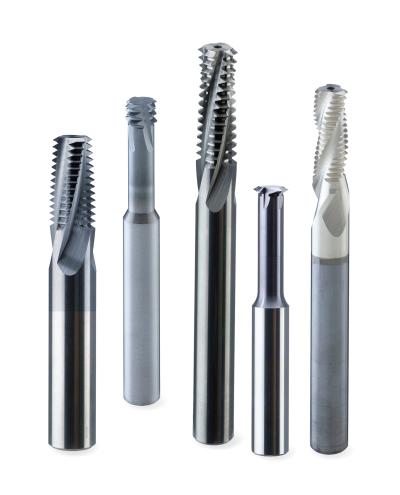
North American Tool Corp. has introduced a new line of standard solid-carbide thread mills. These thread mills feature a helical flute design and are manufactured from premium micrograin carbide for increased life and improved thread quality in a variety of materials. Straight-flute tools are available as specials.
The North American Tool thread mill line includes:
• General purpose thread mills in inch and metric sizes with bright finish or TiAlN coating;
• Coolant-through thread mills in inch and metric sizes with bright finish or TiAlN coating;
• NPT/NPTF pipe sizes with bright finish or TiAlN coating;
• Pipe sizes for exotic materials with AlCrN coating;
• Pipe sizes for aluminum with ZrN coating;
• Material-specific thread mills for exotic materials with AlCrN in inch and metric sizes;
• Material-specific thread mills for aluminum with ZrN coating in inch and metric sizes;
• Single profile (single plane) thread mills with bright and TiAlN coating for the versatility to create varying pitches with a single tool.
The new line of thread mills is available with standard sizes and features, but custom special tools can be manufactured to customer specifications.
“The demand for thread mills continues to increase,” states Phil Samuels, director of sales and marketing at North American Tool. “Applications ranging from general manufacturing, to medical parts, to energy, to aerospace, and everything in between, are looking for the efficiency and increased productivity thread milling can offer over traditional tapping in some applications. Now, North American Tool can meet and exceed the demand for efficient threading with this new line of high performance carbide thread mills.”
Contact Details
Related Glossary Terms
- gang cutting ( milling)
gang cutting ( milling)
Machining with several cutters mounted on a single arbor, generally for simultaneous cutting.
- milling
milling
Machining operation in which metal or other material is removed by applying power to a rotating cutter. In vertical milling, the cutting tool is mounted vertically on the spindle. In horizontal milling, the cutting tool is mounted horizontally, either directly on the spindle or on an arbor. Horizontal milling is further broken down into conventional milling, where the cutter rotates opposite the direction of feed, or “up” into the workpiece; and climb milling, where the cutter rotates in the direction of feed, or “down” into the workpiece. Milling operations include plane or surface milling, endmilling, facemilling, angle milling, form milling and profiling.
- milling machine ( mill)
milling machine ( mill)
Runs endmills and arbor-mounted milling cutters. Features include a head with a spindle that drives the cutters; a column, knee and table that provide motion in the three Cartesian axes; and a base that supports the components and houses the cutting-fluid pump and reservoir. The work is mounted on the table and fed into the rotating cutter or endmill to accomplish the milling steps; vertical milling machines also feed endmills into the work by means of a spindle-mounted quill. Models range from small manual machines to big bed-type and duplex mills. All take one of three basic forms: vertical, horizontal or convertible horizontal/vertical. Vertical machines may be knee-type (the table is mounted on a knee that can be elevated) or bed-type (the table is securely supported and only moves horizontally). In general, horizontal machines are bigger and more powerful, while vertical machines are lighter but more versatile and easier to set up and operate.
- tapping
tapping
Machining operation in which a tap, with teeth on its periphery, cuts internal threads in a predrilled hole having a smaller diameter than the tap diameter. Threads are formed by a combined rotary and axial-relative motion between tap and workpiece. See tap.
- threading
threading
Process of both external (e.g., thread milling) and internal (e.g., tapping, thread milling) cutting, turning and rolling of threads into particular material. Standardized specifications are available to determine the desired results of the threading process. Numerous thread-series designations are written for specific applications. Threading often is performed on a lathe. Specifications such as thread height are critical in determining the strength of the threads. The material used is taken into consideration in determining the expected results of any particular application for that threaded piece. In external threading, a calculated depth is required as well as a particular angle to the cut. To perform internal threading, the exact diameter to bore the hole is critical before threading. The threads are distinguished from one another by the amount of tolerance and/or allowance that is specified. See turning.
- titanium aluminum nitride ( TiAlN)
titanium aluminum nitride ( TiAlN)
Often used as a tool coating. AlTiN indicates the aluminum content is greater than the titanium. See coated tools.