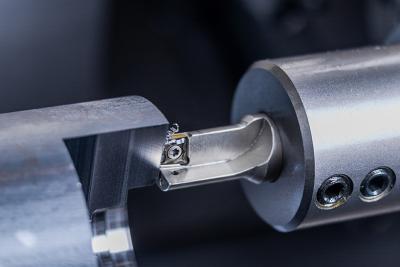
To overcome the challenges of turning and drilling steels, CERATIZIT has updated its classic EcoCut to the new EcoCut-P, and extensive tests have shown that the new inserts achieve 15% greater performance than the predecessor models. With the company’s special DRAGONSKIN coating for ISO-P materials, the inserts increase tool life and reduce machining time - thanks to the coating’s optimised layer structure.
The coating’s mechanical post-treatment induces a unique state of residual stress in the layer surface, which in turn increases process security. The DRAGONSKIN grade CTCP425-P with advanced AL2O3-TiN CVD coating is particularly well suited for when uninterrupted cuts are required. It delivers excellent wear resistance even at increased cutting speeds.
When it comes to general steel machining with interrupted cutting, the AL2O3-TiN CVD DRAGONSKIN grade CTCP435-P excels in poor machining conditions and in all applications where a high degree of toughness is required.
Contact Details
Related Glossary Terms
- chemical vapor deposition ( CVD)
chemical vapor deposition ( CVD)
High-temperature (1,000° C or higher), atmosphere-controlled process in which a chemical reaction is induced for the purpose of depositing a coating 2µm to 12µm thick on a tool’s surface. See coated tools; PVD, physical vapor deposition.
- residual stress
residual stress
Stress present in a body that is free of external forces or thermal gradients.
- turning
turning
Workpiece is held in a chuck, mounted on a face plate or secured between centers and rotated while a cutting tool, normally a single-point tool, is fed into it along its periphery or across its end or face. Takes the form of straight turning (cutting along the periphery of the workpiece); taper turning (creating a taper); step turning (turning different-size diameters on the same work); chamfering (beveling an edge or shoulder); facing (cutting on an end); turning threads (usually external but can be internal); roughing (high-volume metal removal); and finishing (final light cuts). Performed on lathes, turning centers, chucking machines, automatic screw machines and similar machines.
- wear resistance
wear resistance
Ability of the tool to withstand stresses that cause it to wear during cutting; an attribute linked to alloy composition, base material, thermal conditions, type of tooling and operation and other variables.