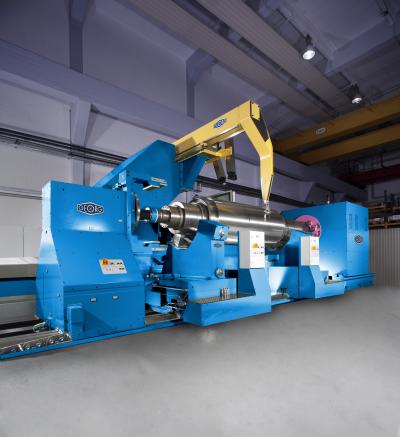
GEORG introduces its new ultragrind roll grinding machine for aluminum rolling mills. The innovative feature of this machine is the CBN technology. The machine achieves grinding times up to 50 percent shorter than those needed with conventional grinders, while achieving a superior surface quality and longer roll life times.
So far, cubic boron nitride (CBN) cutting tools have only been used for grinding rolls used in steel rolling mills. For Salzgitter Flachstahl AG, GEORG manufactured the world’s first CBN roll grinder in use in a roll shop of a hot rolling mill - where it has proved highly successful.
GEORG is now also introducing this technology to the aluminum industry:
The combination of CBN grinding, measuring during the grinding process and the use of a Siemens 840 D sl grinding control system adapted to the CBN technology achieves grinding times up to 50 percent shorter than other grinders used so far.
In 2019, GEORG is going to deliver the first CBN grinding machine to be used in the aluminum sector: GEORG is manufacturing an ultragrind 50 for the roll shop of the new ELVAL rolling mill near Athens in Greece. The machine will grind back-up and work rolls weighing up to 63 tons, with diameters of up to 1,600 mm and widths of up to 6,500 mm automatically.
Dr. Wieland H. Klein, head of GEORG’s machine tools division, explains where he sees the overall economic benefit for the customer: ”Our new machines come with ultrasonic, eddy current and surface wave systems for integrated crack inspection. This ensures that the rolls are not ground any deeper than absolutely necessary. The advantage for the customer are shorter machining times, longer roll live times and, last but not least, cost savings.”
The machine for ELVAL will be part of the plant-wide process network, as all measurement data acquired during the grinding process will be recorded and transferred to the host computers.
Contact Details
Related Glossary Terms
- cubic boron nitride ( CBN)
cubic boron nitride ( CBN)
Crystal manufactured from boron nitride under high pressure and temperature. Used to cut hard-to-machine ferrous and nickel-base materials up to 70 HRC. Second hardest material after diamond. See superabrasive tools.
- cubic boron nitride ( CBN)2
cubic boron nitride ( CBN)
Crystal manufactured from boron nitride under high pressure and temperature. Used to cut hard-to-machine ferrous and nickel-base materials up to 70 HRC. Second hardest material after diamond. See superabrasive tools.
- grinding
grinding
Machining operation in which material is removed from the workpiece by a powered abrasive wheel, stone, belt, paste, sheet, compound, slurry, etc. Takes various forms: surface grinding (creates flat and/or squared surfaces); cylindrical grinding (for external cylindrical and tapered shapes, fillets, undercuts, etc.); centerless grinding; chamfering; thread and form grinding; tool and cutter grinding; offhand grinding; lapping and polishing (grinding with extremely fine grits to create ultrasmooth surfaces); honing; and disc grinding.
- grinding machine
grinding machine
Powers a grinding wheel or other abrasive tool for the purpose of removing metal and finishing workpieces to close tolerances. Provides smooth, square, parallel and accurate workpiece surfaces. When ultrasmooth surfaces and finishes on the order of microns are required, lapping and honing machines (precision grinders that run abrasives with extremely fine, uniform grits) are used. In its “finishing” role, the grinder is perhaps the most widely used machine tool. Various styles are available: bench and pedestal grinders for sharpening lathe bits and drills; surface grinders for producing square, parallel, smooth and accurate parts; cylindrical and centerless grinders; center-hole grinders; form grinders; facemill and endmill grinders; gear-cutting grinders; jig grinders; abrasive belt (backstand, swing-frame, belt-roll) grinders; tool and cutter grinders for sharpening and resharpening cutting tools; carbide grinders; hand-held die grinders; and abrasive cutoff saws.
- milling machine ( mill)
milling machine ( mill)
Runs endmills and arbor-mounted milling cutters. Features include a head with a spindle that drives the cutters; a column, knee and table that provide motion in the three Cartesian axes; and a base that supports the components and houses the cutting-fluid pump and reservoir. The work is mounted on the table and fed into the rotating cutter or endmill to accomplish the milling steps; vertical milling machines also feed endmills into the work by means of a spindle-mounted quill. Models range from small manual machines to big bed-type and duplex mills. All take one of three basic forms: vertical, horizontal or convertible horizontal/vertical. Vertical machines may be knee-type (the table is mounted on a knee that can be elevated) or bed-type (the table is securely supported and only moves horizontally). In general, horizontal machines are bigger and more powerful, while vertical machines are lighter but more versatile and easier to set up and operate.