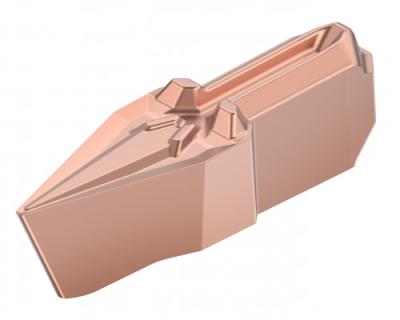
Kennametal has introduced the new Grooving Universal Positive Profiling geometry (GUP-V), expanding on its Beyond Evolution grooving & cut-off platform. With the addition of the new V- shaped single-sided insert, Beyond Evolution can cover now more applications than ever and helps to save tooling cost.
Expanding from grooving, cutoff, facing, and turning now also to profiling applications: the new Beyond Evolution GUP-V insert.
“Since the introduction of the Beyond Evolution platform, we have continued to focus on enhancing its versatility, and the new GUP-V multidirectional profiling insert is no exception says Robert Keilmann, Product Manager, Kennametal. “Together with the other insert geometries, users can now groove, cutoff, face, and turn a wide variety of materials with just a single tooling system. Simply put, when a customer adopts Beyond Evolution for their turning needs, they do not need anything else. It is that versatile.”
All Beyond Evolution insert styles feature the Triple-V Seating: Tight grip on the back (1) and top & bottom (2) provides maximum stability, especially when operating multidirectional turning and profiling.
Like all other Beyond Evolution inserts, the GUP-V profiling insert leverages a proprietary Triple-V seating design that features contact on the top, bottom, and back of the insert, providing superior rigidity that results in excellent surface finishes and dimensional accuracy while delivering the highest metal removal rates.
Contact Details
Related Glossary Terms
- cutoff
cutoff
Step that prepares a slug, blank or other workpiece for machining or other processing by separating it from the original stock. Performed on lathes, chucking machines, automatic screw machines and other turning machines. Also performed on milling machines, machining centers with slitting saws and sawing machines with cold (circular) saws, hacksaws, bandsaws or abrasive cutoff saws. See saw, sawing machine; turning.
- grooving
grooving
Machining grooves and shallow channels. Example: grooving ball-bearing raceways. Typically performed by tools that are capable of light cuts at high feed rates. Imparts high-quality finish.
- profiling
profiling
Machining vertical edges of workpieces having irregular contours; normally performed with an endmill in a vertical spindle on a milling machine or with a profiler, following a pattern. See mill, milling machine.
- turning
turning
Workpiece is held in a chuck, mounted on a face plate or secured between centers and rotated while a cutting tool, normally a single-point tool, is fed into it along its periphery or across its end or face. Takes the form of straight turning (cutting along the periphery of the workpiece); taper turning (creating a taper); step turning (turning different-size diameters on the same work); chamfering (beveling an edge or shoulder); facing (cutting on an end); turning threads (usually external but can be internal); roughing (high-volume metal removal); and finishing (final light cuts). Performed on lathes, turning centers, chucking machines, automatic screw machines and similar machines.