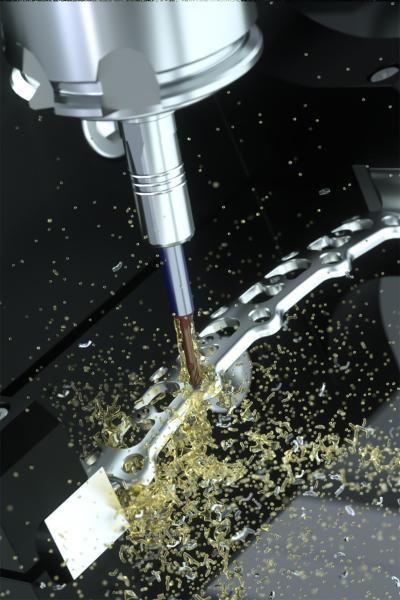
The CrazyMill Cool products have been developed by the Swiss tool manufacturer Mikron Tool for milling in small dimensions with high performance and quality. Now a new “family member” has been added. It is a four-teeth finishing milling cutter with shank integrated cooling, available in the diameter range of 1 to 8 mm und for milling depths of up to 5 diameters deep.
This milling cutter is suitable for machining all materials up to a hardness of 54 HRC. Nevertheless, this new tool has been developed focusing on stainless steels, titanium, heat-resistant alloys based on nickel and chrome-cobalt alloys.
All characteristics of the new milling tool are designed to reach high milling performance, as well as best surface quality. Primarily, this means that due to poor heat conductivity of stainless and heat-resistant materials, overheating of the tool cutting edges must be avoided. Several factors are instrumental.
Especially machining stainless and heat-resistant steels dictate that heat needs to be controlled, because it cannot be absorbed by the material and chips. The milling cutter of Mikron Tool handles this with three to five coolant ducts integrated in the tool shank. This delivers constantly a massive coolant jet directly to the milling area, independent of the work position and possible interfering edges. The tool receives continuously coolant and does not risk any overheating. Hence it is possible to simultaneously work with high speeds, feeds and working depths. This results in a high chip volume and excellent tool life.
Another advantage is the continuous flushing of chips from the milling area. This avoids a repetitive cutting up of chips and the subsequent damaging of the milled surface and in turn facilitates in conjunction with the corresponding geometry a maximal surface quality.
The geometry is entirely focused on reaching a high milling performance and surface quality. There is a flute-angle of 30º on the shorter tools (with cutting length 2 x d), whereas the longer versions (with cutting lengths 3.5 x d and 4.5 x d) have a progressive flute-angle increase from 30º into 40º. For both versions, the transition of 30º from the radius to the cylindrical section creates an optimal cutting-edge corner stability and smooth milling without vibrations.
With its four teeth, the new milling cutter is well-suited for prefinishing and fine finishing. For maximal milling performance, the manufacturer clearly defined the corresponding milling cycles and provides detailed cutting parameters. Alberto Gotti, manager of R&D at Mikron Tool, points out that the tool users often do not venture to work with high cutting parameters in the beginning and thus miss to take full advantage of the performance capacity of these tools. No need to reduce the parameters because these are all based on practical tests with corresponding materials and specific tools. Therefore, one should adhere to the indicated speeds. Slower is not safer in this case.
With the Version N (Milling depth = 4.5 x d) it is for instance possible to mill at the radius and simultaneously at the cylindrical section and, therefore, use the entire length of the tool. Especially when finishing or multipass milling with the head section, Mikron Tool recommends to work with an inclination of 15º. With this, all four cutting edges are engaged in the milling operation which results in a better surface quality. Positive experiences have been made with medical devices when milling bone plates made of titanium.
In principal, according to Gotti, with all materials an efficiency increase is possible thanks to cooling and geometry. This stands out especially when using CrazyMill Cool to machine titanium or stainless and heat-resistant materials. There are several strategies for conventional tools: Some manufacturers recommend to mill with fast feed and speed but with smaller milling path (ap), others try increased milling depths but reduce speeds and feeds. This is where the new “crazy” cutter differentiates in its use. High machining data are recommended for all parameters. An example? Prefinishing a titanium workpiece with a milling cutter 3 mm in diameter at a 150-m/min speed, feed of 0.025 mm/U and a milling path ap of 2 x d reaching with this a chip removal rate of 2,864 mm³/min and simultaneously high tool life of more than 60 m.
Two versions of the CrazyMill Cool Ball Z4 are available with especially long cutting edges. These have progressive spiral flutes (from 30º to 40º), which guarantee a vibration less milling and, thus, afford an additional improvement of the surface quality. The angle of 30º at the tip prevents a too accentuated interface between the cutting edges and the cylindrical section and, therefore, reduces the risk of cutting edge break-out. These versions are especially suitable for side milling because in one or few mill paths the entire depth can be machined. Independent of the milling width the Ra-values of the X-Axis (perpendicular to the milling direction) between 0.1 and 0.3, in the Y-Axis (along the milling direction) are in the range of 0.06 and 0.1. These are values which are usually in the range of what’s achieved with fine grinding or even ultrafine grinding.
Contact Details
Related Glossary Terms
- alloys
alloys
Substances having metallic properties and being composed of two or more chemical elements of which at least one is a metal.
- coolant
coolant
Fluid that reduces temperature buildup at the tool/workpiece interface during machining. Normally takes the form of a liquid such as soluble or chemical mixtures (semisynthetic, synthetic) but can be pressurized air or other gas. Because of water’s ability to absorb great quantities of heat, it is widely used as a coolant and vehicle for various cutting compounds, with the water-to-compound ratio varying with the machining task. See cutting fluid; semisynthetic cutting fluid; soluble-oil cutting fluid; synthetic cutting fluid.
- feed
feed
Rate of change of position of the tool as a whole, relative to the workpiece while cutting.
- flutes
flutes
Grooves and spaces in the body of a tool that permit chip removal from, and cutting-fluid application to, the point of cut.
- gang cutting ( milling)
gang cutting ( milling)
Machining with several cutters mounted on a single arbor, generally for simultaneous cutting.
- grinding
grinding
Machining operation in which material is removed from the workpiece by a powered abrasive wheel, stone, belt, paste, sheet, compound, slurry, etc. Takes various forms: surface grinding (creates flat and/or squared surfaces); cylindrical grinding (for external cylindrical and tapered shapes, fillets, undercuts, etc.); centerless grinding; chamfering; thread and form grinding; tool and cutter grinding; offhand grinding; lapping and polishing (grinding with extremely fine grits to create ultrasmooth surfaces); honing; and disc grinding.
- hardness
hardness
Hardness is a measure of the resistance of a material to surface indentation or abrasion. There is no absolute scale for hardness. In order to express hardness quantitatively, each type of test has its own scale, which defines hardness. Indentation hardness obtained through static methods is measured by Brinell, Rockwell, Vickers and Knoop tests. Hardness without indentation is measured by a dynamic method, known as the Scleroscope test.
- milling
milling
Machining operation in which metal or other material is removed by applying power to a rotating cutter. In vertical milling, the cutting tool is mounted vertically on the spindle. In horizontal milling, the cutting tool is mounted horizontally, either directly on the spindle or on an arbor. Horizontal milling is further broken down into conventional milling, where the cutter rotates opposite the direction of feed, or “up” into the workpiece; and climb milling, where the cutter rotates in the direction of feed, or “down” into the workpiece. Milling operations include plane or surface milling, endmilling, facemilling, angle milling, form milling and profiling.
- milling cutter
milling cutter
Loosely, any milling tool. Horizontal cutters take the form of plain milling cutters, plain spiral-tooth cutters, helical cutters, side-milling cutters, staggered-tooth side-milling cutters, facemilling cutters, angular cutters, double-angle cutters, convex and concave form-milling cutters, straddle-sprocket cutters, spur-gear cutters, corner-rounding cutters and slitting saws. Vertical cutters use shank-mounted cutting tools, including endmills, T-slot cutters, Woodruff keyseat cutters and dovetail cutters; these may also be used on horizontal mills. See milling.
- milling machine ( mill)
milling machine ( mill)
Runs endmills and arbor-mounted milling cutters. Features include a head with a spindle that drives the cutters; a column, knee and table that provide motion in the three Cartesian axes; and a base that supports the components and houses the cutting-fluid pump and reservoir. The work is mounted on the table and fed into the rotating cutter or endmill to accomplish the milling steps; vertical milling machines also feed endmills into the work by means of a spindle-mounted quill. Models range from small manual machines to big bed-type and duplex mills. All take one of three basic forms: vertical, horizontal or convertible horizontal/vertical. Vertical machines may be knee-type (the table is mounted on a knee that can be elevated) or bed-type (the table is securely supported and only moves horizontally). In general, horizontal machines are bigger and more powerful, while vertical machines are lighter but more versatile and easier to set up and operate.
- shank
shank
Main body of a tool; the portion of a drill or similar end-held tool that fits into a collet, chuck or similar mounting device.
- stainless steels
stainless steels
Stainless steels possess high strength, heat resistance, excellent workability and erosion resistance. Four general classes have been developed to cover a range of mechanical and physical properties for particular applications. The four classes are: the austenitic types of the chromium-nickel-manganese 200 series and the chromium-nickel 300 series; the martensitic types of the chromium, hardenable 400 series; the chromium, nonhardenable 400-series ferritic types; and the precipitation-hardening type of chromium-nickel alloys with additional elements that are hardenable by solution treating and aging.