Noncontact 3D laser scanning is a well-established technology for measuring and inspecting machined parts, which is proving beneficial for producers of laser scanning systems. Although the technology existed before he began selling laser scanners nearly two decades ago, Matthew Gibbons, sales applications engineer manager for Nikon Metrology Inc. in Brighton, Michigan, said prospective customers early in his career needed to be sought and educated about what laser scanning could do for them. Since then, parts manufacturers have come to realize the benefits of laser scanning and are seeking it out.
“It’s giving them a lot more information than they were ever able to capture before, maybe giving them more than they would even like,” he said. “At one point, they were only focusing on what they thought were the critical features or areas, and now it’s giving them a much more complete picture of what it is that they’re working with.”
Accuracy always will be better with a touch probe than a laser scanner due to physics, noted Brian Winters, North America product manager for Absolute Arms at Hexagon’s Manufacturing Intelligence division, but tactile probing typically doesn’t capture the whole picture.
“For example,” he said, “if you are trying to measure the surface profile on a complex-shaped part, the best way to obtain complete data is with scanning.”
Scanning generates a point cloud, which is gathered when laser light is projected onto a surface and a camera captures the reflection of that image, Gibbons explained.
“We’re turning that image into a series of points,” he said. “Depending on the scanning, we can collect upward of 450,000 points per second.”

Hexagon’s AS1 scanner, however, features a blue laser line and range finder that operate up to a 300-hertz scan rate for gathering 1.2 million points per second, Winters noted. Sometimes the amount of data collected with a laser scanner seems overwhelming.
“What we are seeing (is) that customers are turning the settings down in less critical areas to keep the point cloud at a more manageable size for processing,” he said.
The most accurate laser scanner that Nikon Metrology offers is down to 10 µm (0.0004"), Gibbons said, which provides a high level of detail and resolution and is suitable for measuring and inspecting small parts. While a probe can be more accurate when measuring individual points, a laser scanner fully characterizes the part features being examined.
Scanner Types
Gibbons said Nikon Metrology offers scanners that fall into two categories: ones that provide automated CNC scanning on a coordinate measuring machine and one that is mounted on an articulated arm for manual scanning. The former includes the L100, LC15Dx and XC65Dx laser scanners, and the latter is the ModelMaker H120, which is mounted on the MCAx S articulated arm.
“There are a lot of speed improvements that can come to a CMM program by adding scanning, because now we don’t have to stop at each one of those features and take a handful of points,” he said. “We can continuously move over it.”
Hexagon offers multiple options to fit a customer’s application, including the RS5, RS-Squared Area Scanner and AS1 modular scanners, Winters said, adding that the AS1 is the most popular. The default scanning mode for the AS1 is SHINE, which stands for systematic high intelligence noise elimination. He said it dynamically evaluates the optimal exposure on each individual point to get the highest-quality data possible without any user intervention. It is a type of HDR, or high data rate+, technology that allows surface types to be scanned accurately without a reduction of the frame rate or laser line width.
“It ensures full scanner performance all the time,” he said. “We also have some external scanners that can be integrated for the seven-axis arm, such as the HP-L-20.8, and for the six-axis arm with the HP-L-8.9.”
The HP-L-8.9 laser scanner, for instance, is compatible with all six-axis Absolute Arm portable CMMs and can switch from laser scanning to tactile probing without any kind of calibration, the company reports.
Winters noted that Absolute Arm portable CMMs are sealed to protect them from the dust, debris and fluids commonly found at machine shops, and they offer a wide operating temperature range of 5 to 45 degrees Celsius (41 to 113 degrees Fahrenheit). This is the only portable arm that offers that level of ingress protection, according to the company.
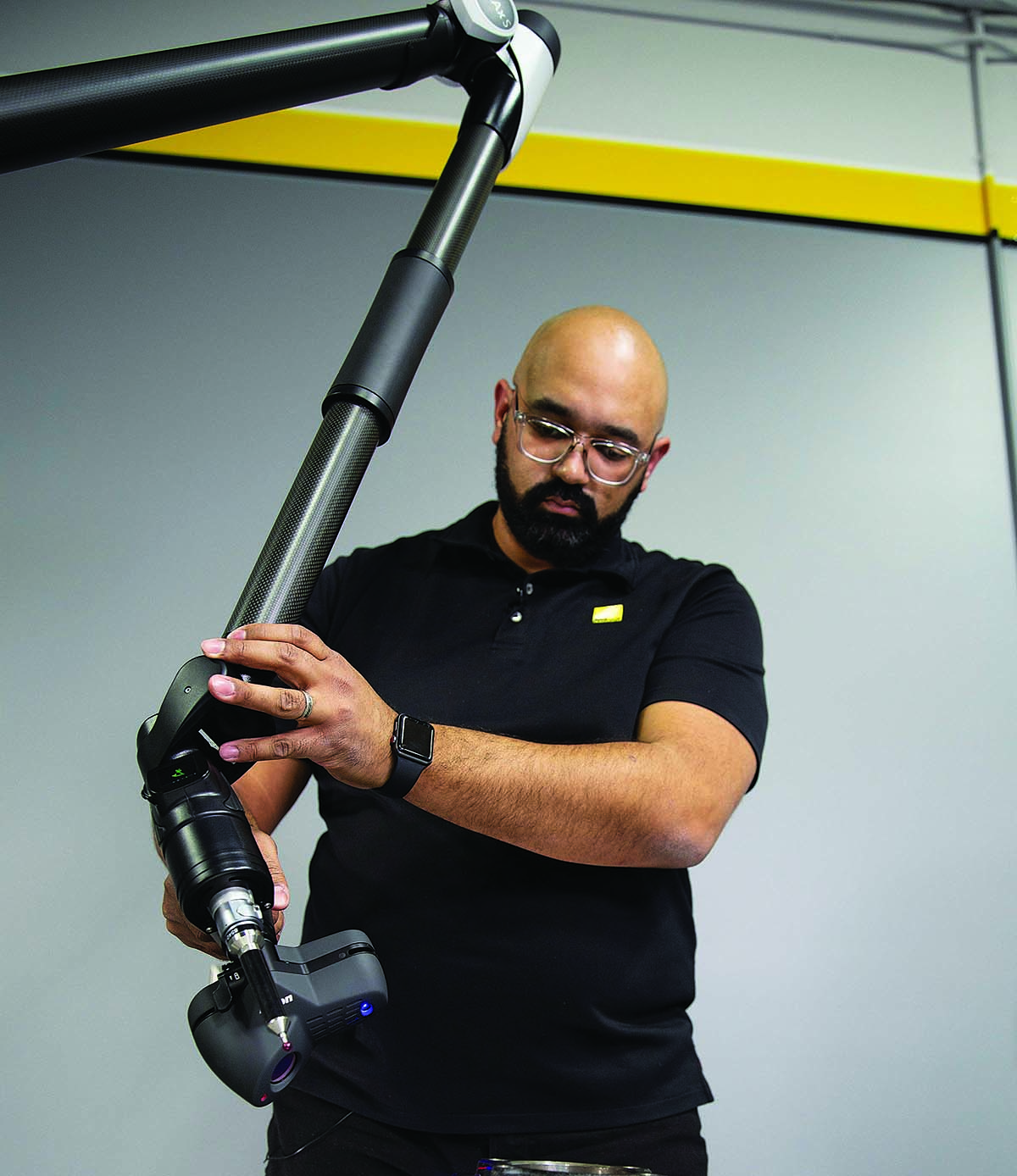
“We offer a completely wireless version that allows you to park the arm on a machine and leave it there for in-process inspection checks,” he said. “This version eliminates any cables or hazards on the floor, and with additional hot-swap batteries you can work indefinitely in this mode.”
All these scanners are options within Hexagon’s Absolute Arm line, Winters said, noting that the company is phasing down production of the HP-L-20.8 because of the increased demand for the AS1.
“We support all our products for a minimum of 10 years,” he said. “We also offer trade-in toward a new scanner so current Hexagon customers can always have access to the latest and greatest technology.”
Laser scanning is well suited to inspecting complex, contoured surfaces, whereas a touch probe is effective at measuring a handful of features, such as a narrow opening that is too deep for a laser to see inside, Gibbons said.
“That’s where a longer stylus on a probe can get down to something because you don’t actually have to see it,” he said.
As noted previously, tactile probing or laser scanning on a CMM is not an either/or situation.
“We have many customers that still use touch probing, along with their laser scanners,” Gibbons said. “We can use the laser scanner just as another tool in the toolbox.”
Material Issues
Some end users understandably are concerned about using a laser scanner on a part made of a material, for example, with a highly reflective surface.
“One play on tactile is that it doesn’t care about the surface itself,” Winters said, referencing parts with surfaces that are reflective, shiny or black. “With the latest capabilities from laser technology, one can deliver complete 3D scan data from many surfaces, including highly reflective and nearly transparent ones.”
A reflective or dark surface can be more challenging for a laser scanner, but Gibbons said the latest scanners perform effectively on those types of surfaces compared with some previous generations of equipment. Nikon Metrology’s interface software for scanners has reflection filtering and can account for “noise” generated during the process.
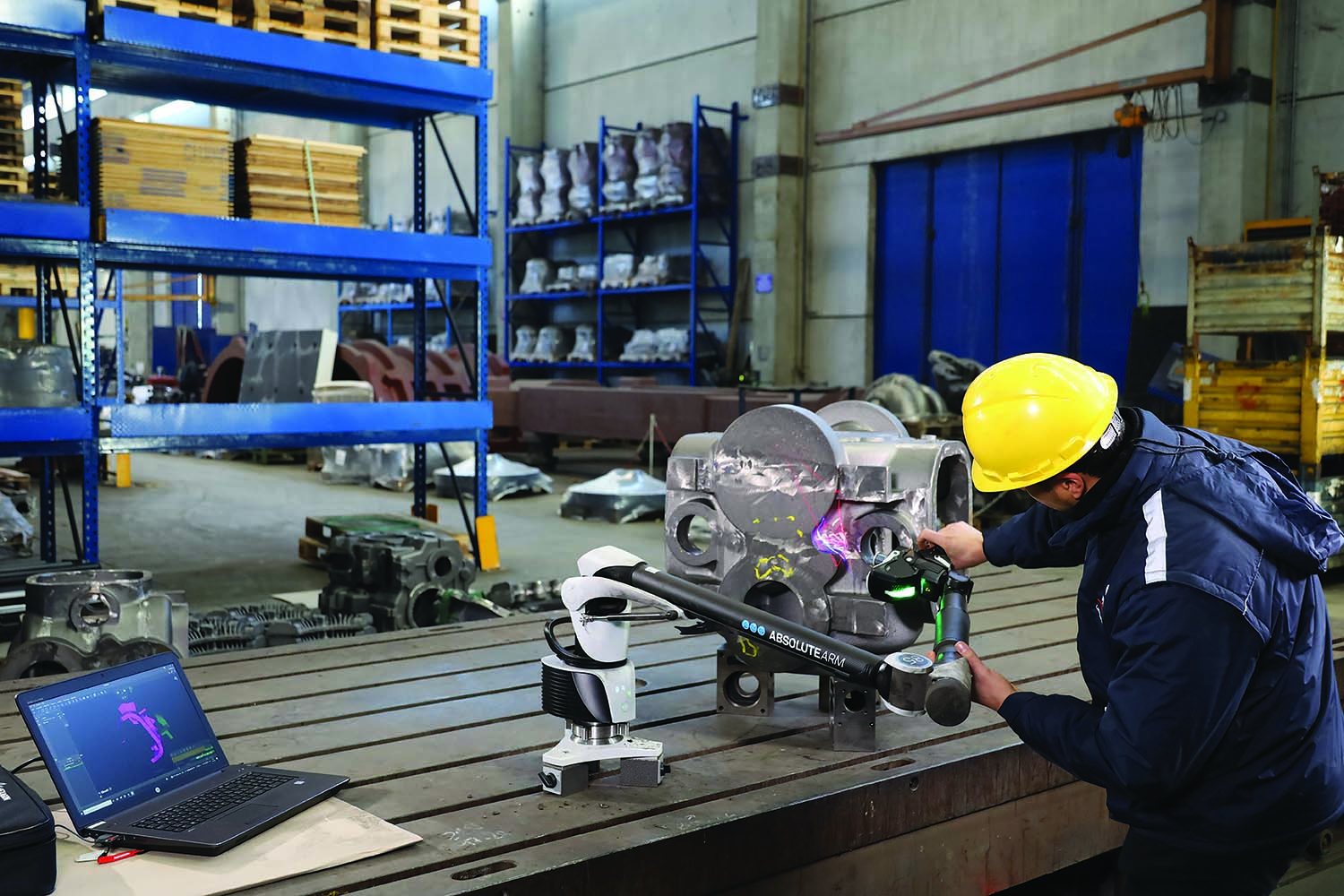
“Our ESP4 technology gives us the ability to adjust laser intensity of each point on the laser stripe,” he said. “We can account for changes in reflectivity, color or texture of the part in real time.”
In addition, Gibbons said scanning techniques can be implemented to reduce any reflection that might impact the image, such as changing the laser angle.
“Overall,” he said, “our scanners handle challenging surface conditions pretty well.”
Limitations exist with the line of sight in the triangulation of the laser, Winters noted, but they can be overcome.
“Many times,” he said, “we see that (for) critical areas where there’s a need to identify micron-level precision, a touch probe can be used in concert with the scanner.”
And advancements continue to be made to laser scanners. For example, Hexagon’s updated algorithm for the AS1 scanner provides better utilization of the data to improve performance when scanning stamped and sheet metal parts, increased accuracy on holes and slots, and spring-up reduction on tangent colors, Winters said.
Digital Threads
As more manufacturers begin and continue Industry 4.0 initiatives, Winters noted that Hexagon’s scanning technology is helping to capture information from the physical realm and create a digital twin.
“We aren’t just capturing at a level to simulate the environment,” he said. “Our scanners are working at a level that allows for the digital analysis to happen at the same time.”
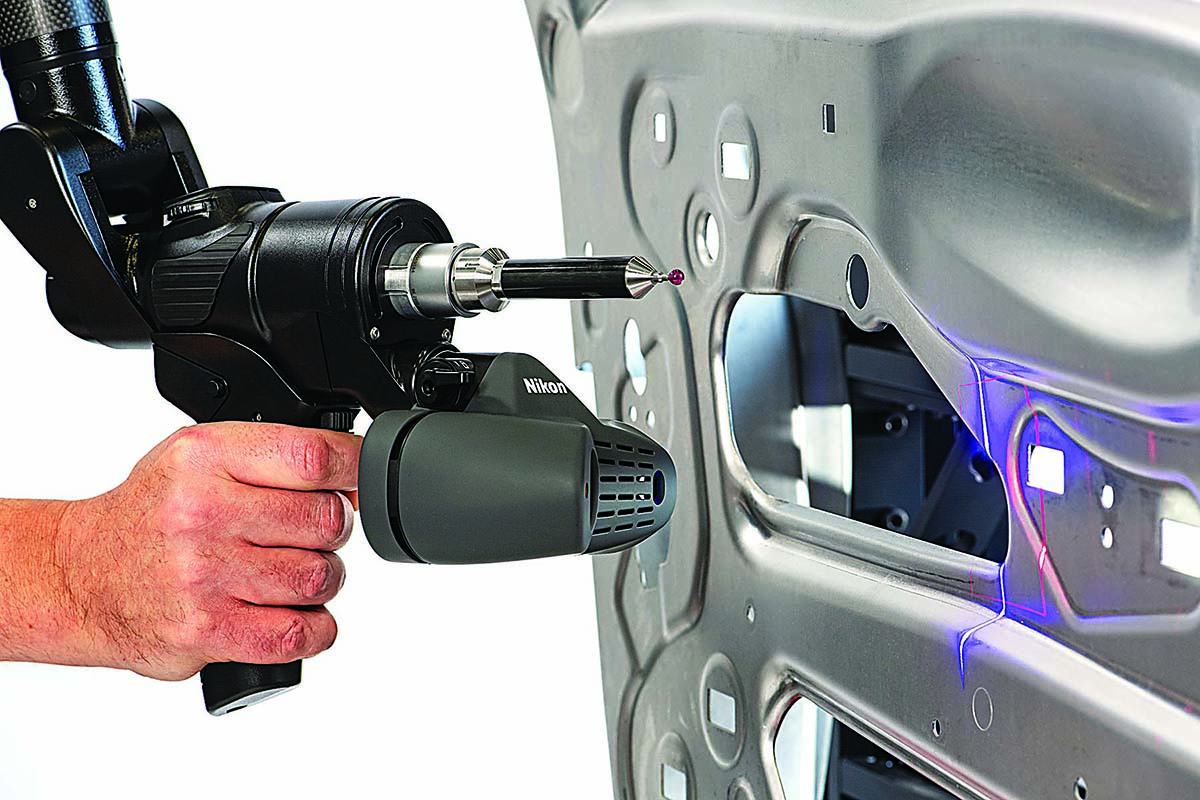
Besides boosting productivity, Winters added that laser scanning can mitigate risk by reducing inspection times and increasing resolution in the point cloud to create a level “previously unknown” for access to organized and intelligent data and identify nonconforming part origins in the supply chain.
He noted that although the Absolute Arm is often the entry point into the Hexagon ecosystem, once end users see the company’s suite of offerings, Hexagon can work with customers to find a bespoke solution and grow with them in the future.
“We have just launched our Nexus platform, which allows for open collaboration across all our offerings,” Winters said. “We might already have the solution to a problem you were unaware you even had.”
As more parts manufacturers integrate noncontact 3D laser scanning into their inspection and measurement activities, they are obtaining beneficial information that they previously didn’t have, Gibbons said. Prior to machining a casting, for instance, a laser scanner can determine whether the setup is sufficient so the needed amount of material can be removed.
“The laser scanner gives you insight before additional time or effort is put into a part,” he said. “It helps prevent a situation where material is going to be scrapped.”
For more information about the Absolute Arm portable measuring arm from Hexagon and the L100 scanner from Nikon Metrology, view video presentations at https://qr.ctemag.com/1j232 and https://qr.ctemag.com/1j233
Contact Details
Contact Details
Related Glossary Terms
- calibration
calibration
Checking measuring instruments and devices against a master set to ensure that, over time, they have remained dimensionally stable and nominally accurate.
- computer numerical control ( CNC)
computer numerical control ( CNC)
Microprocessor-based controller dedicated to a machine tool that permits the creation or modification of parts. Programmed numerical control activates the machine’s servos and spindle drives and controls the various machining operations. See DNC, direct numerical control; NC, numerical control.
- in-process gaging ( in-process inspection)
in-process gaging ( in-process inspection)
Quality-control approach that monitors work in progress, rather than inspecting parts after the run has been completed. May be done manually on a spot-check basis but often involves automatic sensors that provide 100 percent inspection.
- metrology
metrology
Science of measurement; the principles on which precision machining, quality control and inspection are based. See precision machining, measurement.
- turning
turning
Workpiece is held in a chuck, mounted on a face plate or secured between centers and rotated while a cutting tool, normally a single-point tool, is fed into it along its periphery or across its end or face. Takes the form of straight turning (cutting along the periphery of the workpiece); taper turning (creating a taper); step turning (turning different-size diameters on the same work); chamfering (beveling an edge or shoulder); facing (cutting on an end); turning threads (usually external but can be internal); roughing (high-volume metal removal); and finishing (final light cuts). Performed on lathes, turning centers, chucking machines, automatic screw machines and similar machines.
Contributors
Hexagon’s Manufacturing Intelligence division
www.hexagonmi.com
Nikon Metrology Inc.
810-220-4360
www.industry.nikon.com