and I.D. clamping, bar stock clamping and shaft clamping. Easily convert BP to a collet chuck using collet pads for small diameter parts.
A true workhorse, BP maintains high productivity even in harsh environments of dry machining, abrasive powders, high pressure or corrosive coolants, and more. Constant grease lubrication provides clamping force consistency and reduced wear, greatly reducing downtime and loss of productivity. With BP, daily maintenance intervals become a thing of the past and only require maintenance checks every 2,000 hours.
Being fully proofline® sealed from outside contaminants allows BP to maintain a consistent grip force for excellent repeatability at high speed, versus non-sealed chucks which can lose more than 50 percent grip force if not maintained properly. Other advantages include a case-hardened body and internal parts for high resistance and longer life.
Available in 210, 260, and 320 mm, BP series chucks accepts all industry top jaws. The BP-D utilizes master jaws with inch serration while the BP-M operates with metric serration (suitable for Japanese jaws). The American standard, tongue and groove master jaws, are available on the BP-C.
Contact Details
Related Glossary Terms
- abrasive
abrasive
Substance used for grinding, honing, lapping, superfinishing and polishing. Examples include garnet, emery, corundum, silicon carbide, cubic boron nitride and diamond in various grit sizes.
- chuck
chuck
Workholding device that affixes to a mill, lathe or drill-press spindle. It holds a tool or workpiece by one end, allowing it to be rotated. May also be fitted to the machine table to hold a workpiece. Two or more adjustable jaws actually hold the tool or part. May be actuated manually, pneumatically, hydraulically or electrically. See collet.
- collet
collet
Flexible-sided device that secures a tool or workpiece. Similar in function to a chuck, but can accommodate only a narrow size range. Typically provides greater gripping force and precision than a chuck. See chuck.
- computer numerical control ( CNC)
computer numerical control ( CNC)
Microprocessor-based controller dedicated to a machine tool that permits the creation or modification of parts. Programmed numerical control activates the machine’s servos and spindle drives and controls the various machining operations. See DNC, direct numerical control; NC, numerical control.
- lathe
lathe
Turning machine capable of sawing, milling, grinding, gear-cutting, drilling, reaming, boring, threading, facing, chamfering, grooving, knurling, spinning, parting, necking, taper-cutting, and cam- and eccentric-cutting, as well as step- and straight-turning. Comes in a variety of forms, ranging from manual to semiautomatic to fully automatic, with major types being engine lathes, turning and contouring lathes, turret lathes and numerical-control lathes. The engine lathe consists of a headstock and spindle, tailstock, bed, carriage (complete with apron) and cross slides. Features include gear- (speed) and feed-selector levers, toolpost, compound rest, lead screw and reversing lead screw, threading dial and rapid-traverse lever. Special lathe types include through-the-spindle, camshaft and crankshaft, brake drum and rotor, spinning and gun-barrel machines. Toolroom and bench lathes are used for precision work; the former for tool-and-die work and similar tasks, the latter for small workpieces (instruments, watches), normally without a power feed. Models are typically designated according to their “swing,” or the largest-diameter workpiece that can be rotated; bed length, or the distance between centers; and horsepower generated. See turning machine.