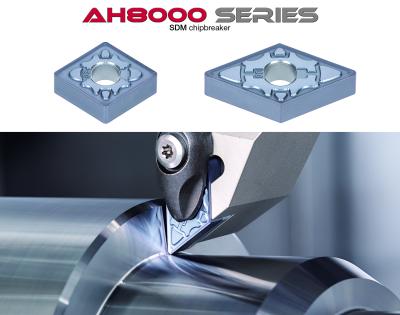
Tungaloy has expanded its AH8000 PVD-coated grade series of ISO turning inserts to include 14 new negative inserts with SDM chipbreaker.
PVD-coated insert grade series AH8000 provides proven performance in turning operations of heat resistant superalloys, which is made possible by nano-multi-layered AlTiN coating with high Al content and enhanced coating substrate adhesion. The series offers two grades: first-choice grade AH8015 is suitable from medium to finish cutting for a wide range of machining conditions; while AH8005 provides the insert with exceptional wear resistance that enables long and predictable tool life in high-speed continuous cutting operations.
SDM chipbreaker features unique T-land with variable widths and optimized rake angle that provide the insert with resistance against notch wear. Difficult metals like HRSAs are prone to cause notch wear on the insert cutting edge that can severely deteriorate insert tool life. A combination of SDM geometry and the AH8000 grade series will substantially extend tool life and provide superior predictability.
Complementing existing HRF chipbreaker for finish operations and HRM for finish to medium cutting operations, SDM further expands the application coverage of the AH8000 series, as well as contributes to customers’ machining cost reductions.
Contact Details
Related Glossary Terms
- chipbreaker
chipbreaker
Groove or other tool geometry that breaks chips into small fragments as they come off the workpiece. Designed to prevent chips from becoming so long that they are difficult to control, catch in turning parts and cause safety problems.
- rake
rake
Angle of inclination between the face of the cutting tool and the workpiece. If the face of the tool lies in a plane through the axis of the workpiece, the tool is said to have a neutral, or zero, rake. If the inclination of the tool face makes the cutting edge more acute than when the rake angle is zero, the rake is positive. If the inclination of the tool face makes the cutting edge less acute or more blunt than when the rake angle is zero, the rake is negative.
- superalloys
superalloys
Tough, difficult-to-machine alloys; includes Hastelloy, Inconel and Monel. Many are nickel-base metals.
- turning
turning
Workpiece is held in a chuck, mounted on a face plate or secured between centers and rotated while a cutting tool, normally a single-point tool, is fed into it along its periphery or across its end or face. Takes the form of straight turning (cutting along the periphery of the workpiece); taper turning (creating a taper); step turning (turning different-size diameters on the same work); chamfering (beveling an edge or shoulder); facing (cutting on an end); turning threads (usually external but can be internal); roughing (high-volume metal removal); and finishing (final light cuts). Performed on lathes, turning centers, chucking machines, automatic screw machines and similar machines.
- wear resistance
wear resistance
Ability of the tool to withstand stresses that cause it to wear during cutting; an attribute linked to alloy composition, base material, thermal conditions, type of tooling and operation and other variables.