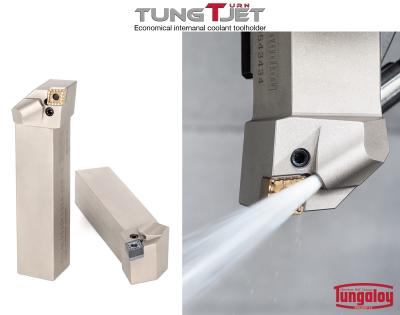
Tungaloy has expanded its TungTurn-Jet high-pressure through-coolant turning toolholders by adding toolholders with new streamlined coolant outlet design.
Tungaloy’s precision through-coolant turning toolholder series, TungTurn-Jet is capable of using high-pressure coolant of over 7 MPa, or 1,015 Psi, to effectively control chips in long-chipping materials such as stainless steel and heat-resistant superalloys.
The new toolholders feature a coolant outlet built in the body. This streamlined design is more effective than conventional through-coolant toolholders that have an adjustable coolant nozzle or bulky nozzle assembly. With reduced number of parts, the new toolholders expand the TungTurn-Jet range with an economical option that can contribute to customers seeking further tool cost reductions, while maintaining effective chip control and maximum tool life.
Furthermore, when used with ISO-EcoTurn downsized insert, the new TungTurn-Jet toolholders improves productivity and economy when machining steel and exotic materials.
The TungTurn-Jet series
Developed for productive OD turning, grooving, thread turning, and ID turning (the ID turning holders are only available in PSC machine-side connection), the series enables high speed machining with effective chip evacuation.
TungTurn-Jet toolholder systems for Swiss machine applications are available as well. Small and miniature parts machining processes can dramatically be improved with TungTurn-Jet toolholders and its through-coolant method. Also, the series can eliminate the hassle of coolant hose connections when used in a Swiss machine that is equipped with the capability of supplying coolant directly into the toolholder from the gang slide. This plug-and-play coolant capability allows operators to simply mount the toolholders on the gang slide or tool post and use the integrated coolant nozzle for effective chip control and maximum tool life.
Contact Details
Related Glossary Terms
- coolant
coolant
Fluid that reduces temperature buildup at the tool/workpiece interface during machining. Normally takes the form of a liquid such as soluble or chemical mixtures (semisynthetic, synthetic) but can be pressurized air or other gas. Because of water’s ability to absorb great quantities of heat, it is widely used as a coolant and vehicle for various cutting compounds, with the water-to-compound ratio varying with the machining task. See cutting fluid; semisynthetic cutting fluid; soluble-oil cutting fluid; synthetic cutting fluid.
- grooving
grooving
Machining grooves and shallow channels. Example: grooving ball-bearing raceways. Typically performed by tools that are capable of light cuts at high feed rates. Imparts high-quality finish.
- inner diameter ( ID)
inner diameter ( ID)
Dimension that defines the inside diameter of a cavity or hole. See OD, outer diameter.
- outer diameter ( OD)
outer diameter ( OD)
Dimension that defines the exterior diameter of a cylindrical or round part. See ID, inner diameter.
- superalloys
superalloys
Tough, difficult-to-machine alloys; includes Hastelloy, Inconel and Monel. Many are nickel-base metals.
- toolholder
toolholder
Secures a cutting tool during a machining operation. Basic types include block, cartridge, chuck, collet, fixed, modular, quick-change and rotating.
- turning
turning
Workpiece is held in a chuck, mounted on a face plate or secured between centers and rotated while a cutting tool, normally a single-point tool, is fed into it along its periphery or across its end or face. Takes the form of straight turning (cutting along the periphery of the workpiece); taper turning (creating a taper); step turning (turning different-size diameters on the same work); chamfering (beveling an edge or shoulder); facing (cutting on an end); turning threads (usually external but can be internal); roughing (high-volume metal removal); and finishing (final light cuts). Performed on lathes, turning centers, chucking machines, automatic screw machines and similar machines.