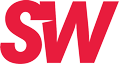
SW North America, a leading supplier of horizontal multi- and single-spindle CNC machining centers, automation, and complete system solutions, announced that parent company Schwäbische Werkzeugmaschinen GmbH (SW) is debuting two new products: the two-spindle BA W03-22 CNC machining center and the BA profile, a new machine concept for machining profiles at EMO 2023, the world's leading trade show for metalworking and production technology in Hanover, Germany.
Additionally, SW will be showcasing its largest machine for machining battery housings, the BA space3, and sharing insights into current trends in manufacturing such as friction stir welding and giga casting.
“Innovate Manufacturing is the theme of this year's EMO event, aligning perfectly with our corporate motto -- Smart Manufacturing Solutions. For us, innovative and smart manufacturing are two sides of the same coin,” says André Harter, Head of Marketing and Business Development, SW. “Both allow us to respond individually and efficiently to our customers' needs, and we are proud to debut two new smart manufacturing solutions that do just that.”
Up to 30% efficiency increases for the automotive industry
Productivity, flexibility, modularity, and connectivity are the most important factors for SW North America when it comes to meeting challenges with efficient system solutions in the fast-growing field of e-mobility, among others. The new BA W03-22 CNC machining center was created to achieve this.
With its high precision and efficiency, the two-spindle BA W03-22 CNC machining center is ideal for producing high-quality work products in medium and large series for the automotive industry. Compared to a single-spindle machine, cycle times can be reduced many times over, ensuring maximum productivity.
“We have expanded the proven machine concept of the model 3 series to include a two-spindle, double-station machine, allowing for faster axis accelerations with the linear motors installed in the machine,” explains Harter. “As a result, we achieve much more power and speed compared to a ball screw as in the BA 322 model, for instance, with 20 percent faster chip-to-chip times.”
With 300 mm of travel, The BA W03-22 CNC machining center also positions in G0 30 percent faster than the BA 322, and it is the first from SW to be equipped with Siemens Sinumerik One control.
Electric vehicle machining with BA profile and BA space3
Another highlight in Hannover is the new BA profile machine concept for machining profiles.
“The BA profile machine concept can easily mill profiles of various materials up to a length of 2,500 mm, for applications in the truck and automotive industries, amongst others,” explains Harter. “Featuring a compact design, the two-spindle machine has two operating areas and allows machining on two worktables per side. It can be loaded either via automation or ergonomically by hand.”
Also on display will be SW’s BA space3, the largest machine in the company's portfolio to date, suited for machining large battery housings and numerous structural components needed for the growing e-vehicle market, as well as aerospace and agriculture.
In giga casting, instead of a multitude of individual parts welded or bolted together, only a few large components are used, each of which is cast and finished from a single piece. Underbodies, subframes, or entire front frames for the construction of electric vehicles can be created in this way.
At the booth, visitors will witness how a robot loads and unloads the BA space3.
Manufacturing trends at the booth in hall 12
Beyond this, SW executives will present additional technologies for machining aluminum, steel, cast iron, cast steel, and light metals at EMO 2023.
“During the show, we not only want to present our extensive portfolio, but also engage customers, experts, and professionals on trending industry topics such as sustainability, friction stir welding and giga casting,” says Harter. “Thanks to friction stir welding, we are bringing more sustainability to manufacturing by working at lower temperatures, without shielding gas. This significantly reduces both energy consumption and emissions.”
Harter adds, “We want to surprise visitors at EMO 2023 with the diversity of our manufacturing solutions. With its flexible manufacturing modules, digital networking of the process chain, and intelligent automation solutions – developed jointly with customers – SW delivers customized manufacturing solutions that are precisely tailored to their individual needs.”
See these new machines and manufacturing solutions from Schwäbische Werkzeugmaschinen GmbH (SW) in person at EMO 2023 in Hannover, Germany. The company will be located in Hall 12 at Booth C04 from September 18-23, 2023.
Contact Details
Related Glossary Terms
- centers
centers
Cone-shaped pins that support a workpiece by one or two ends during machining. The centers fit into holes drilled in the workpiece ends. Centers that turn with the workpiece are called “live” centers; those that do not are called “dead” centers.
- computer numerical control ( CNC)
computer numerical control ( CNC)
Microprocessor-based controller dedicated to a machine tool that permits the creation or modification of parts. Programmed numerical control activates the machine’s servos and spindle drives and controls the various machining operations. See DNC, direct numerical control; NC, numerical control.
- machining center
machining center
CNC machine tool capable of drilling, reaming, tapping, milling and boring. Normally comes with an automatic toolchanger. See automatic toolchanger.
- metalworking
metalworking
Any manufacturing process in which metal is processed or machined such that the workpiece is given a new shape. Broadly defined, the term includes processes such as design and layout, heat-treating, material handling and inspection.
- milling machine ( mill)
milling machine ( mill)
Runs endmills and arbor-mounted milling cutters. Features include a head with a spindle that drives the cutters; a column, knee and table that provide motion in the three Cartesian axes; and a base that supports the components and houses the cutting-fluid pump and reservoir. The work is mounted on the table and fed into the rotating cutter or endmill to accomplish the milling steps; vertical milling machines also feed endmills into the work by means of a spindle-mounted quill. Models range from small manual machines to big bed-type and duplex mills. All take one of three basic forms: vertical, horizontal or convertible horizontal/vertical. Vertical machines may be knee-type (the table is mounted on a knee that can be elevated) or bed-type (the table is securely supported and only moves horizontally). In general, horizontal machines are bigger and more powerful, while vertical machines are lighter but more versatile and easier to set up and operate.