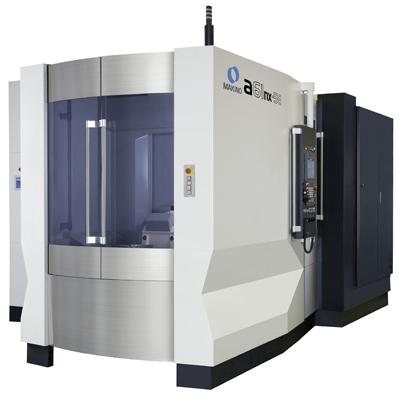
Makino is pleased to introduce the a61nx-5E, a "right-sized" 5-axis horizontal machining center for complex aluminum aerospace parts. As aerospace manufacturing continues to ramp up in North America, the a61nx-5E offers a unique and appropriately sized design for small components featuring 3-D contours, without compromising the highly productive spindle performance and 5-axis capabilities of larger aerospace machines.
"The a61nx-5E features the same robust design and proven reliability of our smaller nx-Series horizontal machining centers, but with the added speed and performance of our larger MAG-Series machines," said David Ward, Makino horizontal product line manager. "This machine differentiates itself from other similar 5-axis horizontal platforms with an innovative pallet-change system, advanced twin-direct-drive rotary table design, and availability of a high-power 24,000-rpm spindle. The result is a highly productive, right-sized solution that can provide up to 310 cubic inches of metal removal per minute."
The a61nx-5E provides enhanced rigidity through a three-point bed casting and tiered column structure. It has X-, Y- and Z-axis travels of 730mm (28.7 inches), 730mm and 680mm (26.8 inches), respectively. Linear acceleration is 1G on the X- and Y-axes, and 0.8 in the Z-axis. The direct-drive rotary tables on the a61nx-5E offer improved access to all sides of a part, especially when using shorter tools—yielding improved performance and accuracy. A closed-loop thermal management system ensures reliability and accuracy by removing heat generated by the large direct-drive rotary table motors. The a61nx-5E also uses the same proven tool magazines as the nx-Series of machines with a ring style ATC60 as standard. Optional matrix magazines with capacities of 133, 218 or 313 are available options.
The a61nx-5E comes equipped with a standard 14,000-rpm spindle with 240 Nm of duty-rated torque and 30 kW of duty-rated output. This configuration is ideal for the premium job shop needing a 5-axis platform to machine a wide variety of materials. Other spindle configurations include an optional 14,000-rpm high-torque version and a 20,000-rpm spindle for those manufacturers that need slightly more speed.
For those companies handling high-performance, high-volume aluminum machining, the a61nx-5E has the option for the new 24,000-rpm high-performance core-cooled spindle. This spindle provides up to 80 kW of duty-rated (60 kW continuous) output, delivering four to five times more metal removal per minute than typical high-speed spindles, and offering superior finishing feed rates. This high-speed spindle brings the aluminum roughing and finishing capabilities that are typically associated with Makino's much larger MAG machines into a smaller platform, enabling cycle-time reductions of 45 to 50 percent in complex parts (when compared to a typical 20,000-rpm high-speed spindle).
The a61nx-5E's innovative pallet changer eliminates material-handling challenges by enabling operator-friendly part loading and unloading via a 45-degree pivot point that transfers pallets from a vertical to horizontal orientation. The loading height is an ergonomically friendly 32 inches off of the floor, improving safety at the loading station. Workpiece limitations are a generous 600mm (23.62 inches) by 385mm (15.15 inches), accommodating easy crane clearance through the doors. For customers wishing to add automation to their 5-axis machining, this unique pallet-change system is fully compatible with the MakinommC-R robotic fixture plate distribution system.
Contact Details
Related Glossary Terms
- 3-D
3-D
Way of displaying real-world objects in a natural way by showing depth, height and width. This system uses the X, Y and Z axes.
- centers
centers
Cone-shaped pins that support a workpiece by one or two ends during machining. The centers fit into holes drilled in the workpiece ends. Centers that turn with the workpiece are called “live” centers; those that do not are called “dead” centers.
- clearance
clearance
Space provided behind a tool’s land or relief to prevent rubbing and subsequent premature deterioration of the tool. See land; relief.
- feed
feed
Rate of change of position of the tool as a whole, relative to the workpiece while cutting.
- fixture
fixture
Device, often made in-house, that holds a specific workpiece. See jig; modular fixturing.
- machining center
machining center
CNC machine tool capable of drilling, reaming, tapping, milling and boring. Normally comes with an automatic toolchanger. See automatic toolchanger.