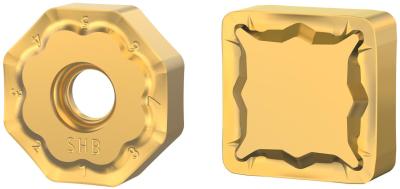
Kennametal has introduced the KCK20B and KCKP10 indexable milling grades for higher wear resistance and up to 30% longer tool life when machining cast iron and compacted graphite iron components. Both grades offer higher productivity and consistent, repeatable performance during roughing, semi-finishing, and finishing operations.
Available for many indexable milling product lines, the new grades come with a golden top layer for fast, easy wear identification, ensuring maximum tool life for each cutting edge.
“The new grades feature High-Power Impulse Magnetron Sputtering (High-PIMS) technology that provides a smoother insert surface and optimal layer adhesion for less flank wear – one of the leading causes of insert failure,” says Gil Getz, Product Manager, Kennametal. He notes that the new coating technology also increases cutting edge strength. “The result is high-performance milling in a broad range of cast iron alloys, including grey cast iron, ductile cast iron, and compacted graphite cast iron.”
KCK20B and KCKP10 are suitable for wet or dry cuts. These include rotor hubs used in windmills, pump housings, steering knuckles and gear housings for heavy equipment, and automotive components like crankshafts and cylinder heads. While KCK20B delivers higher productivity in roughing and semi-finishing operations, KCKP10 is applicable for finishing operations, but also works exceptionally well when profiling and copy milling cast iron and steels up to 45HRC.
“For customers where high tooling cost and downtime associated with tool changes are especially important, KCK20B and KCKP10 grades promise to increase tool life tremendously,” says Getz. “And for those who wish to increase throughput, the new grades deliver there as well. Either way, it is a win-win for any shop machining cast iron.”
Contact Details
Related Glossary Terms
- alloys
alloys
Substances having metallic properties and being composed of two or more chemical elements of which at least one is a metal.
- compacted graphite iron
compacted graphite iron
Cast iron having a graphite shape intermediate between the flake form typical of gray cast iron and the spherical form of fully spherulitic ductile cast iron. Also known as CG iron, CGI or vermicular iron, it is produced in a manner similar to that of ductile cast iron but using a technique that inhibits the formation of fully spherulitic graphite nodules.
- flank wear
flank wear
Reduction in clearance on the tool’s flank caused by contact with the workpiece. Ultimately causes tool failure.
- gang cutting ( milling)
gang cutting ( milling)
Machining with several cutters mounted on a single arbor, generally for simultaneous cutting.
- milling
milling
Machining operation in which metal or other material is removed by applying power to a rotating cutter. In vertical milling, the cutting tool is mounted vertically on the spindle. In horizontal milling, the cutting tool is mounted horizontally, either directly on the spindle or on an arbor. Horizontal milling is further broken down into conventional milling, where the cutter rotates opposite the direction of feed, or “up” into the workpiece; and climb milling, where the cutter rotates in the direction of feed, or “down” into the workpiece. Milling operations include plane or surface milling, endmilling, facemilling, angle milling, form milling and profiling.
- profiling
profiling
Machining vertical edges of workpieces having irregular contours; normally performed with an endmill in a vertical spindle on a milling machine or with a profiler, following a pattern. See mill, milling machine.
- wear resistance
wear resistance
Ability of the tool to withstand stresses that cause it to wear during cutting; an attribute linked to alloy composition, base material, thermal conditions, type of tooling and operation and other variables.