Turning can generate a significant amount of dust, smoke and fumes, which affect air quality if not properly controlled. Like grinding, turning produces a mix of coarse particulate and fine particulate or fumed material. There may also be oil mists from metalworking fluids. Specific health risks vary depending on the types of materials turned and the size of the particulate produced by the turning process.
Common health impacts include:
- Respiratory irritation. Dust, fumes and aerosols generated during turning can irritate the eyes, nose, throat and lungs, causing symptoms like coughing, sneezing, shortness of breath or asthma.
- Allergic reactions. Some people may be allergic to certain types of dust, especially from plastics and specific metals, and might experience allergic reactions, such as skin rashes and hives.
- Cancer. Long-term exposure to particular types of dust and fumes can cause cancer of the lungs and other body systems.
- Metal fume fever. Inhaling metal dust and fumes can cause a flu-like illness with symptoms like fevers, chills, headaches and muscle aches.
- Neurological damage. Exposure to dust and fumes from certain metal alloys, such as stainless steel, is associated with neurological symptoms like headaches, dizziness, fatigue, memory problems and tremors similar to Parkinson’s disease.
- Unpleasant odors. Odors can be generated during turning processes, creating an unpleasant work environment. This may make it more difficult to attract and keep good team members.
- Slip and fall hazards. Mists from coolants and lubricants used in turning end up on the shop floor if they are not captured, creating a hazardous work area.
Proper ventilation and dust collection are essential to mitigate air quality issues associated with turning.
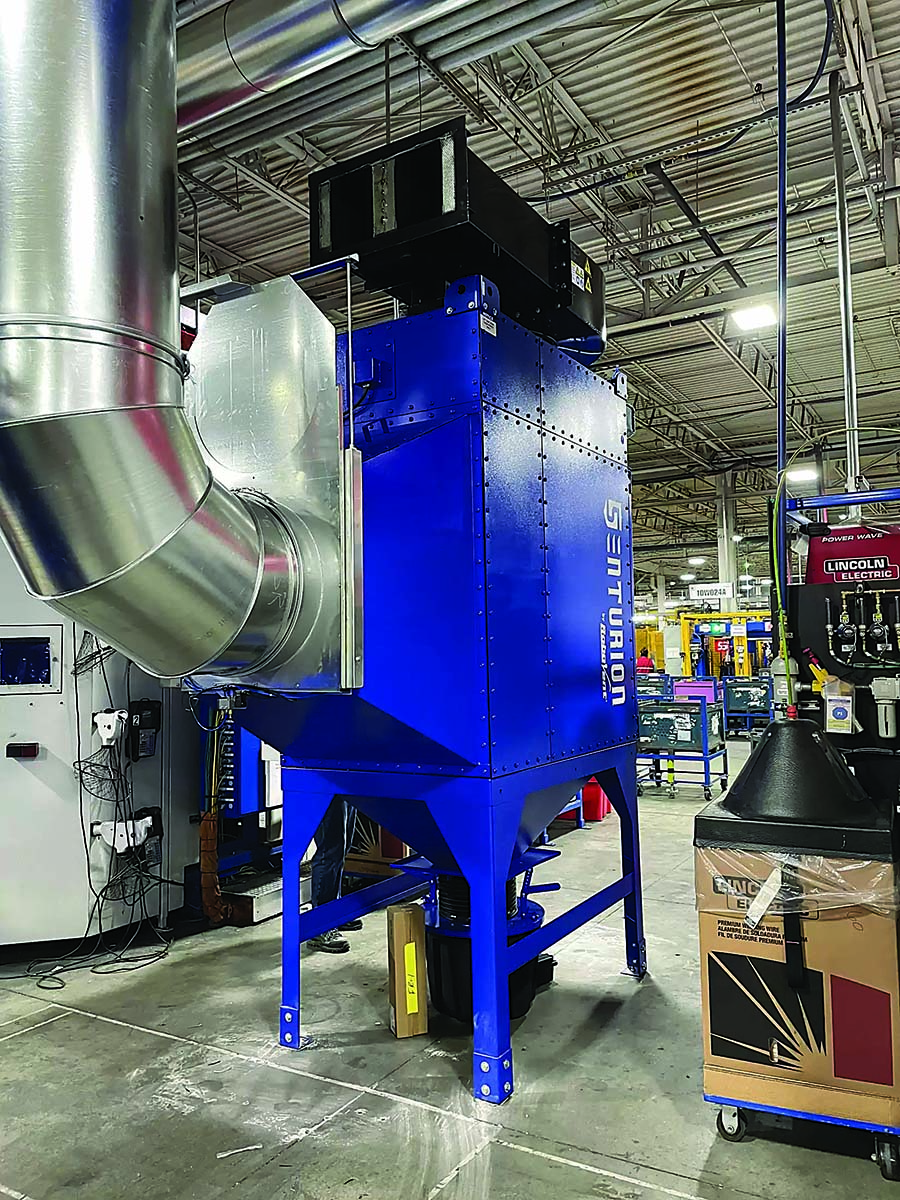
A source capture system is most effective at removing dust, fumes and aerosols from the breathing zone. Robotic turning processes should be enclosed or hooded to prevent these particulates from propagating through a facility. For manual turning, fume arms or backdraft or downdraft tables may be used.
Source capture systems should be designed to effectively capture the particulate. Ensuring that designs are close to the particulate generation point while not interfering with employee work areas is critical. Always look at the direction of particulate generation when designing an efficient system.
The source capture system should be connected to a dust collector to filter the air. If oil mists are present, the collector must be fitted with appropriate filtration for mist. If both particulate types are present, multiple filtration stages could be necessary.
Keep the area well ventilated to remove remaining solid particulates and aerosols and carry away excess heat. A makeup air system may be needed to bring fresh air back into the facility.
Personal protective equipment, such as respirators, should be used as a last resort if engineering controls like dust collection and ventilation cannot bring down particulate and aerosol concentrations in the breathing zone to acceptable levels.
Ventilation and dust collection systems should be designed using best practices laid out by ACGIH, ASHRAE and NAFA for ventilation system and air filtration system design.
Upgrading ventilation and dust collection systems protects workers and keeps facilities compliant with OSHA regulations. It is best to work with a knowledgeable engineering firm when making design decisions.
For more information about RoboVent in Sterling Heights, Michigan, call 213-682-2164 or visit www.robovent.com.
— Senior Application Engineer Mike Meyer
Related Glossary Terms
- alloys
alloys
Substances having metallic properties and being composed of two or more chemical elements of which at least one is a metal.
- fatigue
fatigue
Phenomenon leading to fracture under repeated or fluctuating stresses having a maximum value less than the tensile strength of the material. Fatigue fractures are progressive, beginning as minute cracks that grow under the action of the fluctuating stress.
- grinding
grinding
Machining operation in which material is removed from the workpiece by a powered abrasive wheel, stone, belt, paste, sheet, compound, slurry, etc. Takes various forms: surface grinding (creates flat and/or squared surfaces); cylindrical grinding (for external cylindrical and tapered shapes, fillets, undercuts, etc.); centerless grinding; chamfering; thread and form grinding; tool and cutter grinding; offhand grinding; lapping and polishing (grinding with extremely fine grits to create ultrasmooth surfaces); honing; and disc grinding.
- metalworking
metalworking
Any manufacturing process in which metal is processed or machined such that the workpiece is given a new shape. Broadly defined, the term includes processes such as design and layout, heat-treating, material handling and inspection.
- turning
turning
Workpiece is held in a chuck, mounted on a face plate or secured between centers and rotated while a cutting tool, normally a single-point tool, is fed into it along its periphery or across its end or face. Takes the form of straight turning (cutting along the periphery of the workpiece); taper turning (creating a taper); step turning (turning different-size diameters on the same work); chamfering (beveling an edge or shoulder); facing (cutting on an end); turning threads (usually external but can be internal); roughing (high-volume metal removal); and finishing (final light cuts). Performed on lathes, turning centers, chucking machines, automatic screw machines and similar machines.