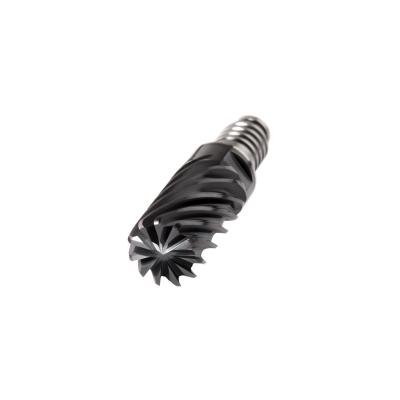
DUO-LOCK from Kennametal Inc. is a modular endmill with the performance of solid carbide. It uses a proprietary, double-cone locating surface similar to that of Kennametal’s KM or KM4X tooling design, assuring “not to exceed” radial runout values of 5 μm (.0002 in.) and Z-axis coupling repeatability of 10 μm (.0004 in.) or better. And since tool to tool repeatability of 50μm (.002 in.) is assured, there’s no need for offset adjustment or offline presetting when
changing tools. It’s also extremely rigid, with a unique and also proprietary “intelligent” coupling thread that reportedly absorbs 25 percent more torque than its nearest competitor. The result is that DUO-LOCK can take 1xD full-width slotting cuts and side milling up to 50 percent radial engagement along its entire 1.5 x D cutting length, even in titanium and similar high-strength alloys.
Thilo Mueller, manager of solid-carbide endmilling at Kennametal, says the initial release of DUO-LOCK included more than 400 line items, and that a number of small additions were made earlier this spring. This new expansion, however, more than doubles the existing cutting tip product offering.
“Last year’s IMTS presented the first wave of the HARVI endmill family, which included HARVI I, HARVI II and HARVI III geometries in diameters ranging from 0.625 in. (16 mm) up to 1.25 in. (32 mm),” says Mueller. “The new offering builds on that, with additional sizes and several completely new cutter styles. This increases DUO-LOCK’s versatility, giving even more customers an opportunity to leverage its proven strength and accuracy.”
Thanks to the following features, DUO-LOCK HARVI covers virtually any application where solid carbide is used:
-The variable HARVI helix design eliminates chatter in even the most difficult materials.
-An asymmetrical flute angle allows higher feed rates than traditional endmills.
-The eccentric flute relief offers greater edge stability with commensurately longer tool life.
-DUO-LOCK HARVI has a tapered core that provides rigidity in even the heaviest cuts
-Its specially designed axial and radial rake angles reduce tool pressure.
-Roughing and finishing can be performed with the same tool, or dedicated roughers and finishers used in the same interface.
Depending on the geometry and cutter size, 4- to 6-flute HARVI versions are available, as are several PVD-coated micrograin carbide grades. These include KCSM15, designed for titanium and other high-temp aerospace grade alloys. KCPM15, suitable for steel, stainless steel, and cast iron, and the multilayer KC643M, a go-to grade for wet-cutting a range of materials. All grades can be used to machine metals up to 52 HRC, and all are effective at reducing depth of cut notching, edge wear, and cratering in difficult materials.
So what’s been added? For one thing, DUO-LOCK modular endmills are now available in much smaller sizes, starting at 0.375 in (10 mm). Corner chamfering and rounding tools have been added to the line as well, in addition to a broad assortment of new geometries. For example, several new “corn cob” style roughers are being introduced. One has a wavy profile that creates small chips for better chip evacuation during heavy metal removal. A ballnose style rougher leverages the same geometry but is designed for 3D profiling in moldmaking and similar applications. And an “aerospace friendly” version has a unique geometry that reduces cutting forces when machining high-temp alloys, as well as corner radii that reduce chipping.
For finishing operations, Kennametal has developed a cutter with six flutes and a 45-degree helix angle similar that of the HARVI III “aerospace expansion,” but modified for better performance in steel and stainless steel. Another series has nine to 19 flutes with a higher number (depending on the diameter), and proprietary W-shaped cutting edge, and unequal flute spacing, eliminating chatter and improving surface finish in high-temp aerospace alloys, even at higher feed rates.
Finally, Kennametal has developed the MaxiMet, 2-flute and 3-flute high-shear endmills that rip through aluminum for highly productive roughing while still generating square walls and smooth floor surfaces when finishing thanks to a precision-ground wiper facet near the corner.
Kennametal is also expanding its toolholding offering with several long reach straight and conical steel shanks, which can be cut to size for your specific needs. This is in addition to the extensive assortment of HSK, PSC, CAT, DIN and BT-flange toolholders already in place.
“We see ourselves as enormously well-positioned with the HARVI family together with our new roughers, finishers, and MaxiMet expansion to meet our customers’ needs,” says Mueller.
If you’re ready to give these new cutters a try, he offers a few bits of advice. “Your arm is not a good torque wrench,” he says. “Always use our Torque Master wrench and the proper amount of torque as described in our catalog. Also, be sure to clean the threads properly before use. Before shipping, a small amount of oil is applied to each insert to prevent corrosion. This must be removed. One might assume that any toolholding mechanism should be lightly lubricated, but this is not the case with DUO-LOCK. The intelligent thread must be clean, as well as the insert locating
surfaces if the tool is to work properly. Do that and you’ll be very happy with the results.”
Contact Details
Related Glossary Terms
- alloys
alloys
Substances having metallic properties and being composed of two or more chemical elements of which at least one is a metal.
- chamfering
chamfering
Machining a bevel on a workpiece or tool; improves a tool’s entrance into the cut.
- chatter
chatter
Condition of vibration involving the machine, workpiece and cutting tool. Once this condition arises, it is often self-sustaining until the problem is corrected. Chatter can be identified when lines or grooves appear at regular intervals in the workpiece. These lines or grooves are caused by the teeth of the cutter as they vibrate in and out of the workpiece and their spacing depends on the frequency of vibration.
- cratering
cratering
Depressions formed on the face of a cutting tool caused by heat, pressure and the motion of chips moving across the tool’s surface.
- depth of cut
depth of cut
Distance between the bottom of the cut and the uncut surface of the workpiece, measured in a direction at right angles to the machined surface of the workpiece.
- endmill
endmill
Milling cutter held by its shank that cuts on its periphery and, if so configured, on its free end. Takes a variety of shapes (single- and double-end, roughing, ballnose and cup-end) and sizes (stub, medium, long and extra-long). Also comes with differing numbers of flutes.
- endmilling
endmilling
Operation in which the cutter is mounted on the machine’s spindle rather than on an arbor. Commonly associated with facing operations on a milling machine.
- feed
feed
Rate of change of position of the tool as a whole, relative to the workpiece while cutting.
- flutes
flutes
Grooves and spaces in the body of a tool that permit chip removal from, and cutting-fluid application to, the point of cut.
- gang cutting ( milling)
gang cutting ( milling)
Machining with several cutters mounted on a single arbor, generally for simultaneous cutting.
- helix angle
helix angle
Angle that the tool’s leading edge makes with the plane of its centerline.
- milling
milling
Machining operation in which metal or other material is removed by applying power to a rotating cutter. In vertical milling, the cutting tool is mounted vertically on the spindle. In horizontal milling, the cutting tool is mounted horizontally, either directly on the spindle or on an arbor. Horizontal milling is further broken down into conventional milling, where the cutter rotates opposite the direction of feed, or “up” into the workpiece; and climb milling, where the cutter rotates in the direction of feed, or “down” into the workpiece. Milling operations include plane or surface milling, endmilling, facemilling, angle milling, form milling and profiling.
- profiling
profiling
Machining vertical edges of workpieces having irregular contours; normally performed with an endmill in a vertical spindle on a milling machine or with a profiler, following a pattern. See mill, milling machine.
- radial rake
radial rake
Also known as the tool back rake, the angle between the tooth face and the radial plane through the tool point.
- rake
rake
Angle of inclination between the face of the cutting tool and the workpiece. If the face of the tool lies in a plane through the axis of the workpiece, the tool is said to have a neutral, or zero, rake. If the inclination of the tool face makes the cutting edge more acute than when the rake angle is zero, the rake is positive. If the inclination of the tool face makes the cutting edge less acute or more blunt than when the rake angle is zero, the rake is negative.
- relief
relief
Space provided behind the cutting edges to prevent rubbing. Sometimes called primary relief. Secondary relief provides additional space behind primary relief. Relief on end teeth is axial relief; relief on side teeth is peripheral relief.
- slotting
slotting
Machining, normally milling, that creates slots, grooves and similar recesses in workpieces, including T-slots and dovetails.
- wiper
wiper
Metal-removing edge on the face of a cutter that travels in a plane perpendicular to the axis. It is the edge that sweeps the machined surface. The flat should be as wide as the feed per revolution of the cutter. This allows any given insert to wipe the entire workpiece surface and impart a fine surface finish at a high feed rate.