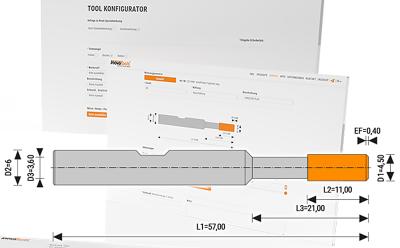
Semi-standard and special tools customized in line with the machining application provide that crucial edge in manufacturing. Coordination between the cutter and tool manufacturer was always a time-consuming business until it then became possible to fix custom-fit tool solutions on the customer machine. The new online tool configurator, which was developed by Inovatools – a tool manufacturer based in Haunstetten, near Kinding in Germany – and can be found at www.inovatools.eu, significantly accelerates the entire process from the initial order through to design and shipment and takes special tool production to a whole new level of efficiency.
Whether drilling, milling or grinding, application-optimized semi-standard and special tools from Inovatools make many machining operations much more productive and efficient than with conventional tools. Tools that exceed standard requirements always constitute a particular challenge. But thanks to the new digital tool configurator service, Inovatools now offers an online application that allows users to quickly and easily identify semi-standard tools from the catalog program on the basis of predefined Inovatools standards and conveniently configure customized special tools based on their individual needs, materials and processes.
Norbert Geyer, Head of Customer Services at Inovatools: “Using our tool configurator, customers can quickly and easily configure and order precisely the tool they need. This saves time and increases efficiency. Whether semi-standard or special tools, the interface for entering all the relevant parameters is extremely easy to use. We ask about all sorts of tool properties and adapt these in line with the machining requirements. In this way, customers can configure in just a few clicks exactly the tool they need for their application.” In addition to entering the required parameters, customers can also upload technical drawings, sketches, photos and so on via the service tool.
The benefits of this online system couldn’t be clearer: The tool configurator automates the entire request and ordering process and radically reduces the need for person-to-person coordination by e-mail or telephone. So in e-mail correspondence, for example, that constant back and forth asking for and supplying additional information so that requests can be processed is a thing of the past, now that an automated tool has been developed that is capable of processing these requests much more quickly and efficiently.
This means that the Inovatools tool configurator saves a lot of time not only during the whole request and ordering process but also in downstream processes too. For example, customers receive a quick response – usually within 24 hours – from Inovatools complete with a detailed offer specially tailored to their specific requirements.
Norbert Geyer: “Using the tool configurator, customers can create a tailor-made, applicationspecific tool solution in just a few clicks of the mouse. In addition to the tool configurator, Inovatools offers personal consultations with specialists who help you to define the optimal specifications. Our tool specialists look at your specific machining requirements, and you receive the perfect tool manufactured to the very highest quality. We get to work as soon as your order is confirmed and deliver your desired product at record speed – usually within just a few working days. This takes special tool production to a whole new level of efficiency and ensures optimal planning certainty for our customers.”
Contact Details
Related Glossary Terms
- gang cutting ( milling)
gang cutting ( milling)
Machining with several cutters mounted on a single arbor, generally for simultaneous cutting.
- grinding
grinding
Machining operation in which material is removed from the workpiece by a powered abrasive wheel, stone, belt, paste, sheet, compound, slurry, etc. Takes various forms: surface grinding (creates flat and/or squared surfaces); cylindrical grinding (for external cylindrical and tapered shapes, fillets, undercuts, etc.); centerless grinding; chamfering; thread and form grinding; tool and cutter grinding; offhand grinding; lapping and polishing (grinding with extremely fine grits to create ultrasmooth surfaces); honing; and disc grinding.
- milling
milling
Machining operation in which metal or other material is removed by applying power to a rotating cutter. In vertical milling, the cutting tool is mounted vertically on the spindle. In horizontal milling, the cutting tool is mounted horizontally, either directly on the spindle or on an arbor. Horizontal milling is further broken down into conventional milling, where the cutter rotates opposite the direction of feed, or “up” into the workpiece; and climb milling, where the cutter rotates in the direction of feed, or “down” into the workpiece. Milling operations include plane or surface milling, endmilling, facemilling, angle milling, form milling and profiling.