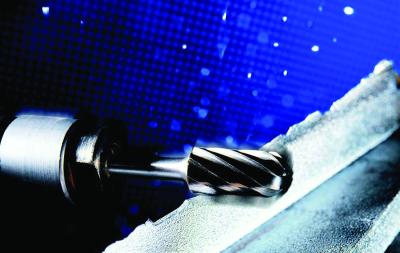
The comprehensive line of ALU/NF CUT carbide burs from PFERD reportedly brings new levels of machining performance particularly to aluminum applications. Aluminum has grown increasingly popular in industry because of its special properties, such as extreme durability, low weight, exceptional corrosion resistance and uncomplicated recycling. Processing the many different aluminum alloys, however, can be complex.
Depending on the alloy, the machinability properties can range from tough and gummy to brittle and hard. In addition, when milling aluminum, built-up edges can occur, which can cause the tool to clog up quickly.
Burs in the PFERD ALU/NF CUT range can effectively process material ranging from soft nonferrous metals, such as aluminum alloys, brass, copper or tin, to harder variants such as alloys with a high SiC content, titanium, titanium alloys and bronze.
The ALU/NF CUT family contains burs in a variety of shapes and dimensions, with shank diameters in 1/8 and 1/4 in. (3 to 6 mm), and bur diameters ranging from 01/8 to 5/8 in. (3 to 16 mm). ALU/NF CUT burs are characterized by high stock removal, long tool life, and deliver smooth milling performance. For working on softer aluminum alloys, PFERD offers a version of ALU/NF CUT called HICOAT, which has an additional coating. Thanks to antifriction properties, this coating improves chip removal significantly, increases the bur’s tool life, and delivers improved surface finishes with greatly reduced loading.
ALU/NF CUT burs with HICOAT are optimized for specific material groups, such as aluminum, of course, but also steel, stainless steel (INOX), cast iron and plastic.
Contact Details
Related Glossary Terms
- alloys
alloys
Substances having metallic properties and being composed of two or more chemical elements of which at least one is a metal.
- aluminum alloys
aluminum alloys
Aluminum containing specified quantities of alloying elements added to obtain the necessary mechanical and physical properties. Aluminum alloys are divided into two categories: wrought compositions and casting compositions. Some compositions may contain up to 10 alloying elements, but only one or two are the main alloying elements, such as copper, manganese, silicon, magnesium, zinc or tin.
- bur
bur
Tool-condition problem characterized by the adhesion of small particles of workpiece material to the cutting edge during chip removal.
- corrosion resistance
corrosion resistance
Ability of an alloy or material to withstand rust and corrosion. These are properties fostered by nickel and chromium in alloys such as stainless steel.
- gang cutting ( milling)
gang cutting ( milling)
Machining with several cutters mounted on a single arbor, generally for simultaneous cutting.
- machinability
machinability
The relative ease of machining metals and alloys.
- milling
milling
Machining operation in which metal or other material is removed by applying power to a rotating cutter. In vertical milling, the cutting tool is mounted vertically on the spindle. In horizontal milling, the cutting tool is mounted horizontally, either directly on the spindle or on an arbor. Horizontal milling is further broken down into conventional milling, where the cutter rotates opposite the direction of feed, or “up” into the workpiece; and climb milling, where the cutter rotates in the direction of feed, or “down” into the workpiece. Milling operations include plane or surface milling, endmilling, facemilling, angle milling, form milling and profiling.
- shank
shank
Main body of a tool; the portion of a drill or similar end-held tool that fits into a collet, chuck or similar mounting device.
- titanium nitride ( TiN)
titanium nitride ( TiN)
Added to titanium-carbide tooling to permit machining of hard metals at high speeds. Also used as a tool coating. See coated tools.