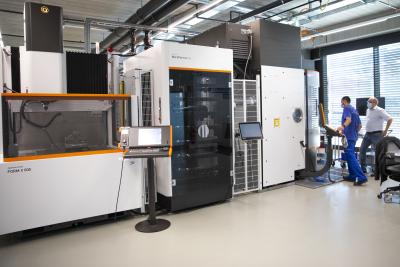
Three visionary partners – GF Machining Solutions, Fraisa and Blaser Swisslube – have teamed up to develop a new graphite machining solution. is the answer for wet-machining graphite, and it supports machining of various materials on the same machine and even in the same setup. The result is a highly efficient process that can achieve .005 tolerances while providing a healthier work environment and lower tooling costs.
Wet instead of dry? It’s a paradigm shift in moldmaking. The entire process – from electrodes right through to the finished molds – can now be performed with a single setup.
“A perfect interplay between machine, metalworking fluid, filtration, and tools,” explains Marc Blaser, CEO of Blaser Swisslube. “This combination allows for unbeatable performance and enables cost savings at the same time. The Blasogrind GTC 7 from Blaser is the ideal coolant for this application. It absorbs the graphite dust, thereby providing a much cleaner shop environment and healthier working conditions for machinists. It also optimally protects against tool wear,” he said.
Aside from the Swiss metalworking fluid manufacturer, toolmaker Fraisa and machine builder GF Machining Solutions also collaborated on the project.
“The oil film reduces the degree of contact between the graphite and the tool surface, which further increases the service life of the tool. This technology offers outstanding advantages in the form of better component quality, fewer rejects and significantly lower production costs,” explains Dr. Dirk Kammermeier, Head of Product Development at Fraisa.
Costly multi-machine operation becomes a thing of the past in cases where various electrode materials need to be processed, as does the associated laborious setup of multiple processes. In addition, considerably healthier work conditions can be achieved due to the absence of dust. Processing graphite with the right metalworking fluid is an extremely economical process that achieves higher-quality workpieces and .005 tolerances.
GF Machining Solutions also contributed to the revolutionary process. “With the most recent innovation from GF Machining Solutions, we have not only solved the problem of dust build-up, but also allows a single machine to be used for graphite, copper, and steel machining,” says Jonas Meier, Head of Center of Competence at GF Machining Solutions.
With this collaborative GR3 solution, all these materials can be machined in the same production system, without any manual intervention and with the same setup and tooling.
Tests at the in-house competence centers
The GR3 solution has been subjected to in-depth performance tests. Tests and adjustments have been performed in Blaser Swisslube’s own Technology Center in Switzerland, as well as in the metal cutting laboratories of Fraisa and GF Machining Solutions. A real component was simulated in the three competence centers, and the process was optimized to perfection. In addition to the various tool coating variants, many different cutting oils were compared against one another during rough cutting and finishing operations.
With the GR3 solution, mold makers will see longer tool life, better part finishes, optimized cycle times and substantial cost savings per machine per year.
Contact Details
Related Glossary Terms
- centers
centers
Cone-shaped pins that support a workpiece by one or two ends during machining. The centers fit into holes drilled in the workpiece ends. Centers that turn with the workpiece are called “live” centers; those that do not are called “dead” centers.
- coolant
coolant
Fluid that reduces temperature buildup at the tool/workpiece interface during machining. Normally takes the form of a liquid such as soluble or chemical mixtures (semisynthetic, synthetic) but can be pressurized air or other gas. Because of water’s ability to absorb great quantities of heat, it is widely used as a coolant and vehicle for various cutting compounds, with the water-to-compound ratio varying with the machining task. See cutting fluid; semisynthetic cutting fluid; soluble-oil cutting fluid; synthetic cutting fluid.
- metalworking
metalworking
Any manufacturing process in which metal is processed or machined such that the workpiece is given a new shape. Broadly defined, the term includes processes such as design and layout, heat-treating, material handling and inspection.