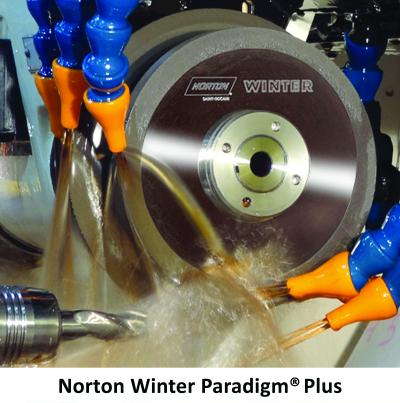
Saint-Gobain Abrasives, one of the world’s largest abrasives manufacturers, announced the introduction of Norton Winter Paradigm® Plus Diamond Grinding Wheels featuring a new premium grain technology complementing the established proprietary, patented brittle-metal bond, resulting in a significant upgrade in performance on carbide round tools for fluting and gashing applications, and periphery grinding on carbide and cermet inserts grinding. Paradigm Plus wheels are the next generation of the popular Paradigm wheels and are in the Norton “Best Tier” of products. New grain technology, together with a new advanced lightweight core, produces lower specific cutting energy with a 25% to 50% higher material removal rate (MRR), and provides significantly improved wheel life when compared with current Paradigm wheels.
The new resin-based core, available for round tool grinding, is over 75% lighter and eliminates the risk of sparks while reducing chipping, breakage and chatter, for better finishing in round tool applications. The Paradigm bond, which combines the wear resistance of a metal bonded wheel with the ease of profiling in a vitrified bonded wheel, has up to 46% porosity enabling improved coolant flow for cooler cutting and reduced part burning, allowing for truing and dressing.
“We are pleased to offer our customers new Paradigm Plus wheels, which produce more parts per wheel, reducing total process costs and cycle times, while delivering better quality part edges and finishes,” said Philip Varghese, Sr. Product Manager for Resin Bond Products, Superabrasives,
Norton | Saint-Gobain Abrasives. “The new lighter core also allows for safer and easier handling,” added Varghese.
Norton Winter Paradigm Plus grinding wheels are made to order.
Norton Winter G-Force™ Plus Next Generation Diamond Wheels
Offered in the Norton “Better Tier” primarily for grinding round tools in fluting and gashing applications, new Norton Winter G-Force™ Plus Next Generation Diamond Wheels feature new premium grain technology with lower normal forces and higher performance, which is complemented by an improved hybrid bond technology providing significant improvement ranging from a 25% to 50% increased MRR, and longer wheel life when compared with current G-Force wheels. New G-Force Plus Wheels offer higher feed rates and reduced cycle times, resulting in more parts per dress and reduced process costs. Improved edge holding, better part quality and surface finish are all key benefits of the new wheels. G-Force Plus Wheels provide cooler cutting when grinding a range of heat- and wear-resistant materials.
Contact Details
Related Glossary Terms
- burning
burning
Rotary tool that removes hard or soft materials similar to a rotary file. A bur’s teeth, or flutes, have a negative rake.
- chatter
chatter
Condition of vibration involving the machine, workpiece and cutting tool. Once this condition arises, it is often self-sustaining until the problem is corrected. Chatter can be identified when lines or grooves appear at regular intervals in the workpiece. These lines or grooves are caused by the teeth of the cutter as they vibrate in and out of the workpiece and their spacing depends on the frequency of vibration.
- coolant
coolant
Fluid that reduces temperature buildup at the tool/workpiece interface during machining. Normally takes the form of a liquid such as soluble or chemical mixtures (semisynthetic, synthetic) but can be pressurized air or other gas. Because of water’s ability to absorb great quantities of heat, it is widely used as a coolant and vehicle for various cutting compounds, with the water-to-compound ratio varying with the machining task. See cutting fluid; semisynthetic cutting fluid; soluble-oil cutting fluid; synthetic cutting fluid.
- dressing
dressing
Removal of undesirable materials from “loaded” grinding wheels using a single- or multi-point diamond or other tool. The process also exposes unused, sharp abrasive points. See loading; truing.
- feed
feed
Rate of change of position of the tool as a whole, relative to the workpiece while cutting.
- fluting
fluting
Cutting straight or spiral grooves in drills, endmills, reamers and taps to improve cutting action and remove chips.
- grinding
grinding
Machining operation in which material is removed from the workpiece by a powered abrasive wheel, stone, belt, paste, sheet, compound, slurry, etc. Takes various forms: surface grinding (creates flat and/or squared surfaces); cylindrical grinding (for external cylindrical and tapered shapes, fillets, undercuts, etc.); centerless grinding; chamfering; thread and form grinding; tool and cutter grinding; offhand grinding; lapping and polishing (grinding with extremely fine grits to create ultrasmooth surfaces); honing; and disc grinding.
- profiling
profiling
Machining vertical edges of workpieces having irregular contours; normally performed with an endmill in a vertical spindle on a milling machine or with a profiler, following a pattern. See mill, milling machine.
- truing
truing
Using a diamond or other dressing tool to ensure that a grinding wheel is round and concentric and will not vibrate at required speeds. Weights also are used to balance the wheel. Also performed to impart a contour to the wheel’s face. See dressing.
- wear resistance
wear resistance
Ability of the tool to withstand stresses that cause it to wear during cutting; an attribute linked to alloy composition, base material, thermal conditions, type of tooling and operation and other variables.