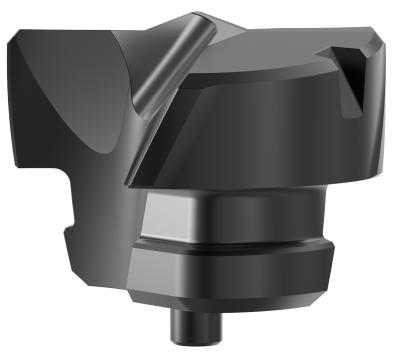
Kennametal has expanded its replaceable drill offering for KenTIP FS modular drill series with the new FEG insert for flat bottom hole applications. Applicable in steel, cast iron, and stainless steels, the FEG insert eliminates end milling operations and completes a task in a single operation, saving time and tooling costs.
Drilling flat-bottom holes is a challenge. So is drilling on inclined or curved surfaces, drilling into cross holes, drilling stacked plates, and drilling into cross holes, stacked plates and castings and other rough surfaces. Not anymore. Leveraging the success of its KenTIP FS modular drill, Kennametal has developed a unique insert geometry (FEG) that streamlines many of these types of applications and simplifies the drilling of counterbores and pilot holes as well.
“The FEG insert is so versatile, you can use it for nearly all your drilling applications”, says Georg Roth, Kennametal’s Global Product Manager of Holemaking for Modular Drilling Tools.
The newest member of the KenTIP FS family, the FEG insert eliminates the need for drilling and end milling flat bottom holes, instead completing the part in a single operation.
Get to the point
Conceptually, the FEG geometry design is simple. It features a 180° cutting edge, and a conical center point, which acts as a pilot to provide exceptional hole position and straightness. Corner chamfers serve to protect the cutting edges and reduce exits burrs. Four margin lands provide stability when breaking into interrupted cuts and cross-holes. And Kennametal's KCP15A grade uses a nano-structured AlTiN coating and fine grain carbide substrate, providing both toughness and wear resistance when drilling steel, stainless steel, and cast iron.
The diameter range covers 6.0 – 26.0 mm (0.236 - 1.024 in.) and drilling depth of up to 12xD is possible depending on the KenTIP FS modular drill body.
Contact Details
Related Glossary Terms
- flat ( screw flat)
flat ( screw flat)
Flat surface machined into the shank of a cutting tool for enhanced holding of the tool.
- gang cutting ( milling)
gang cutting ( milling)
Machining with several cutters mounted on a single arbor, generally for simultaneous cutting.
- milling
milling
Machining operation in which metal or other material is removed by applying power to a rotating cutter. In vertical milling, the cutting tool is mounted vertically on the spindle. In horizontal milling, the cutting tool is mounted horizontally, either directly on the spindle or on an arbor. Horizontal milling is further broken down into conventional milling, where the cutter rotates opposite the direction of feed, or “up” into the workpiece; and climb milling, where the cutter rotates in the direction of feed, or “down” into the workpiece. Milling operations include plane or surface milling, endmilling, facemilling, angle milling, form milling and profiling.
- stainless steels
stainless steels
Stainless steels possess high strength, heat resistance, excellent workability and erosion resistance. Four general classes have been developed to cover a range of mechanical and physical properties for particular applications. The four classes are: the austenitic types of the chromium-nickel-manganese 200 series and the chromium-nickel 300 series; the martensitic types of the chromium, hardenable 400 series; the chromium, nonhardenable 400-series ferritic types; and the precipitation-hardening type of chromium-nickel alloys with additional elements that are hardenable by solution treating and aging.
- wear resistance
wear resistance
Ability of the tool to withstand stresses that cause it to wear during cutting; an attribute linked to alloy composition, base material, thermal conditions, type of tooling and operation and other variables.