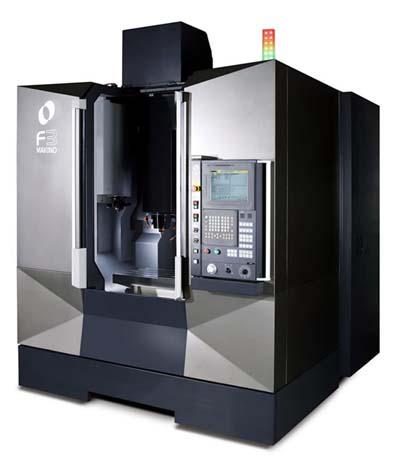
Makino Inc. announces the new F-Series vertical machining center designed to provide stiffness and rigidity for chatter-free cutting, agility for high-speed and hard milling and accuracies for tight tolerance blends and matches typical of complex, 3-D contoured geometry associated with die/mold and medical production. The machine design begins with a unique axis configuration that has no overhangs and incorporates large castings that provide a robust cutting platform. It then integrates 8mm fine-pitch ballscrews and 0.05-micron scale feedback as standard equipment. The F-Series consists of two models: the F3 and the F5. The smaller F3 features X-, Y- and Z-axis travels of 25.6", 19.7" and 17.7", respectively, a 33.5"x19.7" table and a maximum workpiece size of 33.5" long x 19.7" wide x 17.7" tall. By contrast, the larger F5 features X-, Y- and Z-axis travels of 35.4", 19.7" and 17.7", respectively, a 39.4" x 19.7" table and a maximum workpiece size of 39.4" long x 19.7" wide x 17.7" tall. Both the machines have a table load capacity of 1,432 lbs. and a 30-tool magazine provides capacity for a wide array of tooling. Included in the standard configuration of the F-Series machine is a 20,000-rpm, HSK-63A spindle which incorporates Makino's patented core-cooling, under-race and jacket spindle temperature control system. The F-Series utilizes the Makino Professional 5 Control, which affords the blend of a Windows CE graphical user interface (GUI), touch-screen selection offering instant access to information literally at your fingertip, efficient PC-like capability for data management and editing and the networking and storage capability of a data center. Also featured in the F-series is Makino's proprietary Super Geometric Intelligence (SGI.4) software developed for high-feed-rate, tight-tolerance machining of complex, 3-D, contoured shapes.
Contact Details
Related Glossary Terms
- 3-D
3-D
Way of displaying real-world objects in a natural way by showing depth, height and width. This system uses the X, Y and Z axes.
- gang cutting ( milling)
gang cutting ( milling)
Machining with several cutters mounted on a single arbor, generally for simultaneous cutting.
- machining center
machining center
CNC machine tool capable of drilling, reaming, tapping, milling and boring. Normally comes with an automatic toolchanger. See automatic toolchanger.
- milling
milling
Machining operation in which metal or other material is removed by applying power to a rotating cutter. In vertical milling, the cutting tool is mounted vertically on the spindle. In horizontal milling, the cutting tool is mounted horizontally, either directly on the spindle or on an arbor. Horizontal milling is further broken down into conventional milling, where the cutter rotates opposite the direction of feed, or “up” into the workpiece; and climb milling, where the cutter rotates in the direction of feed, or “down” into the workpiece. Milling operations include plane or surface milling, endmilling, facemilling, angle milling, form milling and profiling.
- stiffness
stiffness
1. Ability of a material or part to resist elastic deflection. 2. The rate of stress with respect to strain; the greater the stress required to produce a given strain, the stiffer the material is said to be. See dynamic stiffness; static stiffness.
- tolerance
tolerance
Minimum and maximum amount a workpiece dimension is allowed to vary from a set standard and still be acceptable.