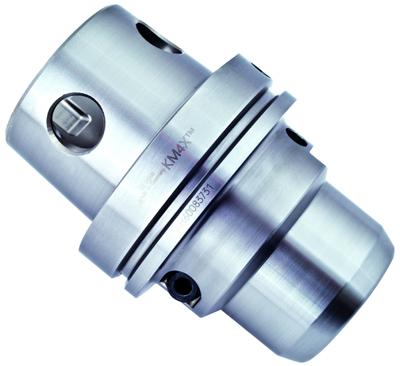
The spindle connection is the "handshake," the interface between the machine tool's spindle and toolholder. As such, this vital component has to provide the torque and bending load capacity compatible with the machine tool's operating specifications. But when machining high-strength materials like titanium and other alloys, cutting forces generate bending moments that will exceed the interface's limits prior to reaching the machine tool's torque threshold. By combining high clamping force and optimized interference levels, Kennametal says its new KM4X100 provides a robust connection, extremely high stiffness, and bending load capacity for greatly improved performance in machining high-strength alloys and other materials. The result is extremely high metal-removal rates and more completed parts per shift.
"In most cases, the tool-spindle connection determines how much material can be removed on a given operation," says Doug Ewald, director, global product management, tooling systems at Kennametal. "This is because this interface must withstand high loads and yet maintain its rigidity. With the ongoing advances in cutting tools and machining centers, a spindle connection like KM4X100 that makes the best utilization of available power possible is an important consideration to investigate early in production planning."
High-strength, lightweight materials such as titanium alloys, Inconel, and new aluminium alloys are eagerly sought by manufacturers in many industries, including aerospace and defense, energy, and transportation. These new materials present significant machining challenges in themselves. Add the competitive pressures in these global industries, and finding advanced manufacturing solutions becomes a top priority.
Machine tool builders have responded with milling and turning centers that feature improved stiffness and damping on spindles and sizable machine structures and motors, all to provide the significant horsepower, torque and thrust forces required while minimizing undesirable vibrations that deteriorate part quality and tool life.
By using three-surface contact for improved stability and optimized clamping force distribution and interference fit, KM4X100's engineering reportedly results in three times the bending moment resistant capacity compared to other tool systems.
This means:
Shops can leverage KM4X-equipped high-performance machine tools to increase speeds and feeds in difficult machining applications, thus gaining the full productivity potential from the machine tool.
Often, a smaller KM4X connection such as a KM4X100 will provide the same or better cutting performance of a larger connection.
KM4X systems can be applied on multitasking, turning, machining centers and transfer machines in manual, semiautomatic, or fully automatic mode.
Contact Details
Related Glossary Terms
- alloys
alloys
Substances having metallic properties and being composed of two or more chemical elements of which at least one is a metal.
- centers
centers
Cone-shaped pins that support a workpiece by one or two ends during machining. The centers fit into holes drilled in the workpiece ends. Centers that turn with the workpiece are called “live” centers; those that do not are called “dead” centers.
- gang cutting ( milling)
gang cutting ( milling)
Machining with several cutters mounted on a single arbor, generally for simultaneous cutting.
- milling
milling
Machining operation in which metal or other material is removed by applying power to a rotating cutter. In vertical milling, the cutting tool is mounted vertically on the spindle. In horizontal milling, the cutting tool is mounted horizontally, either directly on the spindle or on an arbor. Horizontal milling is further broken down into conventional milling, where the cutter rotates opposite the direction of feed, or “up” into the workpiece; and climb milling, where the cutter rotates in the direction of feed, or “down” into the workpiece. Milling operations include plane or surface milling, endmilling, facemilling, angle milling, form milling and profiling.
- stiffness
stiffness
1. Ability of a material or part to resist elastic deflection. 2. The rate of stress with respect to strain; the greater the stress required to produce a given strain, the stiffer the material is said to be. See dynamic stiffness; static stiffness.
- toolholder
toolholder
Secures a cutting tool during a machining operation. Basic types include block, cartridge, chuck, collet, fixed, modular, quick-change and rotating.
- turning
turning
Workpiece is held in a chuck, mounted on a face plate or secured between centers and rotated while a cutting tool, normally a single-point tool, is fed into it along its periphery or across its end or face. Takes the form of straight turning (cutting along the periphery of the workpiece); taper turning (creating a taper); step turning (turning different-size diameters on the same work); chamfering (beveling an edge or shoulder); facing (cutting on an end); turning threads (usually external but can be internal); roughing (high-volume metal removal); and finishing (final light cuts). Performed on lathes, turning centers, chucking machines, automatic screw machines and similar machines.