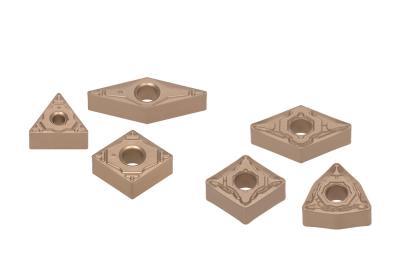
Tungaloy further expands its ISO-EcoTurn line of economical turning inserts, to include new geometries and nose radius size for precision finishing of steel.
ISO-EcoTurn inserts, while downsized for tool economy, incorporate the identical chipbreaker geometry and thickness of regular-sized inserts to maintain the same cutting performance at a depth of cut up to 3.0 mm (0.12"). Typically, when an insert is downsized, the thickness of the insert is reduced as well. However, ISO-EcoTurn inserts preserve the thickness of standard inserts in order to maintain fracture resistance. Thanks to reduced volume per insert, ISO-EcoTurn decreases cost per insert on the production line without compromising insert performance.
The new insert lines include -TSF geometry, a first choice for finishing applications; -TF geometry for precision finishing; as well as 0.2 mm nose radius size for corner accuracy.
The inserts are offered in T9215 and T9225 grades, Tungaloy’s latest CVD grade series provide exceptional wear resistance and prolonged tool life in steel turning. Combined with these T9200 series grades, this addition makes ISO-EcoTurn an ideal tool to boost productivity in a range of applications.
At a Glance
Expanded two geometries: -TSF for finishing and -TF for precision finishing
0.2 mm nose radius for added precision
Downsized inserts for economical and ecological advantages
19 new inserts to be added
Contact Details
Related Glossary Terms
- chemical vapor deposition ( CVD)
chemical vapor deposition ( CVD)
High-temperature (1,000° C or higher), atmosphere-controlled process in which a chemical reaction is induced for the purpose of depositing a coating 2µm to 12µm thick on a tool’s surface. See coated tools; PVD, physical vapor deposition.
- chipbreaker
chipbreaker
Groove or other tool geometry that breaks chips into small fragments as they come off the workpiece. Designed to prevent chips from becoming so long that they are difficult to control, catch in turning parts and cause safety problems.
- depth of cut
depth of cut
Distance between the bottom of the cut and the uncut surface of the workpiece, measured in a direction at right angles to the machined surface of the workpiece.
- turning
turning
Workpiece is held in a chuck, mounted on a face plate or secured between centers and rotated while a cutting tool, normally a single-point tool, is fed into it along its periphery or across its end or face. Takes the form of straight turning (cutting along the periphery of the workpiece); taper turning (creating a taper); step turning (turning different-size diameters on the same work); chamfering (beveling an edge or shoulder); facing (cutting on an end); turning threads (usually external but can be internal); roughing (high-volume metal removal); and finishing (final light cuts). Performed on lathes, turning centers, chucking machines, automatic screw machines and similar machines.
- wear resistance
wear resistance
Ability of the tool to withstand stresses that cause it to wear during cutting; an attribute linked to alloy composition, base material, thermal conditions, type of tooling and operation and other variables.