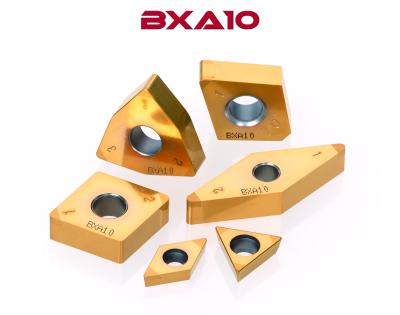
Tungaloy has announced the launch of BXA10, a new coated CBN insert grade in a tipped format for turning hardened steel parts.
BXA10 incorporates a crater-wear-resistant PcBN substrate and the latest multilayer PVD coating for edge toughness, enhancing the grade’s wear and fracture resistance. The latest development will provide improved productivity, tool life, and surface integrity in continuous to light interrupted cuts at high cutting speeds of drive shafts, gears, and other case hardened or induction hardened steel parts common in automotive industries.
The complete standard line of new BXA10 offers 278 inserts in a broad range of sizes, geometries, and unique features. Cutting edge preparations are available in five different standard options: -L, -LF, -LC, and –H in addition to the standard 0.13x25°profile, optimizing insert applications for all hard turning needs including those that require specific attention such as burr elimination or edge toughness. The inserts’ standard nose radii are available in a comprehensive lineup, including as small as 0.1 mm (.004″) radius, which is ideal for minimal undercutting operations, to the largest 2.4 mm (.094″) for high feed turning. The enhanced lineup of the new BXA10 grade CBN inserts will cover a broader spectrum of hard turning applications.
At a Glance
- Crater wear resistant PcBN substrate for process security
- Unique multilayered PVD coating technology enhances the grade’s wear resistance and edge toughness for maximum tool life
- Available in 5 different styles of edge preparations for various hard turning needs
- Available nose radii: 0.1, 0.2, 0.4, 0.8, 1.2, 1.6, 2.0, and 2.4 mm
- A total of 278 inserts are introduced
Contact Details
Related Glossary Terms
- burr
burr
Stringy portions of material formed on workpiece edges during machining. Often sharp. Can be removed with hand files, abrasive wheels or belts, wire wheels, abrasive-fiber brushes, waterjet equipment or other methods.
- cubic boron nitride ( CBN)
cubic boron nitride ( CBN)
Crystal manufactured from boron nitride under high pressure and temperature. Used to cut hard-to-machine ferrous and nickel-base materials up to 70 HRC. Second hardest material after diamond. See superabrasive tools.
- feed
feed
Rate of change of position of the tool as a whole, relative to the workpiece while cutting.
- hard turning
hard turning
Single-point cutting of a workpiece that has a hardness value higher than 45 HRC.
- physical vapor deposition ( PVD)
physical vapor deposition ( PVD)
Tool-coating process performed at low temperature (500° C), compared to chemical vapor deposition (1,000° C). Employs electric field to generate necessary heat for depositing coating on a tool’s surface. See CVD, chemical vapor deposition.
- polycrystalline cubic boron nitride ( PCBN)
polycrystalline cubic boron nitride ( PCBN)
Cutting tool material consisting of polycrystalline cubic boron nitride with a metallic or ceramic binder. PCBN is available either as a tip brazed to a carbide insert carrier or as a solid insert. Primarily used for cutting hardened ferrous alloys.
- turning
turning
Workpiece is held in a chuck, mounted on a face plate or secured between centers and rotated while a cutting tool, normally a single-point tool, is fed into it along its periphery or across its end or face. Takes the form of straight turning (cutting along the periphery of the workpiece); taper turning (creating a taper); step turning (turning different-size diameters on the same work); chamfering (beveling an edge or shoulder); facing (cutting on an end); turning threads (usually external but can be internal); roughing (high-volume metal removal); and finishing (final light cuts). Performed on lathes, turning centers, chucking machines, automatic screw machines and similar machines.
- wear resistance
wear resistance
Ability of the tool to withstand stresses that cause it to wear during cutting; an attribute linked to alloy composition, base material, thermal conditions, type of tooling and operation and other variables.