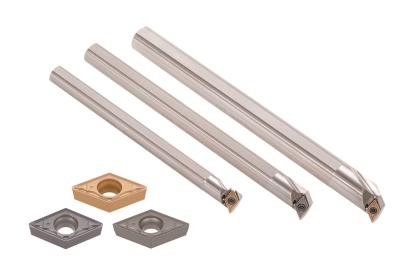
Tungaloy is introducing Premium Internal Bar – DPMT series for efficient ID turning. This new ID turning tool series reduces cutting force by 10 percent compared with conventional tools, while promising end users with machining stability and superior surface finish quality.
The new Premium Internal Bar – DPMT series offers the same proven chip evacuation capability as Tungaloy’s popular internal turning tool series – Stream Jet Bar. The new holder body is made of special alloy steel and incorporates the DPMT insert with a greater flank clearance of 11° than the conventional 7° with the DCMT style. This optimizes vibration stability as well as cutting load reduction during demanding internal boring operations. The DPMT series is a perfect tool for manufacturers who are looking for vibration dampening measures and surface finish quality improvement.
The Premium Internal Bar – DPMT series features a versatile –PS style chipbreaker with proven performance in a variety of operations, and three grades: T9215 CVD-coated grade for turning steel, NS9530 cermet grade for finish turning, and AH8015 PVD-coated grade for high temperature alloys. The new holder lineup covers working diameters ranging from 15 mm to 22 mm or from 0.6” to 0.87”, available in special alloy steel shanks, as well as carbide shanks.
Product at a Glance:
Antivibration shank thanks to the use of special alloy steel
Holder is designed for reduced cutting load as well as maximum performance at the minimum working diameter.
DPMT insert with 11° insert flank clearance offers reduced cutting load
Contact Details
Related Glossary Terms
- alloys
alloys
Substances having metallic properties and being composed of two or more chemical elements of which at least one is a metal.
- boring
boring
Enlarging a hole that already has been drilled or cored. Generally, it is an operation of truing the previously drilled hole with a single-point, lathe-type tool. Boring is essentially internal turning, in that usually a single-point cutting tool forms the internal shape. Some tools are available with two cutting edges to balance cutting forces.
- chipbreaker
chipbreaker
Groove or other tool geometry that breaks chips into small fragments as they come off the workpiece. Designed to prevent chips from becoming so long that they are difficult to control, catch in turning parts and cause safety problems.
- clearance
clearance
Space provided behind a tool’s land or relief to prevent rubbing and subsequent premature deterioration of the tool. See land; relief.
- cutting force
cutting force
Engagement of a tool’s cutting edge with a workpiece generates a cutting force. Such a cutting force combines tangential, feed and radial forces, which can be measured by a dynamometer. Of the three cutting force components, tangential force is the greatest. Tangential force generates torque and accounts for more than 95 percent of the machining power. See dynamometer.
- inner diameter ( ID)
inner diameter ( ID)
Dimension that defines the inside diameter of a cavity or hole. See OD, outer diameter.
- shank
shank
Main body of a tool; the portion of a drill or similar end-held tool that fits into a collet, chuck or similar mounting device.
- turning
turning
Workpiece is held in a chuck, mounted on a face plate or secured between centers and rotated while a cutting tool, normally a single-point tool, is fed into it along its periphery or across its end or face. Takes the form of straight turning (cutting along the periphery of the workpiece); taper turning (creating a taper); step turning (turning different-size diameters on the same work); chamfering (beveling an edge or shoulder); facing (cutting on an end); turning threads (usually external but can be internal); roughing (high-volume metal removal); and finishing (final light cuts). Performed on lathes, turning centers, chucking machines, automatic screw machines and similar machines.