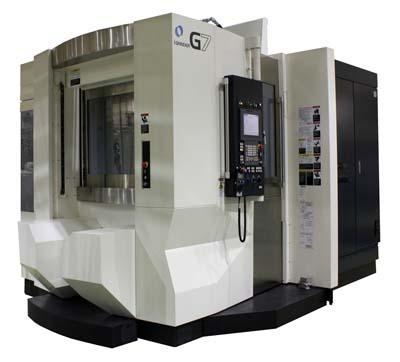
The G7 i Grinder 5-axis horizontal machining center from Makino offers a flexible, single-platform solution for grinding, drilling and milling of aerospace blades, vanes, turbine disks and other complex grinding applications. Its multifunctional configuration paired with 5-axis capabilities enables aerospace manufacturers to eliminate setups, work in process, stack-up errors, and fixture costs. It also simplifies the manufacturing process with NC-controlled intermittent dress.
"Today's capital equipment must be more flexible and capable than ever, removing non-value-added time from the manufacturing process," said David Ward, horizontal product line manager at Makino. "With the G7's capability of combined milling and grinding operations, you're not only saving on capital equipment, but you're also eliminating multiple set-up operations and work in progress times that add to your costs and lead-time."
Similar to Makino's G5 5-axis horizontal machining center, the G7 employs a 12,000-rpm HSK-63A spindle capable of handling tough-to-cut materials, such as inconel. The machine provides X-, Y- and Z-axis travels of 690mm by 650mm by 730mm, respectively, accommodating workpieces with a maximum diameter of 535mm. This ability enables machining of parts one size larger than the G5, such as super-heat-resistant jet engine parts, curvic couplings and vanes (NGV). Its infinite C-axis rotation and maximum B-axis rotation of 270 degrees offer full access to three-dimensional parts for single-setup production capabilities.
A unique two-axis Programmable Coolant Nozzle (PCN) lets the G7 accommodate variations in wheel diameter and changes in cutting direction while maintaining ideal coolant flushing conditions. It also allows for intermittent rotary dressing, an NC-controlled, electrically powered feature that trues the wheel to reestablish profile geometry on the cutting wheel. Combined use with the standard 60-tool capacity automatic tool changer enables continuous operation to be performed, maximizing throughput.
Contact Details
Related Glossary Terms
- coolant
coolant
Fluid that reduces temperature buildup at the tool/workpiece interface during machining. Normally takes the form of a liquid such as soluble or chemical mixtures (semisynthetic, synthetic) but can be pressurized air or other gas. Because of water’s ability to absorb great quantities of heat, it is widely used as a coolant and vehicle for various cutting compounds, with the water-to-compound ratio varying with the machining task. See cutting fluid; semisynthetic cutting fluid; soluble-oil cutting fluid; synthetic cutting fluid.
- dressing
dressing
Removal of undesirable materials from “loaded” grinding wheels using a single- or multi-point diamond or other tool. The process also exposes unused, sharp abrasive points. See loading; truing.
- fixture
fixture
Device, often made in-house, that holds a specific workpiece. See jig; modular fixturing.
- gang cutting ( milling)
gang cutting ( milling)
Machining with several cutters mounted on a single arbor, generally for simultaneous cutting.
- grinding
grinding
Machining operation in which material is removed from the workpiece by a powered abrasive wheel, stone, belt, paste, sheet, compound, slurry, etc. Takes various forms: surface grinding (creates flat and/or squared surfaces); cylindrical grinding (for external cylindrical and tapered shapes, fillets, undercuts, etc.); centerless grinding; chamfering; thread and form grinding; tool and cutter grinding; offhand grinding; lapping and polishing (grinding with extremely fine grits to create ultrasmooth surfaces); honing; and disc grinding.
- machining center
machining center
CNC machine tool capable of drilling, reaming, tapping, milling and boring. Normally comes with an automatic toolchanger. See automatic toolchanger.
- milling
milling
Machining operation in which metal or other material is removed by applying power to a rotating cutter. In vertical milling, the cutting tool is mounted vertically on the spindle. In horizontal milling, the cutting tool is mounted horizontally, either directly on the spindle or on an arbor. Horizontal milling is further broken down into conventional milling, where the cutter rotates opposite the direction of feed, or “up” into the workpiece; and climb milling, where the cutter rotates in the direction of feed, or “down” into the workpiece. Milling operations include plane or surface milling, endmilling, facemilling, angle milling, form milling and profiling.